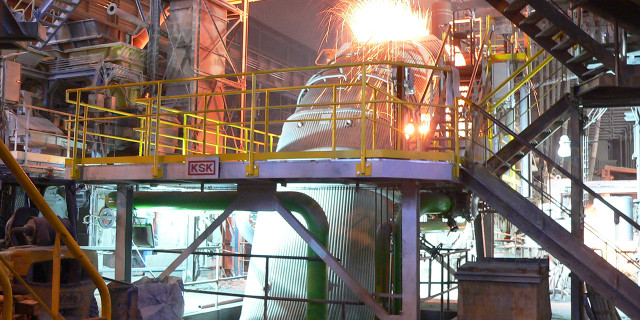
Table of contents
-
KSK electric arc furnace.
- Electric arc furnace: efficient steel production in the electric arc furnace
- Convincing plant technology.
- Intelligent designs.
KSK electric arc furnace.
It all began for KSK in the 1980s with the electric arc furnace. We replaced the original fireproof brickwork of the lid and upper vessels of the electric arc furnace with our water-cooled tube constructions. And even today, much of our work revolves around the electric arc furnace, because the electric arc furnace is more in demand than ever in times of green steel production as an electric steel process.
Electric arc furnace: efficient steel production in the electric arc furnace
The electric arc furnace has established itself as one of the most advanced technologies in steel production by providing an efficient alternative to the traditional blast furnace process. This method of steel production uses electrical energy to achieve the high temperatures required for melting metals. The use of this technology not only makes steel production more cost-efficient, but also more environmentally friendly, as it facilitates the recycling of steel scrap.
Convincing plant technology.
The key to economically successful operation lies in the plant technology used. This is where it is decided how long the repair shift for your electric arc furnace will last. And when the next repair shift will be, because, for example, the weld seam at the reversing hood of the third lid panel was not welded with a root, contrary to the drawing. Wouldn't it be nice to know that competent fitters and welders in two small workshops in the middle of Germany would also take care of the root layers in your cover panel?
Intelligent designs.
