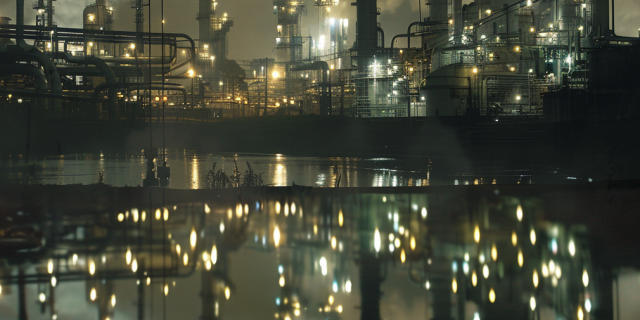
Production of steel: A comprehensive overview
Steel has been a fundamental building block of modern civilisation for centuries. From skyscrapers to cars to our kitchen appliances - steel is everywhere. But how exactly is this versatile material made? This article provides a comprehensive overview of steel production, explaining the basic steps and modern technologies, as well as the differences to other materials such as cast iron.
Table of contents
- Steel production: a comprehensive overview
-
What are the basic steps in steel production?
- The blast furnace process: from iron ore to pig iron
- From pig iron to steel: the converter process
- The role of electric arc furnaces in modern steel production
Steel production: a comprehensive overview
Steel has been a fundamental building block of modern civilization for centuries. From skyscrapers to cars to our kitchen appliances, steel is everywhere. But how exactly is this versatile material produced? This article provides a comprehensive overview of steel production, explaining the basic steps and modern technologies and highlighting the differences to other materials such as cast iron.
What are the basic steps in steel production?
The blast furnace process: from iron ore to pig iron
Steel production begins with the blast furnace process, where iron ore and coke, as almost pure carbon, are melted at temperatures of over 2000°C. The chemical reaction in the blast furnace reduces the iron ore to liquid pig iron. This process is central to steel production due to its efficiency in converting iron and coke into pig iron.
From pig iron to steel: the converter process
After the extraction of the liquid pig iron, it is passed on to the next step: the converter process. Here, the pig iron is heated and oxygen is blown in. This stage reduces the carbon content and removes other impurities such as silicon, manganese and phosphorus through oxidizing processes. The end result of this step is crude steel.
The role of electric arc furnaces in modern steel production
Electric arc furnaces provide an efficient and environmentally friendly alternative to traditional steel production. Steel scrap is melted in these furnaces by high-energy electrodes. These facilities can save twice as much energy as conventional blast furnaces and are central to steel recycling, as they facilitate the constant incorporation of scrap into steel production.
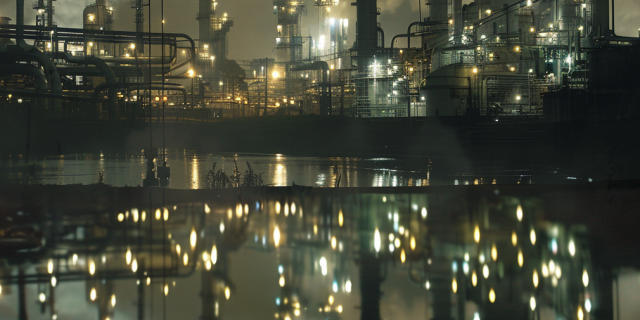
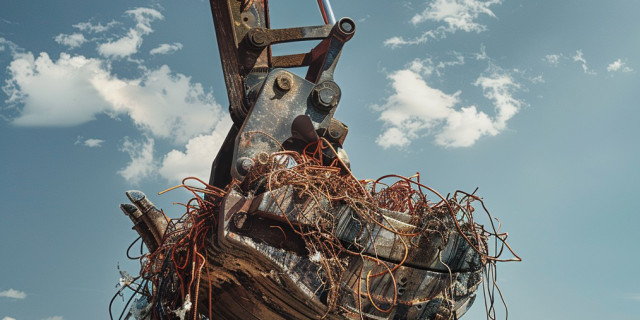
Metal recycling
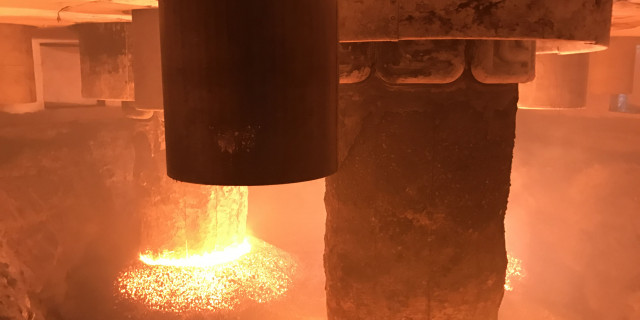
Non-ferrous metals
Why is the blast furnace central to steel production?
