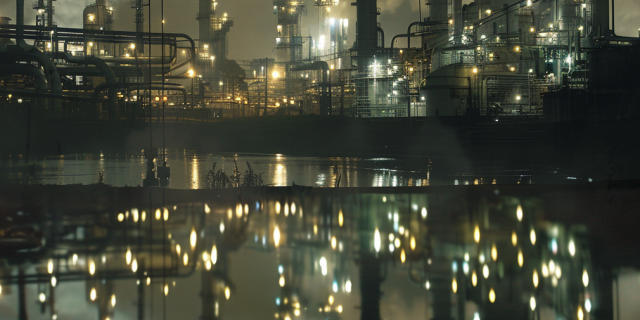
Table of contents
- The world of non-ferrous metals: diversity, application and innovation
-
Applications of non-ferrous metals
- How non-ferrous metals have revolutionized electronics
- Use of non-ferrous metals in the aerospace industry
- Importance of light metals in mechanical engineering
The world of non-ferrous metals: diversity, application and innovation
At the heart of modern technology and industry lies a group of materials whose importance and diversity are often underestimated: non-ferrous metals. These metals, which include aluminum, copper, zinc, lead, nickel and titanium, are essential building blocks for innovation and the development of new technologies due to their unique properties and wide range of applications. In the world of non-ferrous metals, extraordinary lightness meets outstanding conductivity, corrosion resistance meets high strength and the ability to withstand extreme temperatures meets extraordinary formability. These properties make non-ferrous metals an indispensable material in almost all areas of modern life.
Aluminum, known for its light weight and strength, is used in aerospace, automotive, building and construction, and packaging applications. Copper, with its unrivaled electrical conductivity, is the backbone of the electrical industry, essential for the manufacture of electrical wires, motor coils and in numerous electronic devices. Zinc protects steel from corrosion by galvanization and is also an important element in alloys and pharmaceuticals. Lead, with its high density and good formability, is used primarily in batteries, as a shielding material against radiation and in various alloys. Nickel improves the corrosion resistance and heat resistance of steel and is therefore used in food processing, the chemical industry and in batteries. Finally, titanium, known for its strength, low weight and corrosion resistance, is indispensable in aerospace, high-performance sports and medical technology.
The world of non-ferrous metals is fascinating not only because of the wide range of applications, but also because of the constant innovations that are taking place in this area. Researchers and engineers are continuously working to improve the extraction, processing and recycling methods of these metals to make them even more efficient, sustainable and cost-effective.
Applications of non-ferrous metals
Non-ferrous metals are used in a wide range of applications across many industries. Non-ferrous metals such as iron, magnesium and tin are often used as alloys to create materials with enhanced properties. Non-ferrous metals such as copper and tin are used in a wide range of applications due to their high conductivity and corrosion resistance.
Light metals such as magnesium and beryllium are often used as structural materials in the aerospace industry due to their light weight and high thermal conductivity. Pure metals such as gold and silver are used in the production of coins and jewelry. Alloys such as bronze and brass, which include copper and tin, have been used for thousands of years for a variety of purposes.
Brass is produced by alloying copper and zinc. The ratio of strength and ductility can be influenced by selecting the alloy composition. Iron is often used as a building material because it quickly forms a thin protective oxide layer that protects against corrosion. Galvanization is a process in which zinc oxide is applied to the surface of the material to protect it from corrosion.
Pure metals are designated by the chemical symbol of the base metal and the main alloying element. The alloy CuNi25Zn15 is a copper alloy, mainly known for its high conductivity and corrosion resistance.
How non-ferrous metals have revolutionized electronics
Non-ferrous metals have revolutionized the electronics industry in recent years. These non-ferrous metal-based materials offer numerous advantages over the familiar metals that do not contain iron as a main element. Since ancient times, non-ferrous metals such as manganese and precious metals have been used in various applications. They are corrosion-resistant, light metals and have good tensile strength. One example of this is red brass, a copper alloy with 25 percent zinc, which is often used for mechanical parts.
An important aspect of non-ferrous metal-based materials is their purity and alloy, which is regulated according to DIN 1700. Light metal such as aluminum, which has a positive energy balance in primary production, is malleable and reactive. When exposed to air, it forms a protective oxide layer that provides good corrosion resistance. A well-known aluminum alloy with 1 percent copper and 8 percent nickel, for example, is ideal for the construction of engineering materials and semi-finished products.
Another important aspect of non-ferrous metal is recycling. The recycling rate of non-ferrous metal is high because these metals have a lower melting point than iron. When recycling, the metals can be efficiently separated and reused. This not only reduces environmental pollution, but also saves energy compared to primary production.