Or that our dedicated team of engineers designs your electric arc furnace upper vessel in such a way that wall panels can be easily replaced with a few simple steps and an overhead crane? Of course, our engineers also develop excellent technical solutions for shaft furnaces, rotary kilns, ladle furnaces, bath melting furnaces, pilot furnaces and other melting and recycling units, always in accordance with the six KSK quality criteria.
The six KSK quality criteria in the melting and recycling processes.
Clear layout
To make sure you don't lose sight of the big picture, even in critical situations, and always know which damper to use to shut off which cooled area, we always design all melting units to be as clear and as simple as possible. Even if it's just a routine check: everything is much more relaxed when the hose routing is as clear as it is in this electric arc furnace.
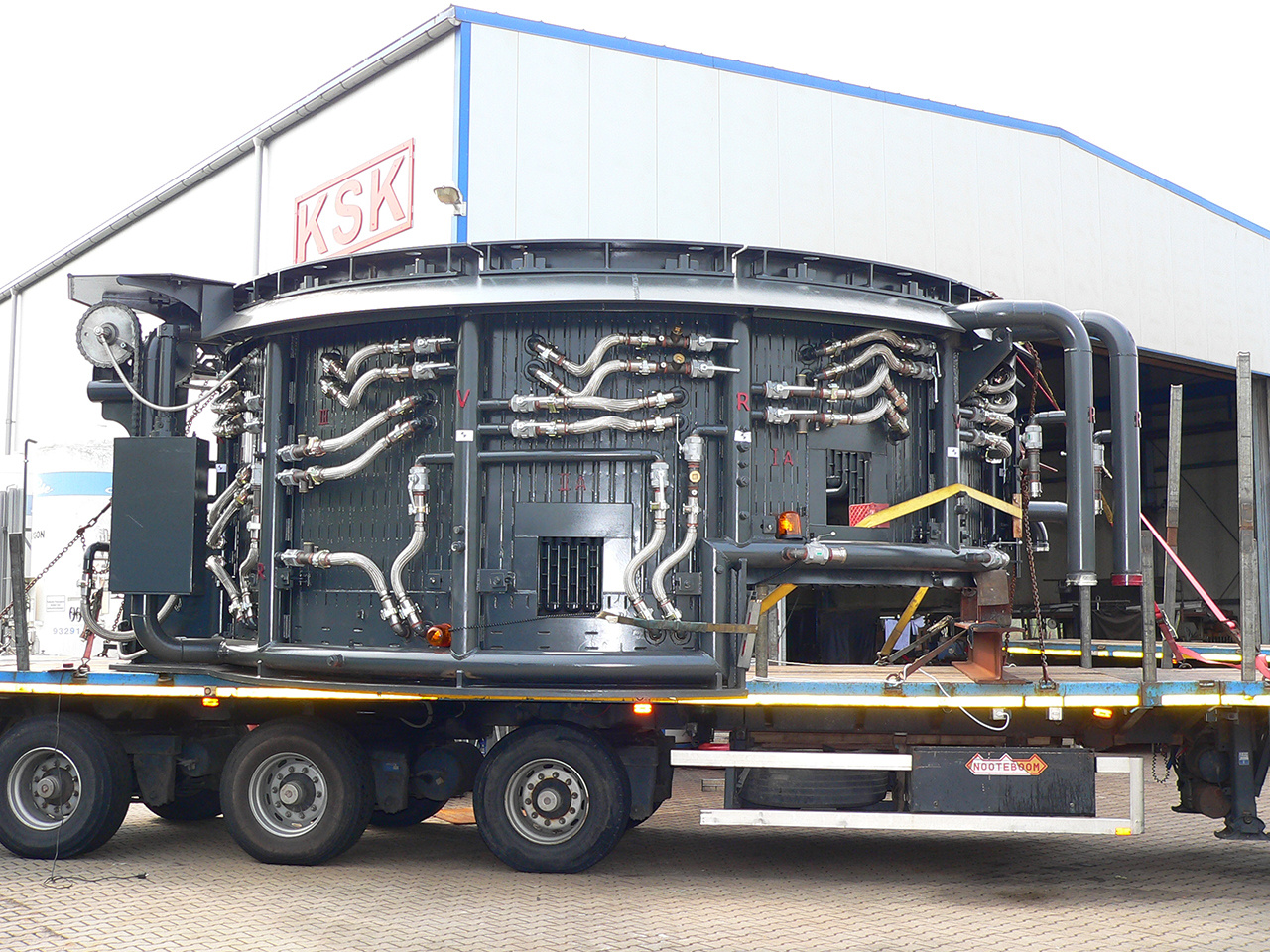
Functional
The slide gate of your ladle furnace is always stuck in the guide, the hinged door on the ladle furnace of the neighboring stand is jammed and can no longer be opened? Of course, this can also happen with our water-cooled hinged slide gates (with hinged and sliding function) – but it is highly unlikely to happen as often. The functionalities of our designs are based on 40 years of experience with the electric steel process and a love of detail – and not just on the ladle furnace cover.
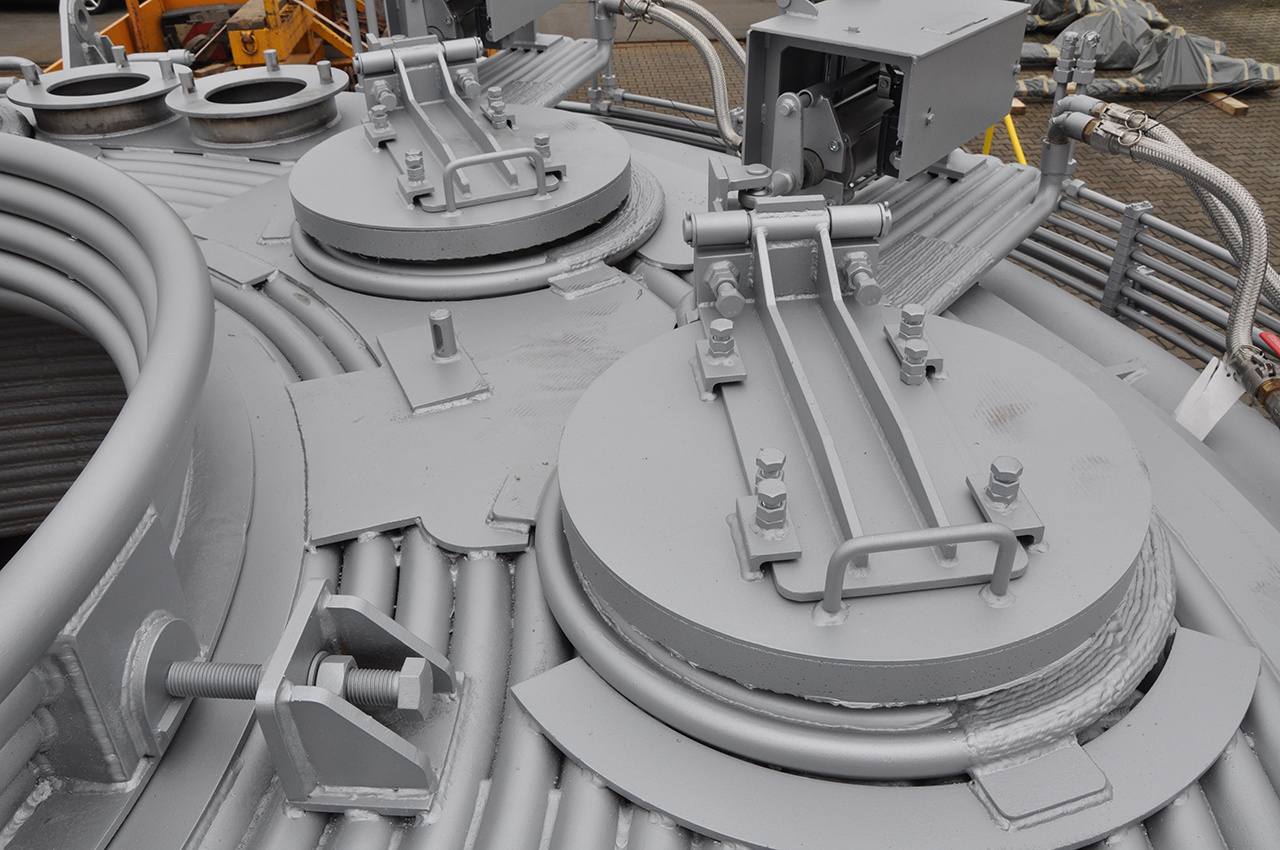
Innovative
You want to know what that is? No, not the immersion sleeves for the temperature sensors. The funny nozzles with screw caps underneath. Exactly! No idea what they are for? Please call us, we will be happy to tell you. Even though electric arc furnaces and ladle furnace covers are not new, we regularly develop innovative solutions in the field of electric steel processes that improve your aggregates and make your everyday life easier.
