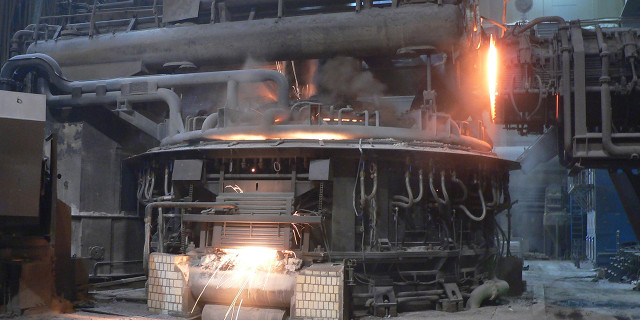
Table of contents
- Industrial cooling: Efficient cooling systems and technologies in industry
-
What can KSK do for you in the field of industrial cooling?
- Closed cooling circuits.
- Industry-independent industrial cooling.
- Hidden potential.
- Benefit from an outside perspective.
- Your point of contact
Industrial cooling: Efficient cooling systems and technologies in industry
Industrial cooling plays a crucial role in many industries, ensuring the efficiency and reliability of industrial processes. The importance of industrial cooling cannot be overstated, as it helps to optimize production and reduce operating costs. In this article, we will explore the basics of industrial cooling, the different types of cooling systems, and the latest technologies and solutions that contribute to energy efficiency and cost reduction.
What can KSK do for you in the field of industrial cooling?
Closed cooling circuits.
Water-cooled components in melting and recycling plants should be in operation for as long as possible and without maintenance. One of the keys to success is a well-functioning re-cooling system that is specially adapted to the plant. The systems we plan are preferably designed as closed cooling circuits, in order to be able to guarantee optimum monitoring (leaks, temperatures, flows, etc.) and control. Furthermore, closed cooling circuits with dry coolers have the advantage over evaporative coolers of not falling under the provisions of the 42nd BImSchV. Biocides, corrosion inhibitors and other chemicals are thus a thing of the past.
Industry-independent industrial cooling.
Our roots are in the steel industry, but our expertise is not limited to it. Based on our experience, we are accustomed to designing and developing process-safe and continuously running systems for industrial cooling. Many principles, procedures, calculations and manufacturing processes can therefore be adapted to systems in a wide range of production plants with a need for recooling.
Are you looking for a planning office that can electrically and mechanically manufacture and deliver your new, individually developed and ready-to-use plug-and-play pump station to your company? Or are you currently simply unsure why your currently installed recooling system overheats regularly? Please do not hesitate to contact us.
Hidden potential.
Optimizing, improving, expanding or redesigning a cooling system or component requires a careful analysis of the status quo, taking into account all other external factors and implementation requirements. Our responsible project engineers will be happy to work with you on-site to get a picture of the situation directly at the plant. We then analyze process parameters, drawings, documentation, worn materials and all other relevant information with a trained eye. The results of such an analysis may include, for example, a heat balance, furnace stoichiometry, process engineering instructions with piping and instrumentation flow diagrams, layout drawings or even a material inspection report.
Benefit from an outside perspective.
This foundation enables us to show you the hidden potential that your plant may still have or where we see a specific need for action. Benefit from the (external) view of our experts and from stimulating discussions on an interdisciplinary basis. Gain planning security for all further project steps and valuable time through targeted budget planning.
Your point of contact
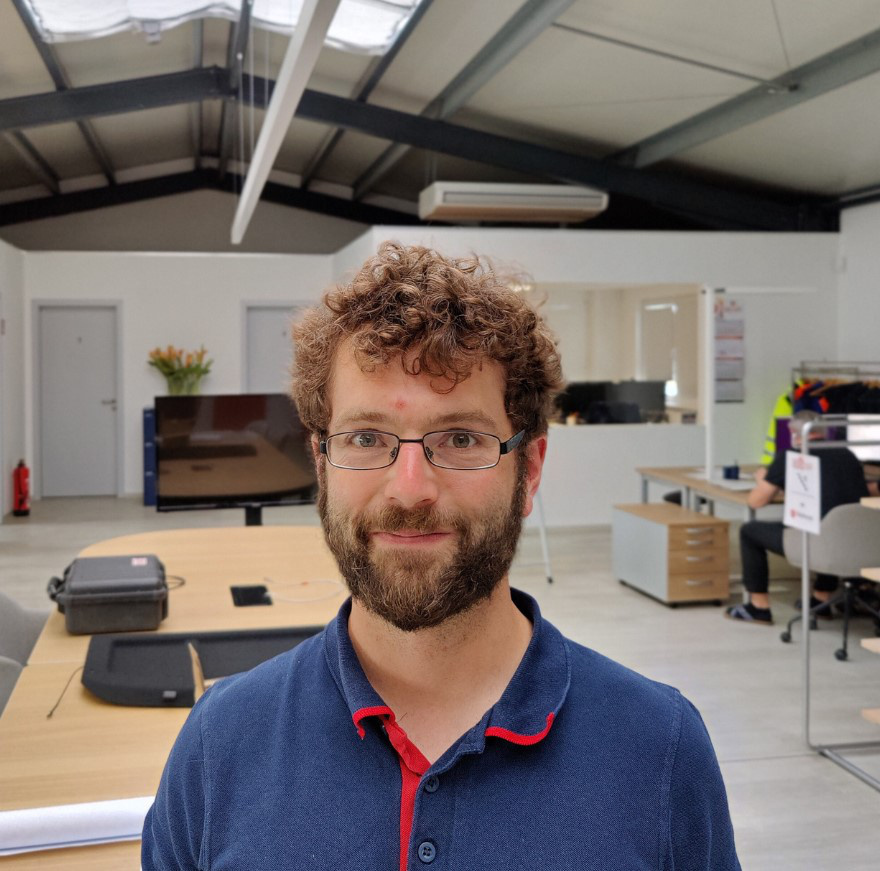
M.eng. Florian Röhl
Project Engineer
+49 (0) 2364 10539-22
The six KSK quality criteria for our recooling systems.