Overall, non-ferrous metal-based materials have revolutionized the way electronics are manufactured. They offer a variety of advantages over conventional metals and have found wide applications in both industry and everyday life.
Use of non-ferrous metals in the aerospace industry
The aerospace industry is known for its high demands on materials that have to withstand extreme conditions such as heat, pressure and vibrations. Non-ferrous metals play a crucial role here because they have excellent mechanical properties. Modern aviation and space travel would be unthinkable without them. Non-ferrous metals, also known as non-ferrous metals, are metals that do not contain iron. They are often alloyed to improve their properties. In the aerospace industry, non-ferrous metals such as aluminum, copper, zinc and nickel are used in various applications. Aluminum, which is extracted from bauxite, is one of the most common metals used in this industry. Copper is often used in electrical systems due to its high conductivity and corrosion resistance. Zinc is used as an alloying element to increase the strength of metals. Nickel is also an important alloying element in the aerospace industry because it improves corrosion resistance. KSK GmbH uses non-ferrous metals such as nickel and zinc in alloys that are used in engine components and structural parts. These alloys are characterized by their high strength and durability, which enable them to withstand the extreme conditions in space. In foundries, non-ferrous metals are often combined with various alloying elements such as copper, zinc and nickel to produce customized materials for the aerospace industry. These alloys are specifically engineered for their desired properties such as strength, durability, and corrosion resistance. Fluxes are used to regulate the melt of non-ferrous metals and remove impurities, resulting in a consistent alloy.
Importance of light metals in mechanical engineering
The importance of light metals in mechanical engineering has increased significantly in recent years. These materials are particularly attractive for industrial applications due to their low density and high strength. It is well known that copper and Zn have been used as important materials in mechanical engineering over the centuries.
An important factor driving the use of light metals in mechanical engineering is their low weight compared to other materials. This means that components made of light metals can be manufactured more easily and efficiently, which in turn leads to higher performance. From a nickel content of 15%, they can be classified as high-performance materials.
Thanks to their high strength and resistance to corrosion and fatigue, light alloys are also ideal for use in environments with extreme conditions. Due to their versatile properties, they can be used in a wide range of applications in mechanical engineering, from aerospace to automotive.
The use of light metals in mechanical engineering will also help to reduce the industry's environmental footprint. By using lighter materials, energy savings can be achieved and CO2 emissions reduced. Overall, light metals offer a sustainable and efficient solution to the demands of modern mechanical engineering.
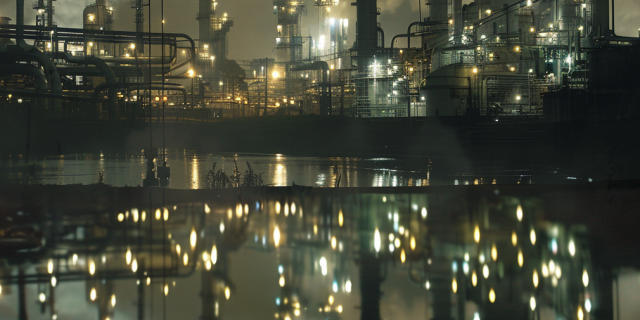
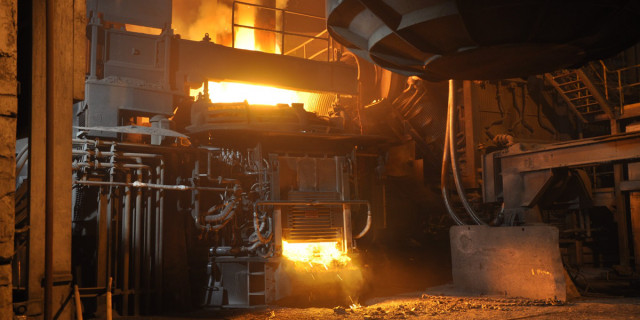
Production of Steel
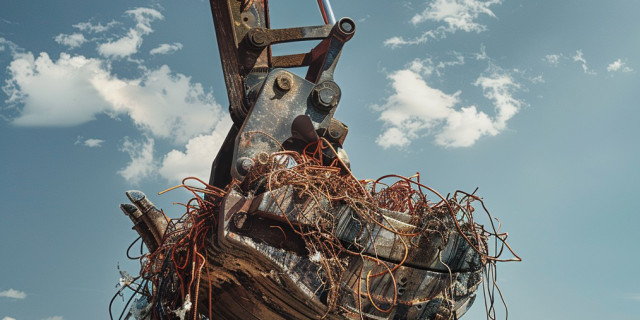
Metal recycling
Important non-ferrous metals and their properties
NF metals, also known as non-ferrous metals, play an important role in various industrial applications. An important NF metal is nickel, which is widely used due to its many positive properties. Nickel is a very durable metal that is highly resistant to heat and corrosion. These properties make it an ideal material for the production of industrial machinery and equipment that has to withstand extreme conditions. In addition, nickel is also an important component of alloys used in the aerospace and chemical industries.