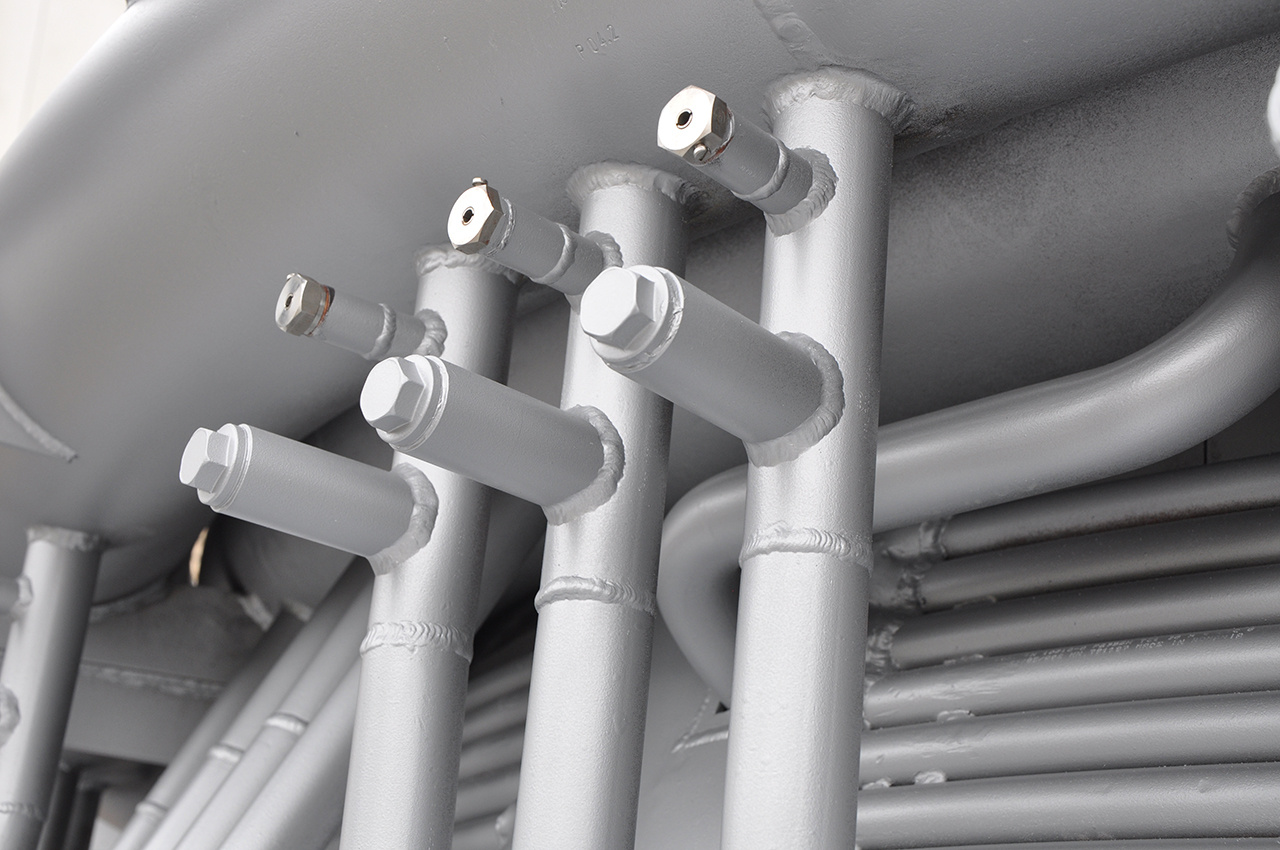
Perfect fit
Nothing we make is off the rack. We assign an order number to every ladle furnace cover, not a type designation. We never develop our customized solutions alone, but always as a team – together with you. And if necessary, we also take the time to go the extra mile in our coordination. What counts in the end is that you don't have to bend to our technical solution, but that our bent tubes can offer you and your electric steel process new technical possibilities. And even if it's just the color concept: We are happy to design according to your wishes!