The chemical reactions in the blast furnace
A series of chemical reactions take place in the blast furnace that are essential for converting iron ore into liquid pig iron. Lime is added to form slag, which absorbs impurities. The reaction between iron oxide and carbon leads to the reduction of iron ore to iron and the formation of carbon monoxide and carbon dioxide as by-products.
The importance of coke and coal in the blast furnace process
Coke and coal are essential to the blast furnace process because of their high carbon content. Coke serves not only as a reducing agent, reducing iron oxide, but also as a supporting material that allows for efficient air circulation in the furnace. Without coke, the blast furnace would not be able to reach the temperatures required to convert iron ore into liquid pig iron.
Converting iron ore into liquid pig iron
The conversion of iron ore into liquid pig iron in the blast furnace is a complex process that requires high temperatures and the right mix of materials. In addition to iron ore and coke, oxygen is also added, which plays an essential role in the reduction reactions that produce the liquid pig iron.
How do alloying elements influence the properties of steel?
Chromium, nickel and carbon: small changes, big impact
Alloying elements such as chromium, nickel and carbon have a significant influence on the properties of steel. Chromium increases corrosion resistance, nickel improves toughness, and carbon content determines the hardness of steel. By precisely controlling these elements, manufacturers can customize the mechanical properties of steel as needed.
The production of stainless steel through targeted alloying
Stainless steel, known for its extraordinary resistance to corrosion, is created by adding alloying elements such as chromium and nickel to steel. Chromium forms an invisible oxide layer on the surface of the steel, protecting it from further corrosion. Nickel, in turn, gives stainless steel its characteristic toughness and makes it resistant to extreme temperatures.
Selecting alloying elements based on application
The selection of alloying elements depends heavily on the intended application of the steel. For example, high-strength structural steels require a different mix of alloying elements than steels used in corrosive seawater environments. Engineers and materials scientists work closely together to determine the right elements that provide the desired properties for specific applications.
What is the difference between cast iron and steel?
Chemical composition and its effects
The main difference between cast iron and steel lies in their carbon content. While steel typically has a carbon content of less than 2%, it can range from 2% to 4% in cast iron. This difference significantly affects the mechanical properties and machinability of the two materials.
Properties and uses of cast iron vs. steel
Cast iron, with its higher carbon content, tends to be more brittle and offers lower tensile strength than steel. However, cast iron is ideal for manufacturing complex castings due to its good castability and wear resistance. Steel, on the other hand, is used in a wider range of applications, from building structures to vehicle bodies, due to its ductility and weldability.
The role of carbon in the difference between cast iron and steel
Carbon is central to the difference in mechanical properties between cast iron and steel. In cast iron, higher carbon levels lead to the formation of graphite, resulting in the characteristic brittleness and lower melting point compared to steel, whose lower carbon levels allow for greater strength and toughness.
New technologies in steel production: how will they change steelmaking?
Electric arc furnaces: An energy-efficient alternative
Electric arc furnaces are at the center of efforts to make steel production more sustainable and energy efficient. By using mainly steel scrap as a starting material, they reduce the need for traditional pig iron production and thus reduce the carbon footprint of steel production.
The role of automation and machine learning in steel production
The use of automation and machine learning in steel production can optimize manufacturing processes, resulting in higher quality and efficiency. Sensors and algorithms continuously analyze production conditions, enabling precise real-time adjustments and reducing waste and energy consumption.
Sustainability in steel production: reducing the carbon footprint
The steel industry is facing the challenge of reducing its carbon footprint. In addition to the use of electric arc furnaces, the development of alternative methods that require less coal and coke and instead use renewable energy sources and green hydrogen is gaining importance. Such technologies could revolutionize the way steel is made and contribute to a greener future.