Clarity
You can't find your way around the pump station of your electric arc furnace? Even looking at the operating instructions doesn't help? Perhaps at this point you are also thinking: What, which operating instructions? Even if it's sometimes just something simple like the documentation: clear and understandable layouts, illustrations and instructions can make work a lot easier at the end of the day, right?
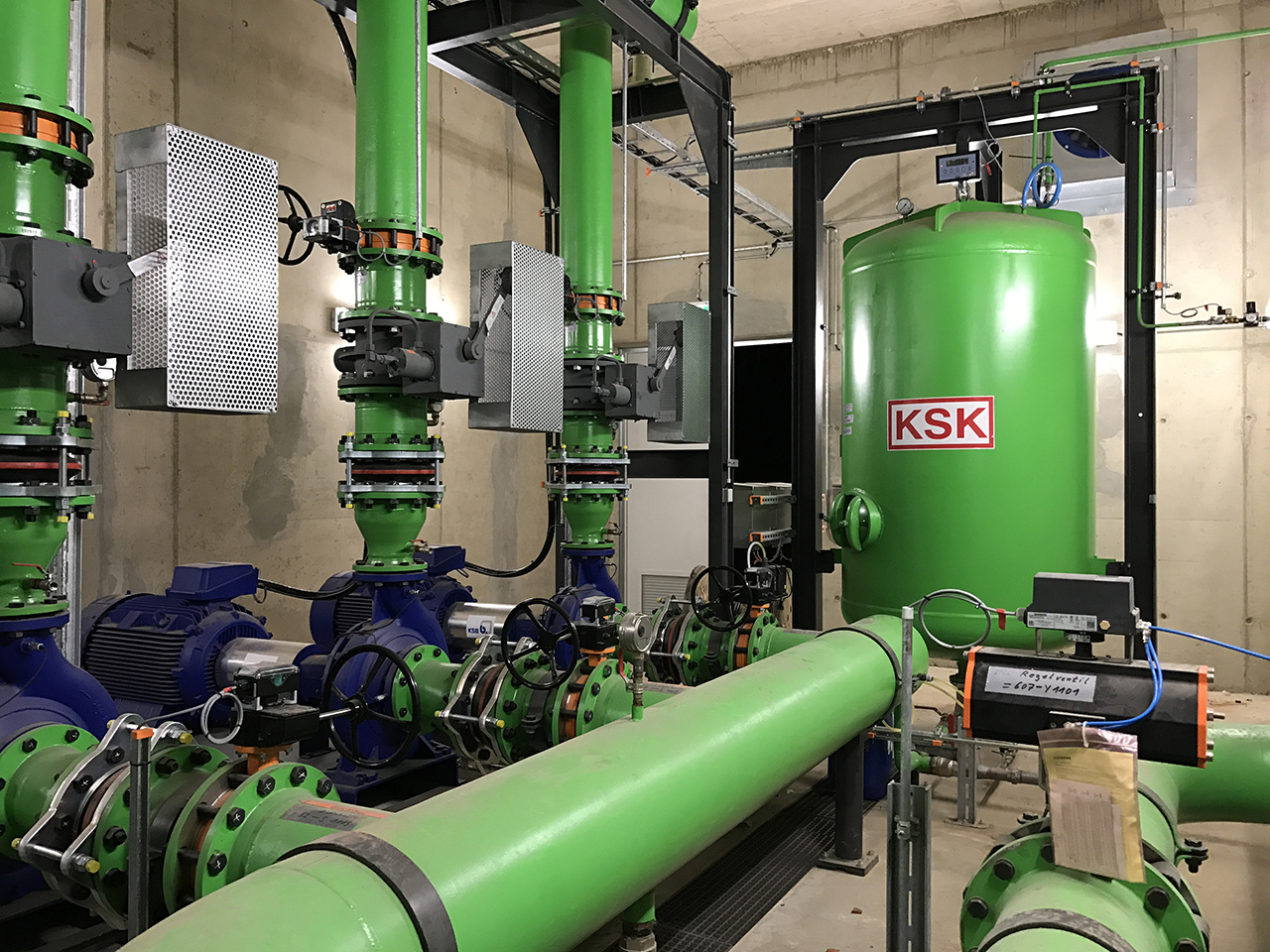
Functional
A modern cooling circuit should be able to do more than just cool. Much more! Does your current cooling circuit only detect the leakage at the electric arc furnace when you can already see a plume of steam? Does the flow temperature in your hot gas line control climate change and not you on the control panel in the pump station? Then we should talk.