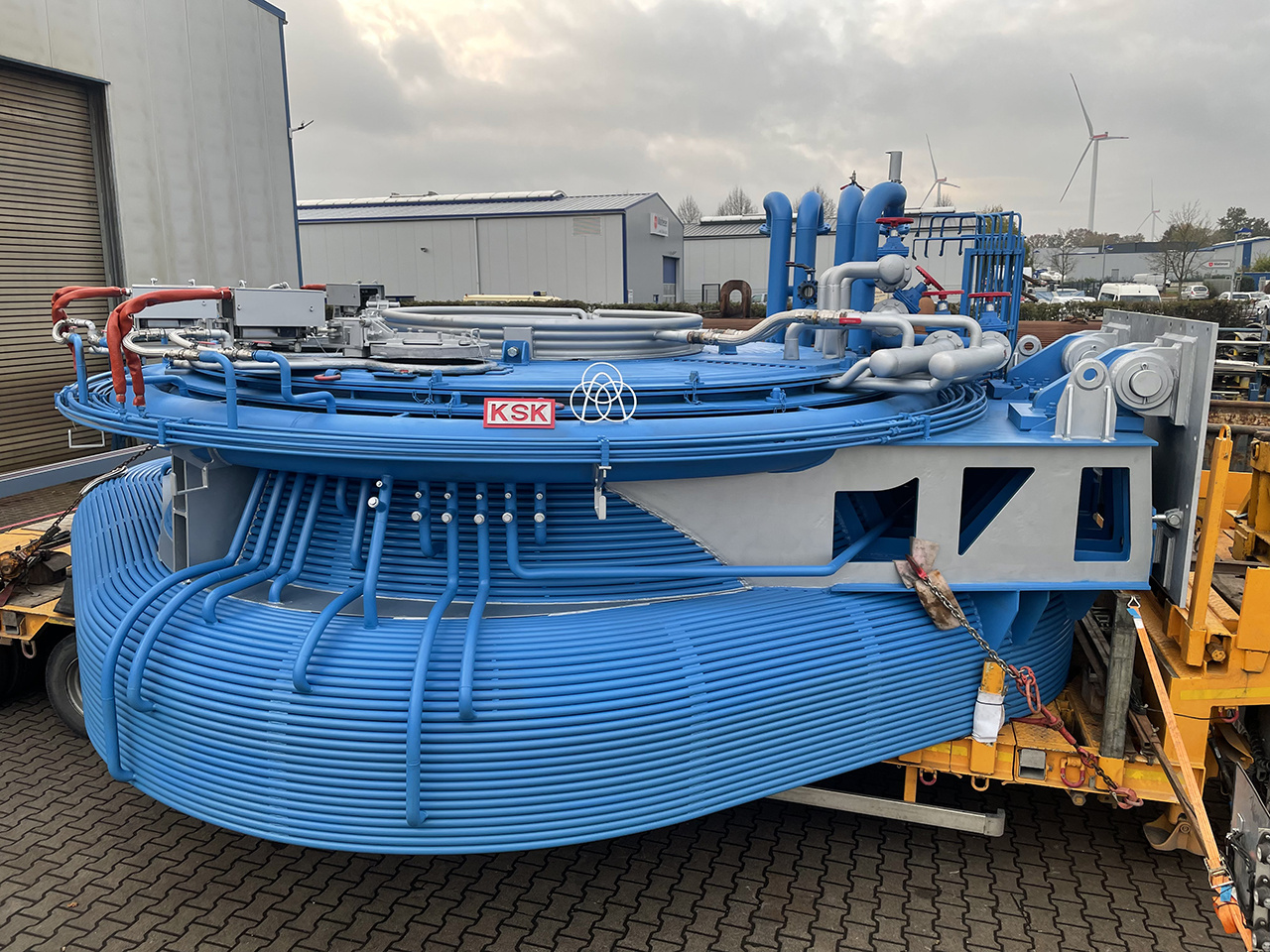
Maintenance-friendly
Do you work in maintenance? Then you've come to the right place! You are the driving force behind our work. And at the same time, our greatest support. We develop solutions for and with maintenance, and have been doing so for almost 40 years. Only by being close to the everyday challenges of working with a ladle furnace cover or other melting units in the electric steel process can we find solutions to make precisely this work easier. Otherwise, we would never have come up with the idea of developing a self-cleaning system for ladle furnace covers.
