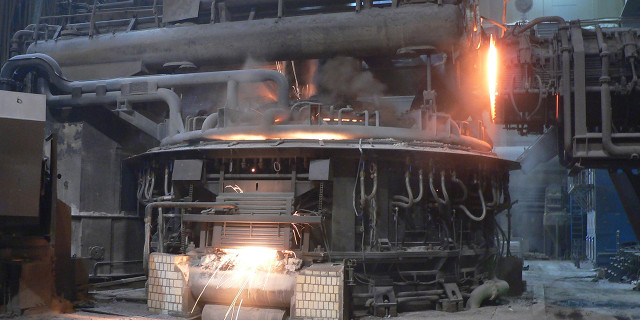
Optimized systems.
The low-maintenance water-cooled systems from KSK - Made in Germany.
Our products are welded special apparatuses that are used in energy-intensive industries whenever wearing parts of a system are exposed to hot exhaust gas, slag or liquid metal. Our designs function as heat exchangers through which water flows. In order to create optimum operating conditions for our heat exchangers in terms of process and thermal engineering, we also offer the appropriate recooling systems including waste heat recovery from a one-stop shop in our product portfolio. Our designs always stand for clarity, functionality, innovation, accuracy of fit, ease of maintenance and cost-effectiveness. Whether spare parts or complete systems - it doesn't matter. Would you like to find out more about our individual product areas or get an idea of the services we offer for our products? Then take a look here.
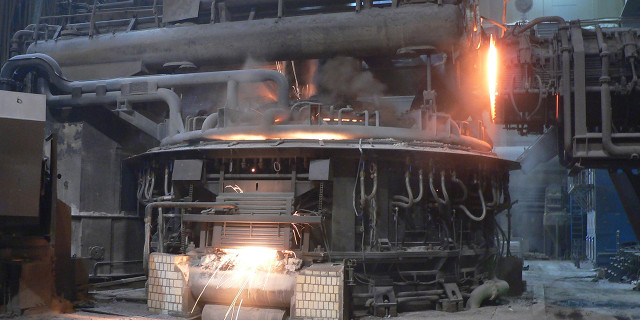
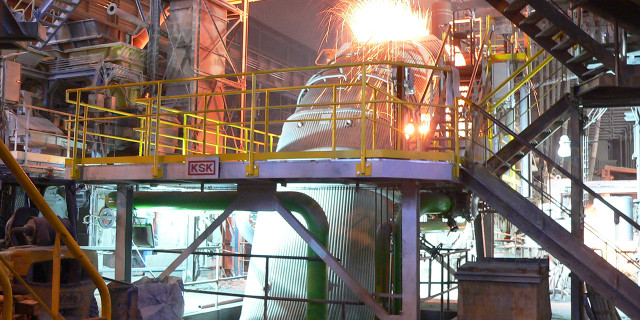
Exhaust gas cooling
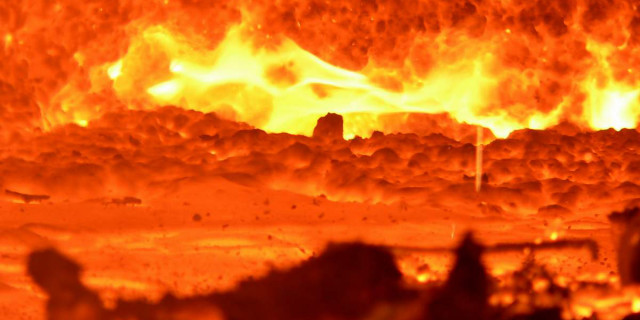
Waste heat recovery
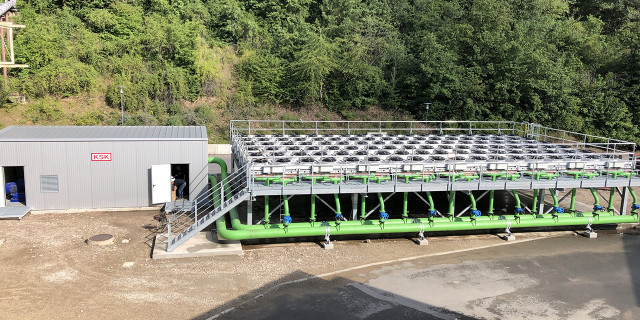
Industrial cooling
Our origins in steel production
The origins of KSK can be found in steel production, more precisely in steel production in electric arc furnaces. This is where our water-cooled special apparatuses were first used as parts of furnace vessels.
When steel is produced in an electric arc furnace, the heat required for melting is generated by the electric arc. The electric arc furnace is charged with scrap, sponge iron and molten iron to produce steel. Lime is also added to produce slag and reducing agents. The arc created from the graphite electrodes to the molten material during steel production can generate temperatures of up to 3500 °C. For this reason, low-melting alloying elements such as tungsten and molybdenum can also be melted into iron alloys using this type of steel production. All steel grades can be produced in electric arc furnaces.
Over the years, we have been able to further develop ourselves and our products so that they are now also used in other steel production processes, such as LD converters.
In the Linz-Donawitz (LD) process, oxygen is blown through a lance into the molten bath in the converter to produce steel. In this way, unwanted by-products are oxidized during steel production and can then be tapped off as slag. By adding scrap and ore, the use of pig iron in this type of steel production can be reduced and the molten metal cooled. Liquid pig iron must be loaded into the converter to produce steel, as the process cannot melt the input material. Finished steel is extracted from the plant by tilting the converter.
The resulting exhaust gases (approx. 1,700 C) are collected and cooled in a tubular converter chimney. This is how waste heat is generated during steel production. In our waste gas cooling systems for steel production using the LD process, this waste heat is converted into steam and thus made available for further use.
This steel production process is named after the Linz and Donawitz sites of the two Austrian companies VÖEST and Alpine Montan (later voestalpine), which developed this steel production process. There are now many variations of the LD process in which oxygen and then argon are simultaneously introduced through the bottom vent.
The two steel production processes described above are often followed by secondary metallurgical treatment in steel production. For example, steel grades can be further alloyed and refined in a ladle furnace or a vacuum furnace. Our water-cooled components have also been used in this form of steel production for more than 20 years.
Applications in other melting processes
The more we continued to develop our technology, the more we were able to use our water-cooled components in melting processes outside of pure steel production. Similar to steel production, a long service life of wear parts is often decisive for the economic success of a system. We are now also developing low-maintenance furnace vessels and lid or ceiling constructions and exhaust gas cooling systems for shaft furnaces, resistance melting furnaces, rotary kilns and many more.
Cooling Systems
In addition to pure water-cooled components for steel production or other melting processes, we are also able to supply complete recooling systems. An equally trouble-free and low-maintenance cooling circuit is crucial for trouble-free steel production. KSK's cooling systems are generally designed as closed circuits. We develop and manufacture the necessary pump stations, including automation and control cabinet technology, in-house. The circuits themselves always safely cool the heat generated in our water-cooled components during steel production. The waste heat can also be recovered for use in other processes. Nevertheless, our cooling systems in steel production are often also equipped with a dry cooler. It efficiently dissipates the heat generated during steel production to the ambient air without any loss of water or the use of biocides.