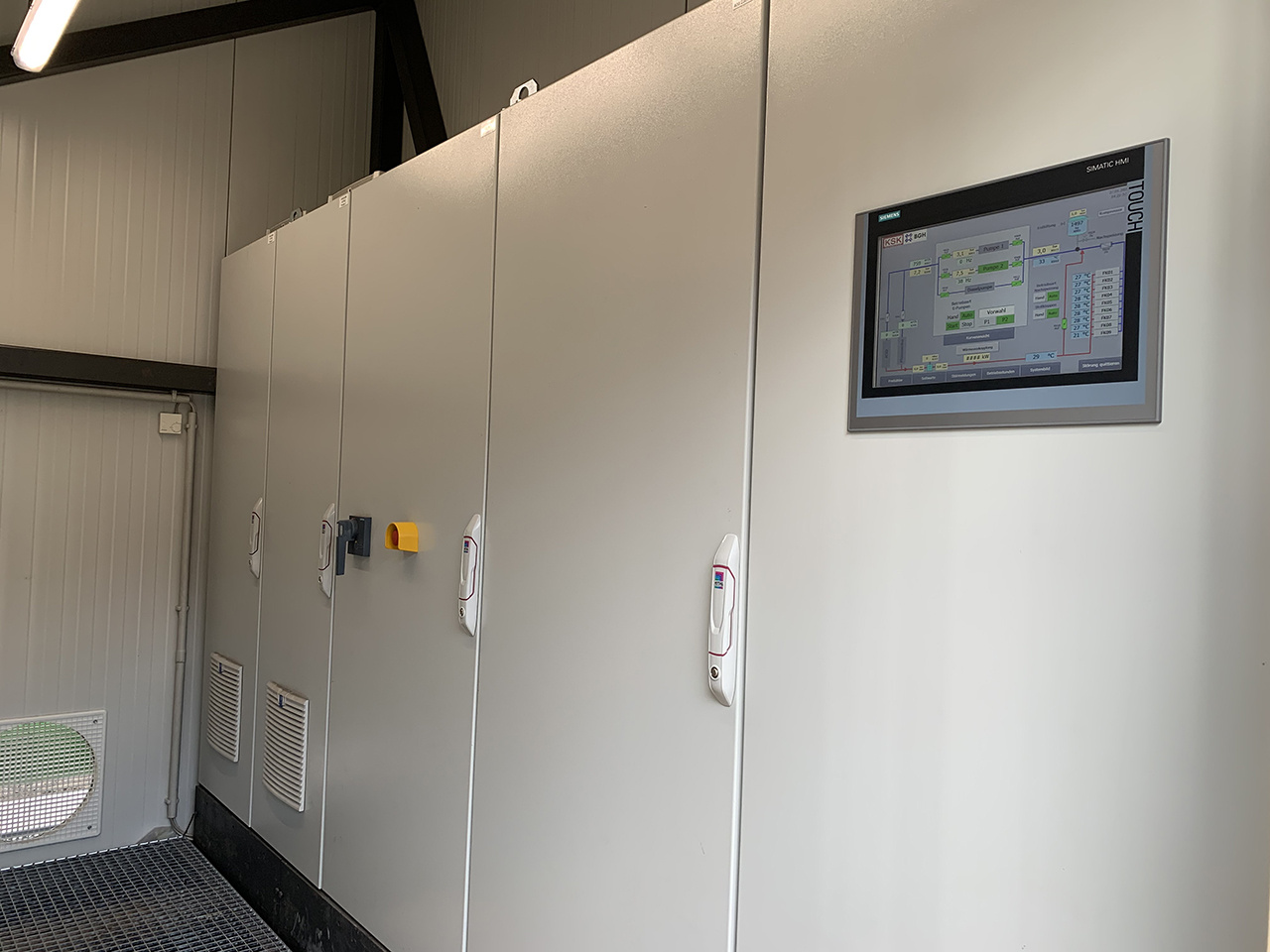
Perfect fit
Every unit to be cooled is different, and every customer has their own ideas. Of course, every cooling circuit we design is a customized one-off. We always remain true to our basic design, but whether we should integrate a diesel pump or a city water pipe for emergency cooling is up to you. And even if there is less space available for your new pump station: We will find a solution.
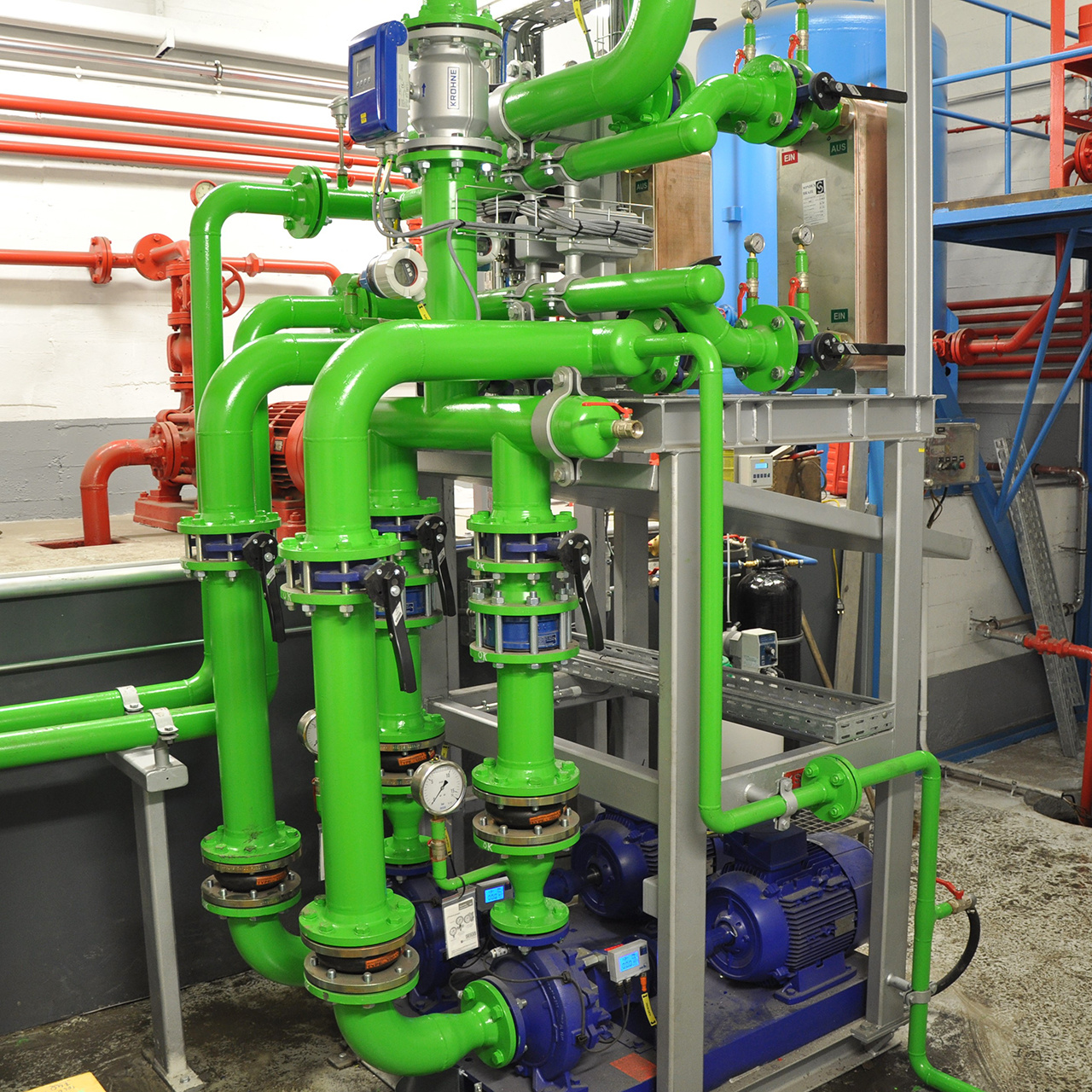
Innovative
The safe cooling of the circulation water heated in the cooling circuit must always be guaranteed. But why not use as much of this waste heat as possible for other purposes? With the innovative solutions for waste heat utilization of our versatile recooling systems, you can easily meet the ever-increasing challenges in energy management. The topic of waste heat utilization is just one of them.