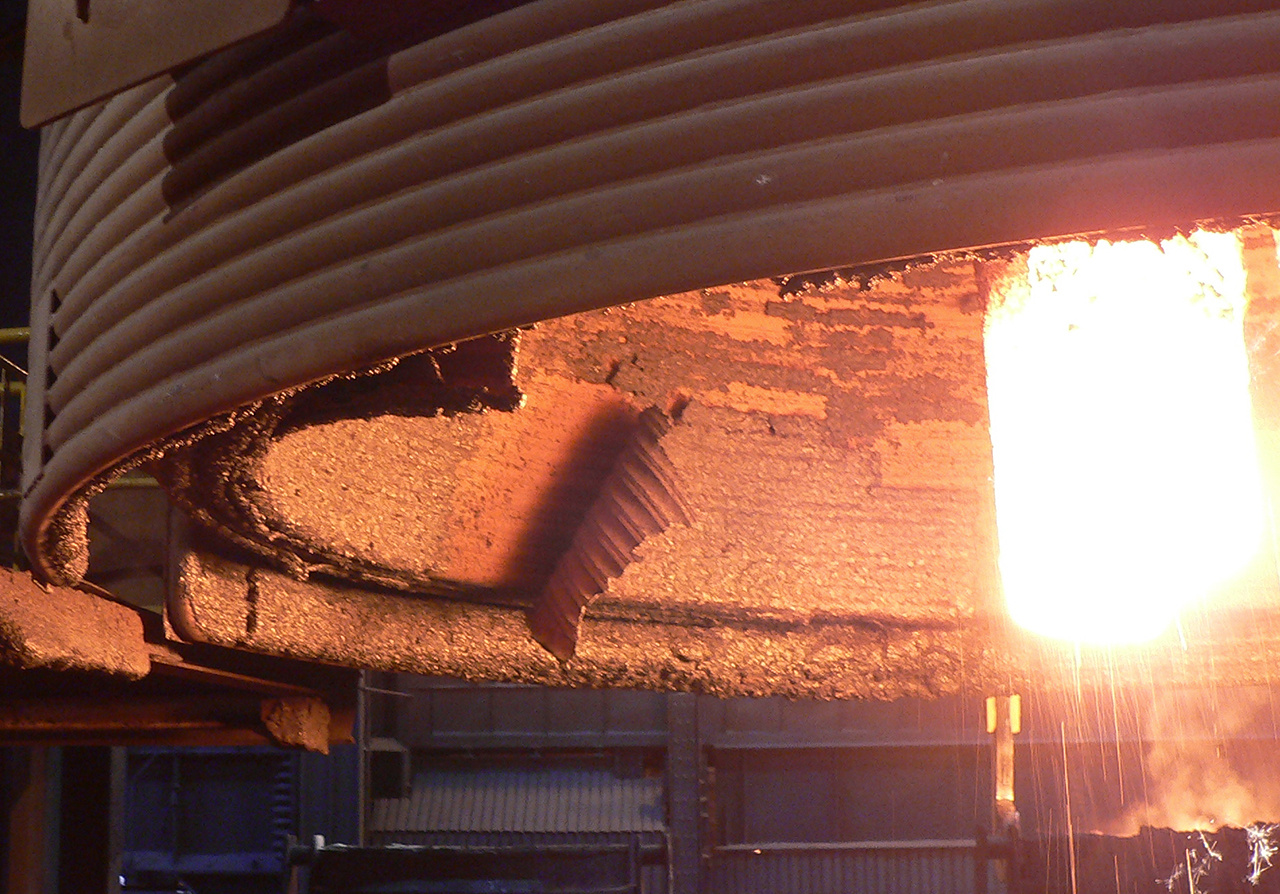
Economical
At the end of the day, every investment should pay off. Of course! When planning our systems, we always have productivity, energy efficiency, service life, material costs, availability and costs of spare parts and many other aspects related to electric arc furnaces, ladle furnace covers and the like in mind and weigh them against each other. After all, we want to work with you in the long term!
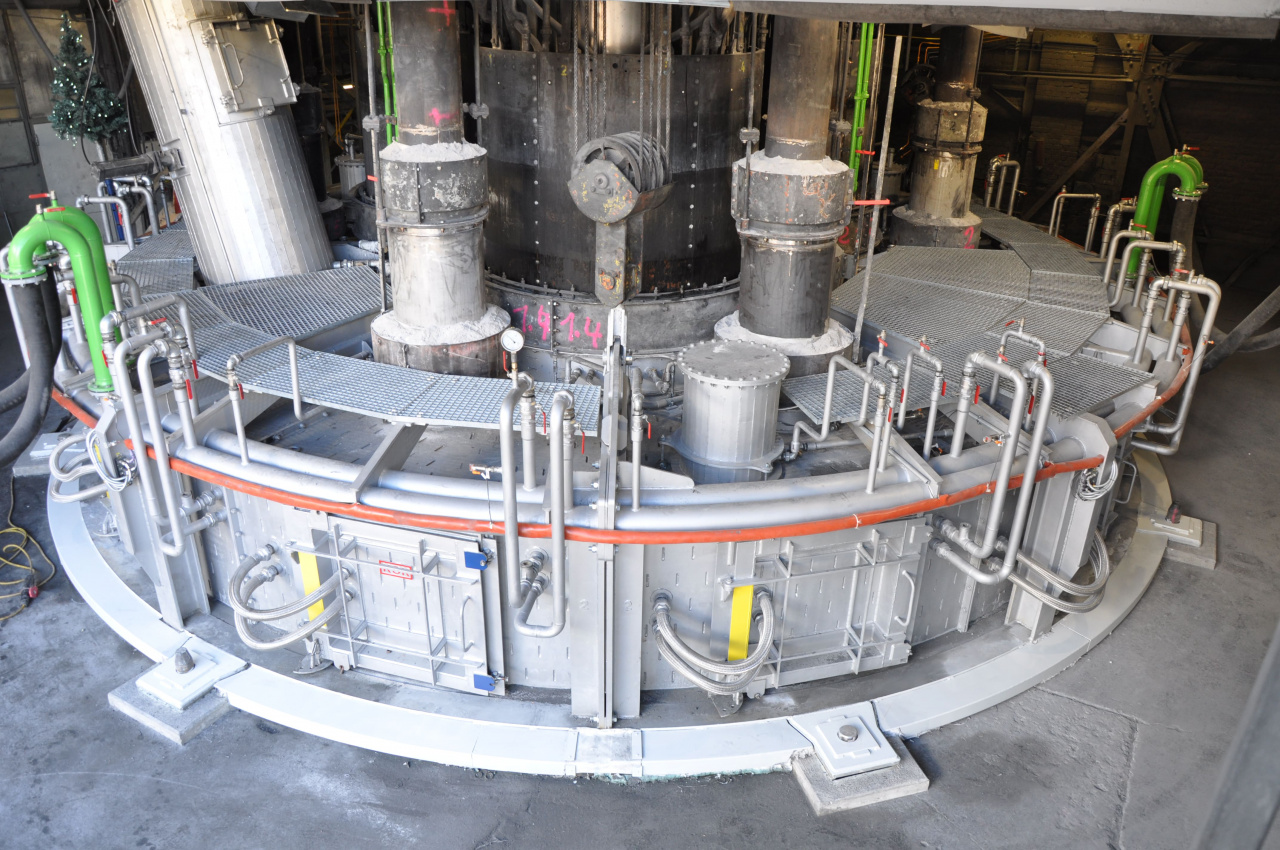
What is an electric arc furnace and how does it work?