Furthermore, 15 is another important non-ferrous metal used in various industries. 15, also known as RAEX, is an alloy of various metals such as chromium, molybdenum and vanadium. This alloy is characterized by its high strength, hardness and corrosion resistance. Due to these properties, 15 is widely used in the manufacture of tools, machine components and other technical applications. In addition, 15 is also used in the jewelry industry due to its beautiful silver color and durability.
The use of non-ferrous metals in various industries is due to their unique properties and advantages. These metals offer a combination of strength, hardness, corrosion resistance and other physical properties that make them an indispensable material for modern industry. The constant development of non-ferrous metals and alloys is opening up new applications in various fields, leading to continuous improvement in products and processes.
Overall, non-ferrous metals play a crucial role in modern industry and technology. Their unique properties and versatility make them indispensable materials for a wide range of applications. With constant innovation and advances in materials science, non-ferrous metals will continue to play an important role in the development of new technologies and products.
Properties and uses of copper
Copper is a highly versatile metal with various properties that make it an extremely valuable material. It has high electrical and thermal conductivity, which makes it ideal for use in electrical wiring and piping systems. In addition, copper is also corrosion resistant, which means that it retains its original shape and structure for a long time. Another advantage of copper is its aesthetics – the metallic red color adds a touch of elegance to any item.
In industry, copper is often used in alloys with other metals such as nickel to modify the properties of the material. For example, a popular alloy is brass, which is made of copper and zinc. This alloy is ideal for making musical instruments and mechanical parts due to its hardness and corrosion resistance. Another commonly used alloy is bronze, which is made of copper and tin, and is used for sculptures and jewelry.
However, the use of copper is not limited to industry. We also come into contact with copper regularly in our daily lives. Many household items, such as cooking pots and pans, are made of copper because it is an excellent heat conductor, making cooking easier and faster. Furthermore, coins are also made of copper because of its durability and resistance to wear and tear.
All in all, copper is an extremely useful and versatile metal used in various industries and applications. From electronics to the construction industry, and from art to everyday life, copper is everywhere and contributes significantly to modern society.
Aluminum: The third most abundant element in the earth's crust
Aluminum is the third most abundant element in the earth's crust and plays an important role in many areas of daily life. It is a light yet strong metal that is widely used in various industries. One of the main uses of aluminum is in the production of packaging materials, especially beverage cans. Due to its corrosion resistance and its ability to conduct heat and electricity well, aluminum is also frequently used in the electrical industry.
An interesting fact about aluminum is that it was first isolated by a German chemist, Friedrich Wöhler, in 1827. Since then, aluminum has found a wide range of applications and modern life would be unimaginable without it. In addition, aluminum is also an important material in the aerospace industry because it is lightweight and has high strength.
An interesting comparison can be drawn between aluminum and other metals, such as nickel. While nickel is only the 24th most abundant element in the earth's crust, aluminum is in third place and is therefore available in large quantities. This contributes to the fact that aluminum is of great importance both economically and ecologically.
Overall, aluminum is a versatile metal that is used in many areas and plays an important role in modern industry. Its properties, such as lightness, strength and corrosion resistance, make it an indispensable material for the manufacture of various products. Due to its frequent availability and versatile application possibilities, aluminum will continue to play an important role in industry in the future.
The versatility of zinc and its applications
Zinc is a versatile metal that can be used in a wide variety of applications. It is an element that stands out for its resistance to corrosion and is therefore often used in the manufacture of coatings and overlays. In addition, zinc is widely used in the electronics industry because it has good conductivity for electrical current. Another important aspect of zinc is its role as an alloying metal, especially when combined with nickel. This alloy, known as nickel silver, has high strength and hardness and is often used in the manufacture of jewelry, cutlery and musical equipment.
Another area in which zinc is widely used is the construction industry. Its high corrosion resistance makes it ideal for use in roof and facade systems. Zinc is also used in the production of paints and pigments because it provides good opacity and color stability. In addition, zinc is used in medicine, especially in the form of zinc oxide. This substance has anti-inflammatory and soothing properties and is often used in ointments and creams to treat skin conditions.