FAQs on the production of steel
Table of contents
- Q: What are the basic stages of steel production?
- Q: What is an electric arc furnace and how does it work in steel production?
- Q: What raw materials are used in steel production?
- Q: What are the advantages of using an electric arc furnace over traditional methods?
- Q: How is the carbon content in steel controlled and adjusted?
- Q: Why is cooling important in steel production?
- Q: What are the differences between the two types of equipment used in steel production?
- Q: How do additives such as ferroalloys influence the properties of steel?
Q: What are the basic stages of steel production?
A: Steel manufacturing usually involves three basic stages: the conversion of iron to steel in a blast furnace, which primarily uses iron ore and coke, followed by the formation of pig iron. Primary steelmaking then occurs in a converter or electric arc furnace, where inoculants such as aluminum or ferroalloys are added to influence chemical composition and mechanical properties. The final stage is the rolling and molding of the steel. The conversion of iron to steel in the blast furnace is achieved by the use of iron ore, coke and limestone. The blast furnace is heated to high temperatures to melt the iron ore and process it into a liquid pig iron. By using coke as a reducing agent, the oxygen is removed from the iron ore to obtain pure iron.
After the iron has been converted into pig iron, it is then further processed in the converter or electric arc furnace to produce steel. By adding alloying elements such as aluminum or ferroalloys, the chemical composition and mechanical properties of the steel can be specifically influenced.
The final stage of the manufacturing process is the rolling and forming of the steel. In this process, the steel is brought into the desired form, whether it is sheet metal, wire, pipe or profile. The end products are manufactured by rolling, forging or casting, and can then be further processed and used.
Overall, steel production is a complex process that requires both technical expertise and specialized equipment. Steel is an essential material in various industries and applications, from the construction industry to the automotive industry and the manufacture of household appliances.
Q: What is an electric arc furnace and how does it work in steel production?
A: An electric arc furnace is a type of smelting furnace used for steel production in which the melting process is initiated by an electric arc ignited between electrodes and scrap material. This process allows for the rapid melting of scrap metal and is widely appreciated for its flexibility and energy efficiency. Electric arc furnaces can be used in the production of both mass-produced steel and specialized alloys. The electric arc furnace works by converting electrical energy into heat energy, which is used to melt the metal. The arc is generated by the electric current flowing between the electrodes, heating the scrap material. This results in a rapid melt of the metal and allows for precise control of the process.
This type of furnace offers many advantages over conventional melting furnaces, such as higher energy efficiency, faster melting time, improved quality of the molten metal and the ability to produce different alloys. Electric arc furnaces are also more environmentally friendly, producing fewer carbon emissions and processing recycled materials more efficiently.
Overall, the electric arc furnace is a versatile tool in the steel industry, used to produce high-quality steel and alloys. Its efficiency and flexibility have led to its use in numerous production plants worldwide.
Q: What raw materials are used in steel production?
A: The main raw materials used in steel production are iron, in the form of iron ore or scrap metal, and coke, which acts as a reducing agent. Lime, aluminum and various ferro-alloys may also be added to adjust the properties of the final product. These additives help lower the melting temperature and improve the quality of the steel. The steel production process begins with the raw materials being fed into a blast furnace, where they are melted at very high temperatures. The coke serves as a reducing agent, converting the iron oxide in the iron ore into pure iron. The addition of lime forms the slag, which removes unwanted impurities from the molten iron.
After the crude steel has been obtained, it is further processed in a converter to achieve the desired carbon content and properties of the steel. Various ferroalloys such as manganese, chromium, nickel or vanadium can be added to improve the strength, hardness or corrosion resistance of the steel.
Additionally, aluminum and other alloying elements can be used to further optimize steel quality. After the desired alloy composition, the steel is cast, rolled and undergoes further processing before being made into end products such as steel beams, sheets, pipes or wires.
Q: What are the advantages of using an electric arc furnace over traditional methods?
A: Electric arc furnaces offer several advantages over traditional blast furnaces. They are able to melt steel faster and more efficiently, resulting in shorter production time. They can also be used flexibly to produce different types of steel. By using scrap metal as a raw material, they also contribute to recycling and are thus more environmentally friendly. Another advantage is that electric arc furnaces offer better temperature control, which helps to improve the quality of the molten steel. Since they are electrically operated, they are also easier to control and require less maintenance than traditional blast furnaces, which are fueled by oil or gas.