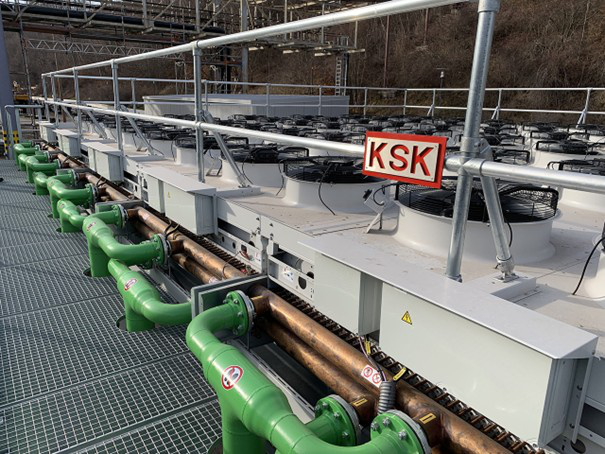
Maintenance-friendly
No long trips to the control room or to the plant to check measured values or to set the cooling circuit to maintenance mode – in a KSK pump station, you will find everything in one place: control cabinets with control panels, pump technology, sensors, water treatment, leakage monitoring and much more. Of course, we ensure that all purchased parts used are absolutely suitable for steelworks. So, after the pump station has been put into operation, you can concentrate fully on the daily madness again. Because unlike suppliers, colleagues and customers, our cooling circuit always does what it is supposed to do, all by itself: cool reliably around the clock.
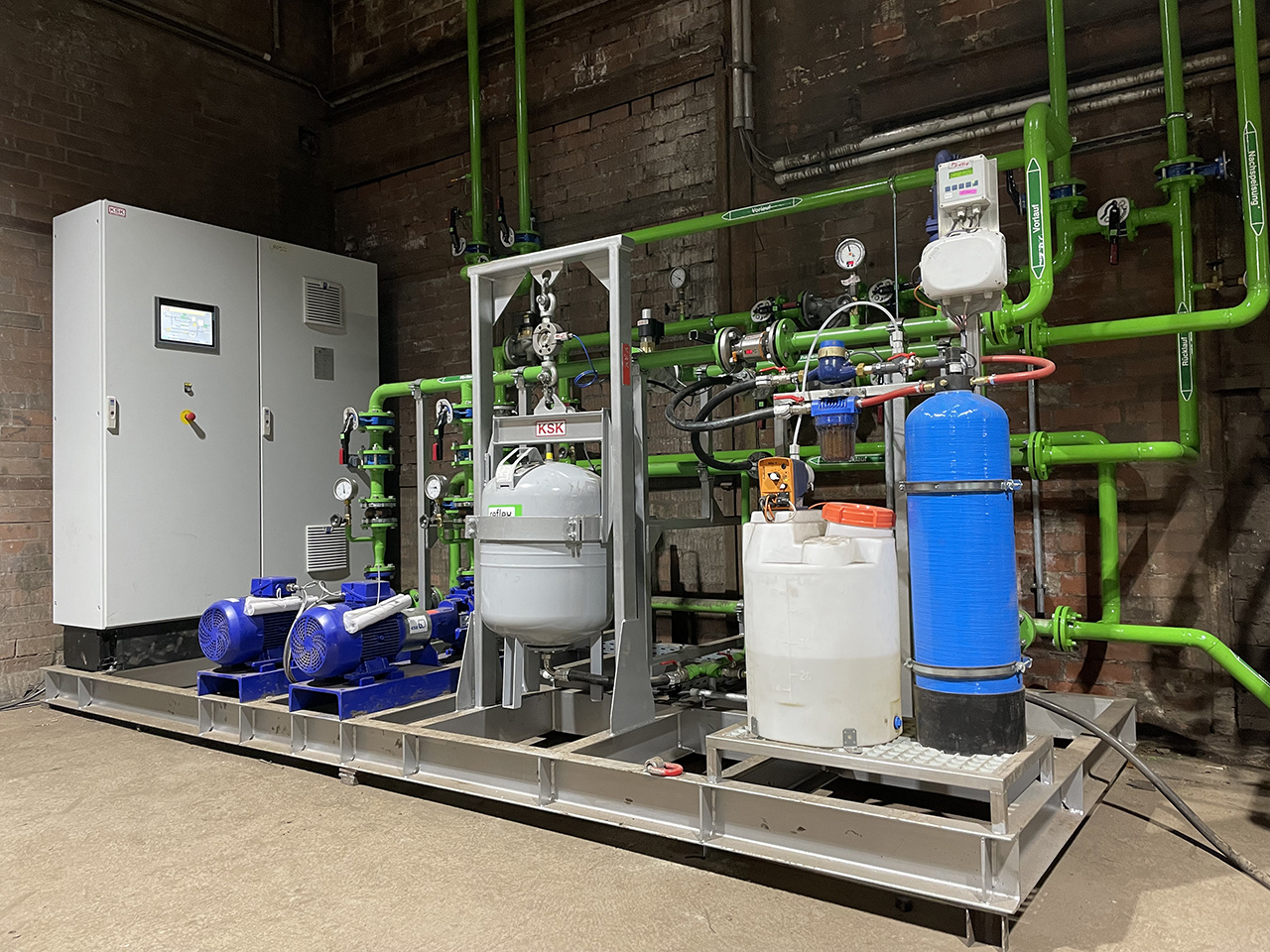
Economical
In terms of process engineering, well-thought-out recooling systems, combined with a thorough understanding of the units to be cooled, ensure that we dimension pumps, recoolers and the like in an economically sensible way. When it comes to combining bought-in components in our recooling circuits, we can also rely on a strong network of partners and suppliers with whom we have been working for years. Not sure which building you should house the new pump station in? Then ask about our KSK plug & play container solution. We install the entire pump technology, control cabinets with control panels and even the heat exchanger in a transportable container, so all you have to do is connect the cables and water pipes on your premises. As a result, you save both investment and operating costs, making the new cooling circuit a complete success for maintenance, operations and purchasing!