How is the arc generated in the furnace?
The arc in the electric arc furnace is generated by the use of three (AC) or one (DC) graphite electrodes that conduct the electric current. These electrodes are lowered into the furnace and a short circuit between the electrodes and the scrap or the charge takes place. As soon as the electric current flows through the electrodes, an arc is created that can reach temperatures of up to 3,500 °C. This extreme heat is necessary to melt the metal and start the steelmaking process.
What role do graphite electrodes play in the electric arc furnace?
Graphite electrodes are crucial to the functionality of the electric arc furnace. They serve as conductors for the electric current and are able to generate the extreme heat necessary to melt the metal. The electrodes are continuously worn down and must be replaced regularly to ensure consistent performance. Their high conductivity and resistance to high temperatures make them an indispensable component of modern steel production.
How does the electric arc furnace affect the steel production process?
The electric arc furnace significantly impacts the steel production process through its ability to melt metals quickly and efficiently. Unlike the blast furnace process, which requires large quantities of coal and iron ore, the electric arc furnace can also use recycled scrap, resulting in a reduction in raw material costs. In addition, the furnace allows for more precise control of chemical composition, enabling the production of high-quality steel grades.
Why is the electric arc furnace important for modern steel production?
What advantages does the electric arc furnace offer over the blast furnace?
The electric arc furnace offers several advantages over the traditional blast furnace. One of the biggest advantages is the ability to efficiently use recycled steel scrap, which reduces both costs and environmental impact. In addition, the electric arc furnace requires less space and can be ramped up faster, resulting in increased production flexibility. The ability to control the temperature accurately also improves the quality of the steel produced.
How does the electric arc furnace contribute to efficiency in steel production?
The efficiency of the electric arc furnace in steel production is primarily reflected in the reduction of energy consumption and production costs. By using electrical energy instead of fossil fuels, energy consumption can be reduced. The flexibility to quickly turn the furnace on and off allows companies to respond quickly to market demands, which optimizes production planning and reduces inventory costs.
What are the environmental impacts of using electric arc furnaces?
The environmental impacts of using electric arc furnaces are significantly lower than those of traditional methods. The ability to use recycled scrap in large quantities reduces dependence on natural raw materials such as iron ore. In addition, the lower consumption of fossil fuels results in reduced CO2 emissions, which significantly reduces the environmental impact of steel production.
How is recycled scrap used in the electric arc furnace?
Why is recycling steel scrap in the electric arc furnace crucial?
Recycling steel scrap in the electric arc furnace is crucial to the sustainability of steel production. Scrap provides a cost-effective and environmentally friendly alternative to traditional raw materials. Reusing scrap reduces the need for new iron ore and coal, which lowers both the cost and environmental impact of steel production.
How is recycled scrap processed in the electric arc furnace?
The recycled scrap is processed in the electric arc furnace by loading it into the furnace and then melting it using the generated electric arc. During the melting process, oxygen is added to remove impurities and control the chemical composition of the steel. This method makes it possible to produce a wide range of steel grades that are tailored to the specific requirements of industry.
What role does scrap play in the production of liquid steel?
Scrap plays a central role in the production of liquid steel in the electric arc furnace. By melting scrap, liquid steel can be produced, which is then processed into various products. The use of scrap not only enables cost-efficient production, but also helps to reduce emissions and promote a circular economy.
Which companies rely on electric arc furnaces and why?
How does KSK GmbH work with electric arc furnaces?
KSK GmbH is one of the leading companies to rely on electric arc furnaces to optimize its steel production. By implementing this technology, KSK GmbH has been able to reduce its production costs while minimizing its environmental impact. The flexibility and efficiency of the electric arc furnace enable KSK GmbH to respond quickly to changing market demands and to offer high-quality steel at competitive prices.
Which other companies rely on this technology?
In addition to KSK GmbH, there are numerous other companies worldwide that take advantage of electric arc furnace technology. These companies have recognized that the use of electric arc furnaces not only offers economic advantages, but also contributes to the sustainability of the steel industry. Many of these companies have adapted their production processes to maximize the use of recycled scrap and improve the efficiency of their steel production.
What economic benefits do electric arc furnaces offer companies?