Zinc also plays an important role in agriculture, as it is an indispensable element for plant growth. It is often used as a fertilizer to supply the soil with essential micronutrients. In addition, zinc is used as an additive in the animal feed industry to promote the health of livestock. The versatile applications of zinc make it an indispensable element in various industries and demonstrate the importance of this metal for our modern society.
The role of alloys in industry
The role of alloys in industry is crucial as they improve the properties of metals and enable their use in various applications. One of the most well-known alloys is nickel, which is widely used in industry for its resistance to corrosion and oxidation. Adding 15 percent nickel to a metal can significantly improve its mechanical properties, making it ideal for use in high-temperature and aggressive chemical environments.
Alloys play an important role in the aerospace industry, where they are used to manufacture aircraft, missiles and satellites. In this area, alloys are particularly in demand due to their light yet strong properties. One example is the alloy Inconel, which has a high nickel and chromium content and is therefore particularly heat-resistant. This alloy is often used in aircraft engines to withstand the extreme temperatures that can occur during flight.
Alloys also play an important role in the automotive industry. By using alloys, vehicles can be made lighter and at the same time more robust. Aluminum alloys, for example, are used in car bodies to reduce weight while maintaining strength. These alloys are also corrosion resistant, making them ideal for use in various weather conditions.
In addition to improving the mechanical properties of metals, alloys also have an aesthetic function. In the jewelry industry, alloys are often used to influence the color and hardness of precious metals such as gold. By adding 15 percent of another metal such as copper or silver, different shades of gold can be created to suit the personal preferences of consumers. Thus, alloys are not only important in industry, but also in areas such as jewelry, where they help to create unique and appealing designs.
Why are copper alloys so important for industry?
Copper alloys are of great importance in industry because they have a variety of positive properties. One of the main reasons for using copper alloys is their high thermal conductivity. These alloys are widely used in applications where heat needs to be dissipated quickly and efficiently, such as in the electronics industry. Another important aspect is their good corrosion resistance, which makes them particularly suitable for applications in aggressive environments. In addition, copper alloys offer high strength and hardness, making them ideal materials for structural applications.
A particularly important component of many copper alloys is nickel. This alloy is used in a wide range of applications, including the manufacture of electrical contacts, valves and pumps. Nickel further improves the corrosion resistance of copper alloys and makes them particularly durable. In addition, nickel contributes to the strength and hardness of the alloy, making it particularly suitable for applications in the automotive and aerospace industries.
Another important aspect that makes copper alloys indispensable in industry is their good machinability. These alloys are easy to form, cut and weld, which makes them easier to process in the manufacturing industry. This makes them ideal materials for the production of components and parts in a wide range of industries.
Overall, copper alloys are essential to industry due to their versatile properties and wide range of applications. Their heat conductivity, corrosion resistance, strength, and machinability make them ideal materials for a variety of uses.
Brass and bronze: application and production
Brass and bronze are two alloys that are widely used in various industries due to their versatility and durability. Brass is mainly composed of copper and zinc, while bronze is a mixture of copper and tin. Both alloys have similar characteristics, such as a beautiful golden color and high corrosion resistance, but they differ in hardness and strength. Because of these properties, brass and bronze are widely used in the manufacture of jewelry, musical instruments and decorative objects.
However, the application of brass and bronze also extends to more technical areas such as the production of machine parts and electronic components. Due to their excellent conductivity of electricity, these alloys are often used in electrical engineering. In addition, brass and bronze also have good thermal conductivity, making them ideal materials for the production of radiators and air conditioners.
The production of brass and bronze usually involves melting copper or copper slag together with the respective alloying elements, such as zinc for brass or tin for bronze. Another important element in the production of brass and bronze is nickel, which is often added as an alloying element to increase the strength of the alloy. Typically, brass contains about 5-45% zinc and bronze about 1-15% tin, depending on the desired properties of the end product.
Overall, brass and bronze are indispensable materials in many industries due to their versatility and durability. Their application ranges from decorative items to technical components, and their production requires specialized knowledge and techniques.
Non-ferrous metals in the recycling process
Non-ferrous metals in the recycling process play an important role in the sustainable and environmentally friendly recycling of materials. Unlike ferrous metals such as steel or iron, non-ferrous metals such as nickel and 15 other metals are not attracted by magnets, which makes them difficult to separate and sort in the recycling process.
Various techniques are used to effectively recycle non-ferrous metals. One common method is to melt and compress metals into new raw materials. This process allows non-ferrous metals such as nickel to be recycled in the form of scrap or rejects without compromising the quality of the material.