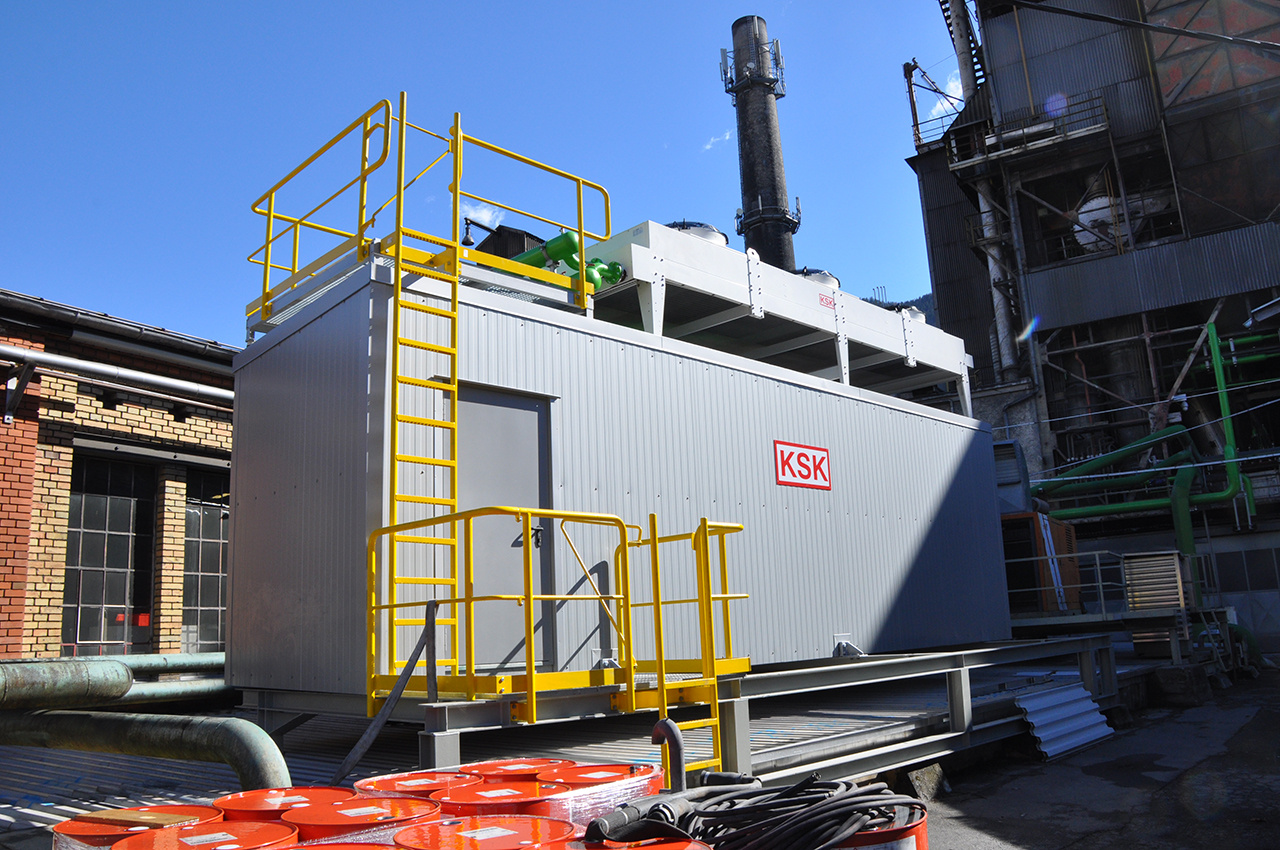
What is industrial cooling and why is it important?
Basics of industrial cooling
Industrial cooling encompasses all measures and technologies used to regulate the temperature in industrial processes. Industrial cooling is needed to ensure the optimal functioning of machines and equipment that depend on a constant and precise temperature. Efficient and reliable industrial cooling can extend the lifespan of machinery and improve product quality in many industries.
The importance of process cooling in industry
Process cooling is an integral part of industrial cooling, as it controls the temperature during production and thus ensures the smooth running of industrial processes. Whether in the food industry, in the storage of sensitive materials or in the manufacture of machine tools – process cooling is crucial for the quality and competitiveness of products. It guarantees that temperature requirements are precisely met.
How industrial cooling optimizes production
Industrial chillers are designed to efficiently dissipate the heat generated during industrial processes. This not only optimizes production, but also increases the operational safety and reliability of the systems. By using industrial machine cooling, manufacturers can shorten production times and increase efficiency. This leads to greater competitiveness in the market.