Furthermore, electric arc furnaces are able to efficiently melt even smaller quantities of steel, which is particularly advantageous for smaller manufacturers. Their compact design and flexibility also allows them to be used in a variety of production environments.
Overall, electric arc furnaces offer a variety of advantages over traditional blast furnaces and help make steel production more efficient, environmentally friendly, and flexible.
Q: How is the carbon content in steel controlled and adjusted?
A: The carbon content in steel is controlled during the melting process in the converter or electric arc furnace. By adding oxygen and other chemical additives, the excess carbon can be removed from the melt as CO2. This is a crucial step in achieving the desired mechanical properties and quality of the steel. Too much carbon in the steel can result in a brittle structure, while too little can affect strength and hardness. By precisely controlling the carbon content during the melting process, the composition of the steel can be precisely adjusted and optimized.
It is important that the carbon content in the steel is within a certain range to achieve the desired properties. Therefore, the process of controlling and adjusting the carbon content is carefully monitored and controlled. This ensures that the steel produced meets the required specifications and satisfies the requirements of the various applications.
Q: Why is cooling important in steel production?
A: Cooling plays a crucial role in the entire steelmaking process, especially after melting and during subsequent molding. Controlled cooling is necessary to achieve the desired physical properties of the steel, such as hardness. Furthermore, cooling of the equipment and facilities serves to maintain their lifespan and performance. Effective cooling is achieved through various methods such as air cooling, water mist or water cooling. The choice of cooling method depends on various factors, such as the amount of heat that needs to be removed, the type of steel and the speed of the cooling process.
An important aspect of cooling in steel production is also to avoid unwanted effects such as cracks or deformation of the steel. Through precise control of cooling, the quality of the end product can be improved and the waste of energy minimized.
In summary, cooling plays an indispensable role in steel production in achieving the desired properties of the steel, extending the service life of equipment, and increasing the efficiency of the process. Therefore, continuous monitoring and optimization of cooling is of great importance for the entire production chain.
Q: What are the differences between the two types of equipment used in steel production?
A: There are two main types of facilities used in steel production: blast furnaces and electric arc furnaces. Blast furnaces are responsible for converting iron ore into liquid pig iron by reducing ore with coke in a continuous process. Electric arc furnaces, on the other hand, melt prepared scrap metal using an electric arc. Blast furnaces are typically used for mass production, while electric arc furnaces are more flexible and can be used to produce special steel grades. The following steps are generally carried out to produce steel:
1. Reduction: iron ore or iron is reduced in a blast furnace with coke or other carbon source to produce pig iron.
2. Refinement: the pig iron is further processed by oxidation in a converter or electric arc furnace to produce steel. The desired carbon and alloy content is adjusted in the process.
3. Shaping: The liquid steel is poured into molds or shaped by rolling, forging or other processes to obtain the desired shape and dimensions.
4. Heat treatment: The steel can be further refined by various heat treatments such as hardening, tempering or annealing to achieve the desired mechanical properties.
Steel production is an energy- and resource-intensive process, but it is essential to the production of materials used in a wide range of applications, from automotive and construction to engineering and electronics. Environmentally friendly technologies and processes are continuously being developed to reduce the environmental impact of steel production.
Q: How do additives such as ferroalloys influence the properties of steel?
A: Ferro-alloys, which contain elements such as chromium, nickel and molybdenum, are added to steel during the melting process to specifically influence its properties. The addition of these alloys can improve the hardness, strength, corrosion resistance and toughness of the steel. They enable the production of steels designed for special applications, such as stainless steels. Chromium is often added to improve the corrosion resistance of steel. Nickel can increase tensile strength and improve ductility, while molybdenum can increase strength and hardness. These alloying elements are added in varying amounts depending on the desired properties of the end product.
Ferro-alloys play a vital role in steel production as they allow manufacturers to create steels with tailored properties. This enables them to meet the demands of various industries, from automotive to construction and energy production.
Overall, ferro-alloys enable the production of high-quality steels that are optimized for various applications and offer better performance and durability. The use of alloys in steel production is therefore essential to meet the diverse needs of modern industry.