Another important step in the recycling process of non-ferrous metals is the sorting and cleaning of the materials. In this process, the various metals are separated from each other and impurities such as varnish or coatings are removed. This is crucial to reintroduce high-quality recycled metals such as nickel into the production cycle.
The use of non-ferrous metals in the recycling process not only has ecological advantages, but also offers economic opportunities. By reusing metals such as nickel, resources can be saved and dependence on primary raw materials reduced. In addition, recycled metals can often be produced more cost-effectively than newly extracted materials, which is beneficial for both the environment and businesses.
Recycling aluminum and its importance for the environment
Aluminum is an extremely important raw material in modern industry. It is used for a wide range of products, from beverage cans to aircraft components. Due to its versatile use, aluminum is also a highly sought-after raw material. However, the production of new aluminum is very energy-intensive and results in high CO2 emissions. Recycling aluminum offers a sustainable alternative here.
Aluminum recycling plays a crucial role in environmental protection. In contrast to new production, up to 95% of the energy can be saved when recycling aluminum. This not only leads to a reduction in CO2 emissions, but also to a reduction in the mining of raw materials. Aluminum can be recycled almost infinitely without losing quality. This reduces the demand for new aluminum and the environmental impact of aluminum production.
The aluminum recycling process is comparatively simple and efficient. Old aluminum products are collected, melted down and processed into new products. The energy required for recycling is significantly lower than for the production of new aluminum. Thanks to the closed loop in aluminum recycling, old products can also be reintroduced into the market, which saves resources and protects the environment.
All in all, aluminum recycling is therefore of great importance for the environment. It helps to save energy, conserve resources and reduce CO2 emissions. By recycling and reusing aluminum products, we can make an important contribution to protecting the environment and promoting the sustainable use of resources. It is therefore crucial that we all do our part by disposing of aluminum products correctly and recycling them.
Increased efficiency through recycling of metals such as copper and zinc
Increasing efficiency by recycling metals such as copper and zinc is of great importance as demand for these raw materials is constantly increasing. Recycling allows valuable resources to be reclaimed and reused instead of being extracted from original ore deposits. This not only saves energy and costs, but also protects the environment, as mining ores has a significant environmental impact.
An important aspect of the efficiency gains from metal recycling is the reduction in the need for new production. By reusing existing metals, the need for resource-intensive extraction and transportation can be reduced. This leads to a decrease in CO2 emissions and thus helps to combat climate change.
Furthermore, recycling copper and zinc offers economic advantages. By reusing metals, companies can save costs and improve their profit margins. In addition, new business opportunities in the field of metal recycling are being created, leading to increased profitability and innovation.
It is therefore crucial that both companies and consumers make greater use of the recycling of metals such as copper and zinc. By working together to contribute to the circular economy, we can not only conserve resources, but also make an important contribution to environmental protection and sustainable development. It is our responsibility to drive efficiency gains through metal recycling, thus contributing to a more sustainable future.
Specific challenges and solutions in handling non-ferrous metals
Challenges: Handling non-ferrous metals, such as copper, aluminum or zinc, presents specific challenges. These metals are often not as robust as ferrous metals and can be more sensitive to certain environmental influences. In addition, they are often more susceptible to corrosion and therefore require special care and maintenance to extend their lifespan. Furthermore, non-ferrous metals are often more expensive than ferrous metals, which can make their processing and use financially challenging.
Solutions: There are various approaches to overcoming the challenges of handling non-ferrous metals. One option is to apply special coatings to non-ferrous metals to protect them from corrosion and other harmful influences. Regular inspections and maintenance can also help to extend the lifespan of non-ferrous metals and maintain their functionality. In addition, careful storage and handling of non-ferrous metals is important to avoid damage and maintain their quality. Furthermore, selecting high-quality non-ferrous metals can help to improve their robustness and longevity.
Conclusion: Handling of non-ferrous metals requires special attention and care to ensure their functionality and longevity. By using specialized coatings, regular maintenance and careful handling, the challenges of handling non-ferrous metals can be successfully overcome. In addition, the selection of high-quality non-ferrous metals is of great importance to improve their robustness and durability and to expand their range of applications.
Preventing corrosion of non-ferrous metals
Non-ferrous metals are metals that, thanks to their specific properties, are used in many different areas. One of the main problems faced by non-ferrous metals is corrosion. Corrosion can compromise the structural integrity of the metals and shorten their lifespan. Therefore, it is important to take appropriate measures to prevent corrosion in order to maintain the lifespan and performance of the non-ferrous metals.
Surface coating
One way to prevent corrosion in non-ferrous metals is to use surface coatings. These coatings serve as a protective layer that shields the metals from damaging influences such as moisture, salt, chemicals and other environmental factors. By selecting the right coating and applying it in a professional manner, the corrosion resistance of the metals can be significantly improved.