What types of cooling systems are there in industrial cooling?
Differences between chillers and cooling towers
Chillers and cooling towers are two of the most commonly used systems in industrial cooling. Chillers are particularly efficient because they use refrigerant-cooled fluids to dissipate heat. In contrast, cooling towers use evaporative cooling and are particularly in demand for large industrial applications. Both systems offer customized solutions that are tailored to the specific requirements of industry.
How do water-cooled systems work?
Water-cooled systems use water as a coolant to increase the efficiency of heat removal. These systems are particularly attractive in applications with high cooling requirements, as they provide constant and reliable cooling. Water-cooled cooling systems are able to absorb large amounts of heat and are therefore ideal for use in large industrial processes where precision and reliability are crucial.
What are free coolers and their applications?
Free cooling systems, also known as “free cooling”, use outside air to support cooling without the use of refrigeration units. This technology is particularly energy efficient as it reduces energy consumption and lowers operating costs. Free cooling systems are ideal for applications in cooler climates or during cold seasons, as they provide an environmentally friendly alternative to traditional process cooling.
How do you choose the right cooling system for industrial applications?
Requirements and solutions for individual applications
Selecting the right cooling system depends on the specific requirements of the application. Factors such as the size of the plant, cooling demand, type of process and ambient temperatures play a crucial role. A careful analysis of these requirements makes it possible to develop customized solutions that maximize cooling efficiency and reliability.
What role do chillers play in process cooling?
Chillers are a central component of process cooling, as they precisely regulate the temperature in industrial processes. They ensure that the required temperatures are constantly maintained to ensure the quality and reliability of production. Modern chillers are equipped with advanced technology that guarantees high energy efficiency and low operating costs.
How can the reliability of cooling systems be ensured?
The reliability of cooling systems can be ensured through regular maintenance and the use of smart technologies. Remote monitoring and automated control systems make it possible to detect potential problems early on and rectify them before they lead to a failure. Well-planned maintenance helps to extend the lifespan of the equipment and keep operational reliability at a high level.
Which technologies increase the efficiency of cooling systems?
Smart technologies in industrial cooling
Smart technologies are revolutionizing industrial cooling by enabling precise control and monitoring of cooling systems. These technologies use sensors and algorithms to optimize operations and maximize energy efficiency. By using smart technologies, companies can reduce energy consumption and significantly reduce operating costs.
How chillers contribute to energy efficiency
Chillers are known for their high energy efficiency because they are able to dissipate large amounts of heat with minimal energy input. By using energy-efficient components and technologies, chillers help to reduce the total cost of cooling. They provide a reliable and cost-effective solution for many industrial applications.
Innovations in cooling technology
Cooling technology is constantly evolving to meet the increasing demands of industry. New innovations such as high-efficiency heat exchangers, advanced control systems and environmentally friendly refrigerants are helping to improve the efficiency and sustainability of cooling systems. These innovations enable companies to optimize their cooling processes and increase their competitiveness.
How can you reduce the operating costs of cooling systems?
Optimizing the energy efficiency of refrigeration systems
Optimizing energy efficiency is key to reducing the operating costs of refrigeration systems. By implementing energy-efficient technologies and regularly maintaining systems, companies can significantly reduce their energy consumption. Careful planning and optimization of cooling processes helps to reduce costs in the long term.
How do refrigerants affect operating costs?
Choosing the right refrigerant can have a significant impact on operating costs. Environmentally friendly and energy-efficient refrigerants help to reduce energy costs and environmental impact. By using modern refrigerants, companies can increase the efficiency of their cooling systems while minimizing operating costs.
Customized solutions to reduce costs
Customized solutions are crucial to reducing the operating costs of refrigeration systems. By adapting cooling systems to the specific requirements of the applications, companies can maximize efficiency and cost-effectiveness. Working closely with experienced manufacturers and suppliers makes it possible to develop individual solutions that meet the highest standards of energy efficiency.
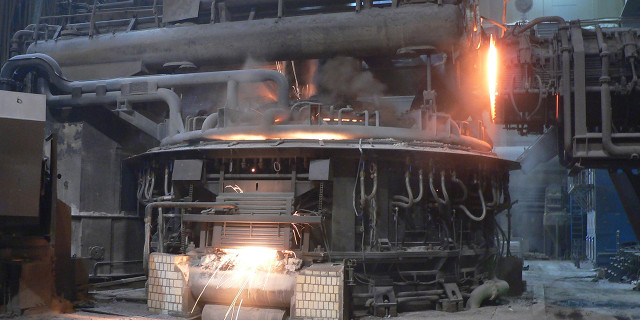
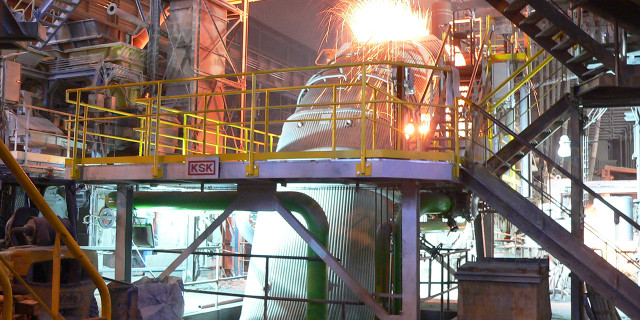
Exhaust gas cooling
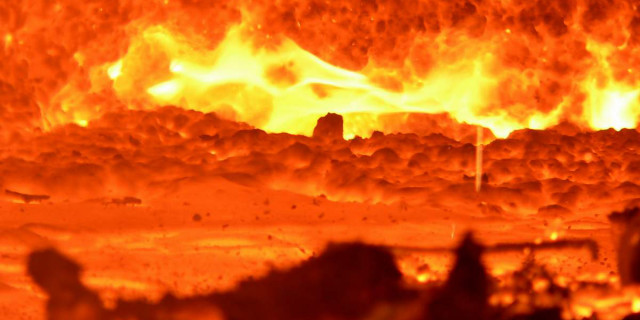
Waste heat recovery
FAQs on Industrial cooling
Table of contents
- Q: What is industrial cooling?