Electric arc furnaces offer companies significant economic benefits, including reduced raw material and energy costs. Since these furnaces run primarily on electricity, companies can benefit from lower energy costs, especially in regions with favorable electricity prices. The ability to respond quickly to market changes enables companies to flexibly adjust their production plans and thus reduce inventory costs. In addition, the ability to use recycled scrap opens up new revenue streams and helps to increase profits.
How does temperature affect steel production in the electric arc furnace?
What temperatures are reached in the electric arc furnace?
Extremely high temperatures are reached in the electric arc furnace, which can reach up to 3,500°C. These high temperatures are crucial for efficiently melting the metal and removing impurities. The ability to generate such temperatures allows the EAF to melt a wide range of metals and produce various types of steel.
How does temperature affect the melting of the metal?
The temperature in the EAF plays a crucial role in melting the metal. Higher temperatures accelerate the melting process and improve the efficiency of steel production. By precisely controlling the temperature, impurities can be efficiently removed and the chemical composition of the steel can be precisely adjusted. This results in higher quality of the produced steel and enables the production of specialty steels that meet specific requirements.
Why is temperature control crucial for the quality of the produced steel?
Temperature control in the electric arc furnace is crucial for the quality of the steel produced, as it influences the chemical composition and physical properties of the steel. Precise temperature control makes it possible to minimize impurities and achieve the desired properties of the steel. This is particularly important for the production of high-quality steel used in demanding applications where material properties are crucial.
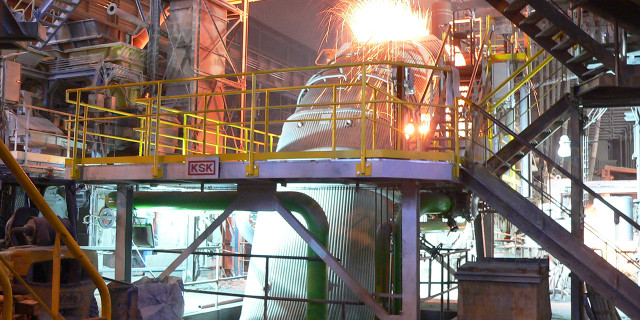
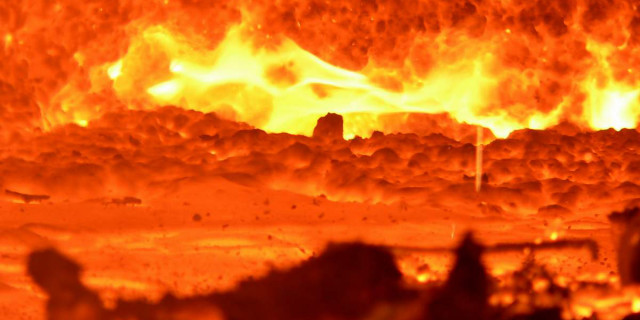
Waste heat recovery
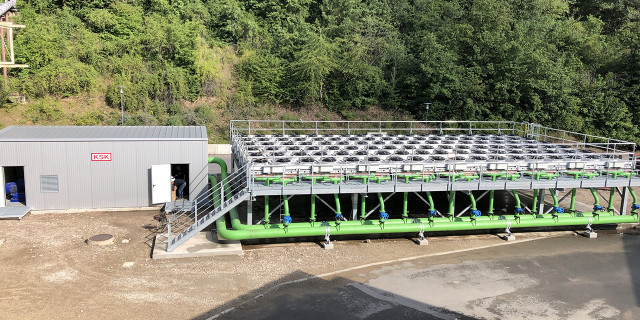
Industrial cooling
Exciting and interesting facts about the electric arc furnace
Table of contents
- What characterizes the electric arc furnace?
- How does the electric arc furnace contribute to the EU climate targets?
- What types of steel are produced in the electric arc furnace?
- How much electricity does an electric arc furnace need?
- What happens in the electric arc furnace?
- What is the advantage of the electric steel process?
- What happens in a steel mill?
What characterizes the electric arc furnace?
Although we see ourselves as an apparatus and plant engineering company, our 40 years of experience in the electric steel process has also given us a fundamental knowledge of the process technology and metallurgy of the electric arc furnace. We would be happy to discuss further questions with you that go beyond water cooling or put you in touch with a good partner from our network who, like us, is an expert in a particular technology.
The electric arc furnace itself is a unit for melting steel scrap of various qualities. Steel can be produced from iron ore via the blast furnace and converter route. However, it makes more sense in terms of energy to melt it from steel scrap in an electric arc furnace using the electric steel process. After the electric arc furnace, the liquid steel can be further processed in secondary metallurgy in a ladle furnace, for example, to refine its metallurgy.
Incidentally, induction is also an electric steel process in which we are at home. In this electric steel process, however, our expertise is clearly limited to off-gas cooling. The situation is similar for other electric steel processes, such as the bath melting furnace. We remain true to our motto “We do what we can and can what we do”, largely staying out of the metallurgy of this electric steel process and concentrating on the apparatus engineering, or in this case on furnace construction.
How does the electric arc furnace contribute to the EU climate targets?