Cathodic Corrosion Protection
Another effective approach to preventing corrosion in non-ferrous metals is cathodic corrosion protection. In this process, a protective voltage is applied to the metal to protect it from corrosion. This can be achieved by sacrificial anodes or electrolysis. Cathodic corrosion protection is particularly effective in environments with high corrosion rates, such as in the maritime industry.
Corrosion inhibitors
In addition to surface coatings and cathodic protection, corrosion inhibitors can also be used to prevent corrosion in non-ferrous metals. These chemicals are introduced into the environment of the metal and inhibit the corrosion reaction. Corrosion inhibitors are an effective solution for extending the service life of non-ferrous metals and maintaining their performance.
Increasing the strength and durability of light metals
Light metals such as aluminum, magnesium and titanium are very popular in many areas due to their low density and good processability. However, they are also known for their relative softness and low strength compared to steel or other heavier metals. Therefore, a lot of research and development is being done to improve the strength and durability of these light metals.
One way to increase the strength of light metals is to form alloys. By adding certain elements such as copper, silicon or zinc, the mechanical properties of the base metal can be improved. These alloying elements can increase the strength, hardness and corrosion resistance of the light metal, making it more suitable for use in demanding applications such as aviation or the automotive industry.
Another way to improve the strength of light metals is through heat treatment. With targeted heat treatment, the internal structures of the metal can be changed, resulting in improved strength and durability. Various processes such as forging, annealing or cold forming can be used to achieve the desired mechanical properties.
In addition to alloy formation and heat treatment, modern manufacturing technologies also play an important role in increasing the strength of light metals. For example, innovative processing techniques such as injection molding, forging or additive manufacturing can be used to produce complex components made of light metals that exhibit high strength and durability. These technologies open up new possibilities for the use of light metals in various industries and applications.
Future prospects of the non-ferrous metals industry
The future prospects of the non-ferrous metals industry are both promising and challenging. The industry plays an important role in the global economy and is responsible for the production of metals such as aluminum, copper, nickel, and zinc. These metals are used in a wide range of applications, from the automotive and aerospace industries to electronics and construction. Therefore, it is crucial that the NF metals industry keeps pace with changing market conditions and technologies to remain competitive.
One important aspect influencing the future prospects of the NF metals industry is sustainability. With an increasing global demand for more environmentally friendly products and processes, the NF metals industry is expected to shift its manufacturing processes and materials to more sustainable options. This could include the development of recycling technologies, the reduction of emissions and the use of renewable energies. Companies that are able to meet these requirements could have a competitive advantage in the market.
Another important factor for the future prospects of the non-ferrous metals industry is digitalization. By implementing technologies such as artificial intelligence, big data and the Internet of Things, companies can work more efficiently and optimize their production processes. This can lead to improved quality, cost efficiency and flexibility. Companies that invest in digitalization and develop innovative solutions can strengthen their market position and develop new business opportunities.
It is clear that the future prospects of the non-ferrous metals industry depend on various factors, including sustainability, digitalization and the ability to adapt to changing market conditions.
Innovations and new applications for non-ferrous metals
Innovations and new applications for non-ferrous metals have increased significantly in recent years due to the growing demand for efficient, durable and environmentally friendly materials. NF metals, also known as non-ferrous metals, include a wide range of materials such as aluminum, copper, titanium and zinc. They are used in various industries such as automotive, electronics, aerospace and construction due to their versatile properties.
One area that offers great potential for innovation and new applications for NF metals is electric mobility. Aluminum is widely used in the production of electric vehicles due to its lightness and strength. Copper is used in the electric motors and batteries of these vehicles, while titanium is used in the production of components for high-performance batteries. These applications not only help to reduce the weight of vehicles, but also to improve their performance and range.
Other innovative applications for non-ferrous metals can be found in the aerospace industry. Aluminum alloys are used in aircraft manufacturing due to their high strength and corrosion resistance. Titanium is used for structural components and engines, while magnesium is used in lightweight components to reduce the overall weight of aircraft. These materials help to improve the efficiency and safety of aircraft.
In the construction industry, innovations and new applications for non-ferrous metals are also becoming increasingly important. Aluminum is used for facades, roofs and window frames due to its durability and resistance to weathering. Copper is used for guttering and roofing, while zinc is used for roof coverings and facade cladding. These metals not only contribute to the aesthetics of buildings, but also to increasing their sustainability and longevity.