- Q: How does a chiller work in industrial cooling?
- Q: What role does stability play in industrial cooling?
- Q: What is a cooling tower and how is it used in industrial cooling?
- Q: What are the benefits of using smart cooling systems in industry?
- Q: Why is machine cooling important in industry?
- Q: What are the challenges in the design of industrial cooling systems?
- Q: How is cold storage implemented in the pharmaceutical industry?
- Q: What is the role of oil cooling in industrial processes?
Q: What is industrial cooling?
A: Industrial cooling refers to the processes and systems designed to efficiently cool machinery, production equipment and other industrial applications. This may include chillers, cooling towers and specialized air conditioning systems. Industrial cooling plays a crucial role in many industries, including food and beverage, chemical production, metal processing and pharmaceuticals. The main objectives of industrial cooling are to maintain optimal temperatures for machinery and processes, to prevent overheating, and to ensure high energy efficiency.
Chillers are central components of many cooling systems, as they generate and distribute cool water that is used to regulate the temperature in various processes. Cooling towers, on the other hand, use evaporation to remove heat and bring the cooling water back to a usable temperature. Specialized air conditioning systems are often used in areas where precise temperature and humidity control is required, such as clean rooms or the storage of temperature-sensitive products.
Selecting the appropriate cooling system depends on various factors, including the specific requirements of industrial processes, ambient temperatures and the company's energy efficiency goals. Modern systems often integrate advanced technologies such as IoT sensors and automation to optimize operations and minimize energy consumption. In addition, sustainable cooling methods that are based on renewable energy or use natural coolants are becoming increasingly important to reduce the environmental footprint of industrial cooling.
Q: How does a chiller work in industrial cooling?
A chiller is a system that cools water for use in a circuit to cool machinery, production equipment or buildings. It is often used in process cooling to ensure stability and efficiency in industrial applications. A chiller typically consists of several main components, including a compressor, an evaporator, a condenser and an expansion valve. The compressor draws and compresses the refrigerant, causing it to heat up. The refrigerant is then cooled and liquefied in the condenser before passing through the expansion valve, where the pressure drops and the refrigerant cools. In the evaporator, the cold refrigerant draws heat from the water, cooling the water. This cooled water is then pumped through a system of pipes to the machines or buildings that need cooling.
Chillers are available in a range of sizes and designs, and can be used for both small applications, such as office buildings, and large industrial applications. They are an energy-efficient solution because they are able to remove large amounts of heat with relatively little energy input. Modern chillers are also equipped with advanced control systems that allow precise control of temperature and energy consumption.
Selecting the right chiller depends on various factors, including the specific cooling requirements, the size of the area to be cooled and the ambient conditions. Efficiency, reliability and environmental compatibility are also important criteria when making the selection. In times of rising energy costs and growing environmental awareness, the integration of sustainable technologies, such as the use of environmentally friendly refrigerants, is also becoming increasingly important.
In summary, the use of chillers offers an effective way to optimize temperature control in various industrial and commercial applications, resulting in increased productivity and a longer service life for equipment.
Q: What role does stability play in industrial cooling?
A: Stability is crucial in industrial cooling, as it ensures that cooling processes run reliably and smoothly. This is especially important in the food and pharmaceutical industries, where constant temperatures are crucial for the quality and safety of the products. To ensure stability in industrial cooling, a range of technologies and strategies are used. First, precise control systems play a central role. These systems continuously monitor temperature and automatically adjust cooling capacity to minimize fluctuations. Modern sensors and control units are crucial to ensure a high level of accuracy and responsiveness.
In addition, the maintenance of cooling systems is of great importance. Regular inspections and maintenance help to identify potential problems early on and to fix them before they can lead to major disruptions. This includes checking the refrigerant level, seals, valves and other critical components.
Another important aspect is the energy efficiency of the cooling systems. By using energy-efficient technologies and optimizing operations, companies can not only save costs but also reduce their environmental impact. The use of environmentally friendly refrigerants and the implementation of heat recovery systems also contribute to sustainability.
Finally, staff training plays a crucial role. Well-trained employees are able to operate the systems optimally and respond to faults quickly and effectively. They can also support the implementation and optimization of new technologies.
Overall, the combination of modern technology, regular maintenance, energy efficiency and qualified personnel is crucial to ensure stability in industrial cooling and to meet the high requirements of the food and pharmaceutical industries.
Q: What is a cooling tower and how is it used in industrial cooling?
A: A cooling tower is a device that dissipates heat from a cooling water circuit to the surrounding air. It is often used in large production plants to remove excess heat from machines and processes such as welding machines and presses. A cooling tower is a device that dissipates heat from a cooling water circuit to the surrounding air. It is often used in large production plants to dissipate excess heat from machines and processes such as welding machines and presses. Cooling towers are also crucial in power plants, refineries and other industrial facilities to maximize the efficiency of processes and ensure operational reliability.
There are several types of cooling towers, including wet cooling towers, dry cooling towers, and hybrid cooling towers. Wet cooling towers use the evaporation of water to remove heat, while dry cooling towers rely on airflow to lower temperature. Hybrid cooling towers combine both methods to take advantage of both systems.
A key aspect of operating a cooling tower is water treatment, as the evaporation of water can cause a concentration of minerals and other impurities. Insufficient water treatment can lead to scaling, corrosion and biological growth, which reduces the efficiency of the cooling tower and increases maintenance costs.
In addition, cooling towers play an important role in environmental management by helping to reduce water consumption and minimize environmental impact. Modern cooling tower designs focus on maximizing energy efficiency and reducing emissions to reduce the environmental footprint of industrial facilities.
Q: What are the benefits of using smart cooling systems in industry?