The role of non-ferrous metals in a sustainable economy
NF metals play a crucial role in a sustainable economy. These metals, which include copper, aluminum and nickel, are essential for the production of electronics, buildings and transportation. They are durable, recyclable and offer high conductivity, making them important materials in various industries. Due to their wide range of applications, NF metals help to use resources efficiently and reduce the ecological footprint.
Copper is one of the most important non-ferrous metals, as it is widely used in the electronics and construction industries due to its high conductivity and corrosion resistance. It is used to manufacture cables, pipes and electronic components and is a sustainable material due to its recyclability. The use of copper in e-mobility and renewable energies is also driving the transition to a greener economy.
Aluminum is another non-ferrous metal that is in high demand in the transportation industry due to its light weight and corrosion resistance. It is used to manufacture car body parts, aircraft and packaging and helps to reduce fuel consumption and CO2 emissions. As aluminum is almost 100% recyclable, it also plays an important role in closing material loops and reducing waste.
Another important non-ferrous metal is nickel, which is mainly used in stainless steel production and battery manufacturing. Nickel alloys are durable and resistant to corrosion, making them ideal materials for the construction of infrastructure and industrial plants. The use of nickel in batteries for electric vehicles and stationary energy storage also supports the energy transition and reduces dependence on fossil fuels.
FAQs on non-ferrous metals
Table of contents
- Q: What are non-ferrous metals and what are they used for?
- Q: What are the special characteristics of nickel and in which areas is it used?
- Q: How is magnesium used in industry and what advantages does it offer as a construction material?
- Q: To what extent do light metals play a role in modern construction materials?
- Q: Why is lead still an important metal in certain applications despite its toxicity?
- Q: What makes a metal a preferred engineering material in industry?
- Q: How does choosing the right non-ferrous metal affect a product's lifespan and efficiency?
- Q: Why is the recyclability of non-ferrous metals an important factor in terms of environmental protection and sustainability?
Q: What are non-ferrous metals and what are they used for?
A: Non-ferrous metals, also known as non-ferrous metals, include a large group of metals that do not contain iron. They are used in various industries, such as the automotive, electronics, construction and aerospace industries, due to their properties such as corrosion resistance, thermal conductivity and low weight. Examples of non-ferrous metals include copper, aluminum, nickel, zinc, titanium, and lead. These metals have a wide range of applications, from making cables and pipes to building structures and electronic components. They are in high demand due to their versatility and durability.
Another important advantage of non-ferrous metals is their recyclability. Since they do not rust or oxidize, they can be recycled multiple times without losing quality. This makes them an environmentally friendly option at a time when sustainability is becoming increasingly important.
In summary, non-ferrous metals are indispensable in many industries due to their versatility, durability and recyclability. Their unique properties make them a valuable resource for modern society.
Q: What are the special characteristics of nickel and in which areas is it used?
A: Nickel is characterized by its high resistance to corrosion and high temperatures. It is often used in alloys to improve their strength and resilience. Nickel is used in the production of stainless steel, coins, batteries and as a catalyst in chemical processes. Nickel is also used in the electronics industry to manufacture electrical cables and contacts. It is also used in the aerospace industry for the production of engines, aircraft parts and satellites.
Another important application of nickel is in jewelry making. Nickel alloys such as white gold are popular for their durability and elegant look.
Nickel is also used in medicine, for example in dental implants, surgical instruments and medical devices.
Overall, nickel is an extremely important material in various industrial sectors due to its diverse applications and excellent properties.
Q: How is magnesium used in industry and what advantages does it offer as a construction material?
A: Magnesium is one of the lightest metals and is therefore particularly valued in the automotive and aerospace industries. As a structural material, it offers high strength at low weight, which contributes to fuel efficiency. It is also easy to machine and has good vibration damping properties. Magnesium is also widely used in the manufacture of electronic components, batteries and fireworks. It is an important component of alloys such as aluminum-magnesium alloys, which are used in a variety of applications.
In addition, magnesium plays an important role in our body. It is an essential mineral needed for many metabolic functions. Magnesium deficiency can lead to a variety of health problems, such as muscle cramps, fatigue, cardiac arrhythmias and osteoporosis.
Magnesium is taken in various forms such as magnesium oxide, magnesium chloride or magnesium citrate as a dietary supplement to meet the body's needs. It also has anti-inflammatory and soothing properties that can help treat migraines, muscle aches and sleep disorders.
Overall, magnesium is a versatile and important element that is widely used both in industry and in our bodies and can have numerous positive effects on our health and our daily lives.
Q: To what extent do light metals play a role in modern construction materials?
A: Light metals, which include aluminum, magnesium and titanium, are of great importance for modern construction materials. Their low weight combined with high strength enables innovative designs in automotive, aerospace, and machinery and equipment construction. They contribute to energy efficiency and sustainability. Light metals such as aluminum, magnesium and titanium have a significantly lower density compared to conventional materials such as steel, which makes them lighter and thus helps to reduce the overall weight of components and structures. This leads to improved energy efficiency, as less power is needed to move or transport them.
In addition, light metals are characterized by their high strength, which means that even at a low weight, they can withstand high loads and stresses. This makes it possible to produce thinner and lighter components without sacrificing stability and safety.
Light metals are therefore increasingly used in vehicle construction to reduce fuel consumption and emissions. In the aerospace industry, they help to improve the efficiency of aircraft and satellites. They are also used in complex structures in mechanical and plant engineering that have to withstand high loads.
All in all, light metals such as aluminum, magnesium and titanium are important materials for sustainable and future-oriented development in various industries. Their unique properties enable innovative solutions and help to conserve resources and reduce environmental pollution.
Q: Why is lead still an important metal in certain applications despite its toxicity?
A: Lead is still valued for its density, softness and corrosion resistance in specific areas. It is used in batteries, cable sheathing, protective layers against radiation in medical technology and as an alloying element. However, handling and processing of lead requires strict safety measures to protect health. Exposure to lead can cause serious health problems such as neurological damage, kidney damage, anemia and developmental disorders. It is therefore important to take precautions when using lead to avoid exposure.
Workers handling lead should wear personal protective equipment such as gloves, goggles and respirators to minimize contact with lead dust and particles. In addition, exposure to lead should be kept to a minimum by performing the work in well-ventilated areas and by performing regular cleaning and maintenance.
It is also important to have regular health check-ups to monitor the level of lead in the body and to detect possible health risks at an early stage. In addition, pregnant women and children should be given special protection as they are particularly vulnerable to the harmful effects of lead.
Overall, it is important to handle lead responsibly and to take all necessary safety precautions to protect the health of workers and the wider population.
Q: What makes a metal a preferred engineering material in industry?
A: A metal is preferred as an engineering material in industry because of its specific properties such as strength, ductility, corrosion resistance, heat and electricity conductivity, and workability. The selection depends on the application purpose and requirements of the respective project. Metals such as steel, aluminum, copper, nickel and titanium are commonly used in various industries, including automotive, aerospace, construction, electronics, power plants and many others. Each metal has specific properties that make it particularly suitable for certain applications.
Steel, for example, is a widely used construction material for buildings, bridges, vehicles and machines due to its high strength and hardness. Aluminum, on the other hand, is particularly popular in the aerospace and automotive industries due to its light weight. Copper is often used in the electrical industry due to its excellent electrical conductivity.
Choosing the right metal also depends on other factors such as cost, availability, environmental sustainability, and recyclability. To achieve the best results, it is important to carefully select the appropriate material according to the requirements of the respective project.
Q: How does choosing the right non-ferrous metal affect a product's lifespan and efficiency?
A: Choosing the right non-ferrous metal can significantly affect a product's lifespan and efficiency. Materials with high corrosion resistance and specific physical properties can reduce maintenance needs and improve product functionality and reliability over its entire lifespan. For example, the use of aluminum instead of steel in certain applications can reduce maintenance requirements because aluminum has a higher corrosion resistance and is therefore less prone to rust. In addition, aluminum is lighter than steel, which can lead to a weight reduction and thus lower energy consumption and costs for transport and handling.
Another example is the use of copper instead of other materials in electrical applications, as copper has high conductivity and heat resistance. This can lead to improved efficiency and reliability of electrical equipment.
It is therefore important to consider the specific requirements and conditions of the application when choosing the non-ferrous metal in order to ensure the best possible performance and service life of the product.
Q: Why is the recyclability of non-ferrous metals an important factor in terms of environmental protection and sustainability?
A: The recyclability of non-ferrous metals plays an important role in environmental protection and sustainability because recycling can significantly reduce energy consumption and CO2 emissions compared to new production. It also helps to conserve natural resources by reducing the need to mine raw materials. Recycling non-ferrous metals also helps to avoid toxic heavy metals, which are produced during the extraction and processing of primary metals. This helps to reduce the environmental impact of mining and protects human health.
Furthermore, recycling non-ferrous metals makes economic sense, as the materials can be reused, thus saving the costs of new production. In addition, recycling can create new jobs and strengthen the economy.
It is therefore important that we all contribute to recycling non-ferrous metals and thus contribute to environmental protection and sustainability. By raising awareness of the importance of recycling and using efficient recycling processes, we can make an important contribution to protecting our environment.