A: Smart cooling systems offer numerous advantages, including improved energy efficiency, more precise control of temperatures, and the ability to detect potential malfunctions early on. This results in cost savings and increased reliability of cooling processes. In addition, smart cooling systems enable seamless integration with existing building automation systems, facilitating centralized control and monitoring. By utilizing advanced sensors and IoT technologies, users can access real-time key performance data and make informed decisions to further optimize operations.
Another advantage is the possibility of predictive maintenance. By continuously monitoring system parameters, anomalies can be detected early and resolved before failure occurs. This not only minimizes downtime but also extends the service life of the equipment.
Finally, smart cooling systems contribute to sustainability by reducing energy consumption and reducing companies' carbon footprint. The implementation of such technologies is an important step towards greener and more efficient industrial processes.
Q: Why is machine cooling important in industry?
A: Machine cooling is crucial to ensure the lifespan and performance of industrial machines such as lasers and presses. Efficient cooling prevents overheating and breakdowns that can lead to lost production and increased maintenance costs. In addition, well-designed cooling helps improve the energy efficiency of the machines by minimizing the energy consumption required to maintain optimal operating temperatures. Various cooling methods, such as air or liquid cooling, can be used depending on the specific needs of the application.
Liquid cooling systems are often more effective at removing heat and are particularly suitable for high-performance machines that generate large amounts of heat. These systems use coolants that circulate through heat exchangers to remove heat from critical components.
Regular maintenance and monitoring of cooling systems is also important to ensure that they are operating efficiently and that there are no leaks or other issues that could affect cooling performance. Modern cooling systems are often equipped with sensors and monitoring technology that can provide real-time data and provide early warning of potential problems.
In summary, effective machine cooling not only extends the service life of the machines, but also optimizes their performance and reduces operating costs. Companies that invest in high-quality cooling systems and prioritize their maintenance can benefit from higher productivity and reduced downtime in the long term.
Q: What are the challenges in the design of industrial cooling systems?
A: The challenges in designing industrial cooling systems include adapting to specific production process requirements, integrating smart technologies to improve efficiency, and ensuring reliability under various operating conditions. Another important aspect is taking into account environmental and sustainability standards. Industrial cooling systems must be designed to minimize energy consumption while maximizing cooling capacity to reduce the environmental footprint. The choice of the right refrigerants plays a crucial role here, as more environmentally friendly alternatives to traditional refrigerants are increasingly in demand to meet legal requirements and minimize the impact on the environment.
Furthermore, ease of maintenance is an important factor in the design process. Systems should be designed to be easily accessible and simple to maintain in order to reduce downtime and lower operating costs. This often requires the implementation of modular components that can be quickly replaced when needed.
The increasing digitalization in industry also brings with it the opportunity to implement better monitoring and control of cooling systems through the use of IoT (Internet of Things) technologies. By using sensors and real-time data analysis, potential problems can be detected early and resolved before they cause serious disruptions.
In summary, the design of industrial cooling systems requires a careful balance between efficiency, environmental sustainability, reliability and ease of maintenance. Only by considering all these factors can a cooling system be developed that meets the complex requirements of modern industrial processes while also being sustainable and cost-effective.
Q: How is cold storage implemented in the pharmaceutical industry?
A: In the pharmaceutical industry, storage cooling is implemented by specialized refrigeration systems that enable constant and precise temperature control. This is crucial to ensure the quality and efficacy of pharmaceutical products. In the pharmaceutical industry, cold storage is implemented through specialized refrigeration systems that provide constant and precise temperature control. This is crucial to ensure the quality and efficacy of pharmaceutical products. Effective cooling prevents the degradation of active ingredients and protects sensitive formulations from temperature fluctuations that could compromise their stability.
Modern cooling systems utilize advanced technologies such as sensors and automated control systems to monitor and adjust temperature in real time. These systems can be programmed to sound an alarm when the temperature is outside a predetermined range, enabling quick corrective action.
In addition, compliance with international guidelines and standards, such as the Good Distribution Practice (GDP) guidelines, ensures that the cold chain is not interrupted during transportation and storage. This is especially important for vaccines, biologics, and other temperature-sensitive products that must be stored at specific temperatures to retain full potency.
Regular maintenance and calibration of cooling systems are also crucial to ensure their reliability. Companies are increasingly investing in environmentally friendly cooling solutions that reduce energy consumption and minimize environmental impact without compromising cooling quality.
In summary, precise temperature control in the pharmaceutical industry is a critical factor that not only ensures product quality but also ensures regulatory compliance and strengthens consumer confidence in pharmaceutical products.
Q: What is the role of oil cooling in industrial processes?
A: Oil cooling plays an important role in industrial processes by regulating the temperature of oils used in machines. This prevents overheating and ensures that machines function smoothly, increasing their lifespan and efficiency. In addition, oil cooling helps to reduce wear on machine parts by ensuring the thermal stability of the oil. Maintaining a constant and optimal operating temperature of the oil is crucial to maintaining its viscosity, which in turn improves its lubricating properties. This is especially important in high-performance machines where precise movements and high speeds are required.
In practice, oil cooling is often achieved by using heat exchangers that transfer excess heat to the surrounding environment or to a cooling system. Some systems also use fans or liquid cooling to lower the temperature of the oil. The choice of appropriate cooling method depends on various factors, including the type of machine, operating conditions and the specific requirements of the process.
Modern oil cooling systems are often equipped with sensors and control technologies that enable continuous monitoring and adjustment of the cooling performance. This not only ensures efficient operation but also contributes to energy savings by optimally controlling the cooling process.
Furthermore, advanced oil cooling solutions can be integrated with condition monitoring systems that monitor the condition of the oil and the machine in real time. This way, potential problems can be detected early and addressed before they lead to major breakdowns.
Overall, oil cooling is an essential component of modern industrial applications, which not only helps to extend the service life of machines, but also offers significant economic advantages by reducing downtime and maintenance costs.