The electric arc furnace is an important tool in the steel industry. It is a specialized furnace used to melt scrap and produce steel products. With energy efficiency and the ability to produce clean and highly efficient steel products, the electric arc furnace makes a significant contribution to meeting EU climate targets.
A key element in the fight against climate change is the reduction of greenhouse gas emissions. The electric arc furnace is an important tool for achieving this goal. It enables the production of steel with minimal energy consumption, which significantly reduces greenhouse gas emissions. In addition, higher quality steel products can be produced, meaning that less energy is needed to produce them, which in turn leads to a further reduction in greenhouse gas emissions.
Another advantage of the electric arc furnace is that it offers a cleaner and more efficient method of producing steel. It uses a combination of electricity and gas to heat scrap, which in principle reduces the use of fossil fuels. This reduces emissions of pollutants and other harmful substances, which also contributes to reduced greenhouse gas emissions. The electric arc furnace is an important tool for sustainable energy supply. It uses electricity, ideally from renewable sources such as wind or solar energy, and thus enables the steel industry to produce and use steel cleanly and efficiently. This is an important contribution to a sustainable energy supply and at the same time helps to reduce greenhouse gas emissions.
The electric arc furnace is a powerful tool to help the steel industry meet EU climate targets. Thanks to its energy efficiency and ability to produce clean and highly efficient steel products, the electric arc furnace makes a significant contribution to reducing greenhouse gas emissions and ensuring a sustainable energy supply. This enables the steel industry to contribute to the implementation of the EU's climate and environmental protection goals.
What types of steel are produced in the electric arc furnace?
In general, special steels such as high-alloy tool steels, high-performance structural steels, engineering steels, creep-resistant structural steels or low-quality steels are preferred for the electric arc furnace. In addition, other special steels such as maraging steel, nitriding steel, cold-work steel, etc. are useful.
How much electricity does an electric arc furnace need?
An electric arc furnace is a key piece of equipment in the steel and metal industry because it provides the ability to heat large amounts of metal to very high temperatures. The energy requirements of an electric arc furnace depend on various factors, including the size of the furnace, the type of metal being melted, the desired melting capacity, and the efficiency of the furnace. However, electric arc furnaces generally require a significant amount of power to reach the required temperatures. For a typical electric arc furnace, the power requirement can range from 500 kilowatts to several megawatts. This high power consumption makes operating an electric arc furnace a costly proposition, especially in light of continuously rising energy prices. The cost of electricity consumption can account for a significant proportion of the total cost of production, which means that operators are keen to optimize energy consumption in order to reduce operating costs.
To optimize electricity consumption, many electric arc furnace operators rely on advanced technologies and processes that enable more efficient use of energy. These include, for example, the implementation of heat recovery systems that make it possible to use the heat emitted by the furnace to generate electricity or heat buildings. In addition, modern electric arc furnaces are often equipped with computer-controlled systems that enable energy consumption to be precisely monitored and controlled. This can help to optimize power consumption and improve the furnace's energy efficiency.
Another approach to reducing electricity consumption is to switch to alternative energy sources that are more environmentally friendly and cost-effective. An increasing number of electric arc furnace operators are investing in renewable energies such as solar or wind power to reduce their demand for conventionally generated electricity.
What happens in the electric arc furnace?
The electric arc furnace is used to melt metals and other electrically conductive materials. The process of electric arc melting is based on generating an electric arc between the electrodes of the furnace. This arc heats the material in the furnace to very high temperatures, causing it to melt. The electric arc furnace is widely used in the metallurgical industry to produce steel and other alloys. The melting process in the electric arc furnace allows for precise control of the melting temperature and composition of the alloy. In addition, specific properties of the end product can be influenced by adding various alloying metals. The electric arc melting process is also more energy efficient compared to other melting processes because it converts electrical energy directly into heat without the use of fossil fuels. By using recycled materials, the electric arc furnace can also contribute to the conservation of resources. After the material has been melted in the electric arc furnace, it is cast in special molds to obtain the desired final shape. The entire process in the electric arc furnace takes place under controlled conditions to ensure consistent quality of the end product. In addition, the electric arc furnace can also remove harmful substances and impurities from the material, resulting in a higher purity of the end product. Recycling metallic waste is also an important application of the electric arc furnace, as the high temperatures in the furnace help to remove most impurities and make the recycled material usable again for the production of new products. Overall, the electric arc furnace plays an important role in metallurgy and the recycling of metallic materials, as it enables efficient melting processes and can help conserve resources and reduce environmental pollution.
What is the advantage of the electric steel process?
The electric steel process offers numerous advantages that make it an attractive option for steel production. One of the most important advantages is the ability to produce high-quality steel with reduced CO2 emissions. Compared to conventional steelmaking processes, such as the blast furnace process, the electric steel process produces significantly fewer emissions, which helps to reduce the negative impact on the environment. In addition, the electric steel process enables more flexible production, as it can react more quickly to changes in demand. This results in improved adaptability and efficiency in steel production, ultimately leading to cost savings. Another advantage of the electric steel process is the ability to produce a wide variety of steel grades, including highly alloyed steel and special steels. This makes the process versatile and enables manufacturers to respond to the specific requirements of their customers. Furthermore, the electric steel process also offers advantages in terms of working conditions. Compared to other processes, there is less noise and air pollution, resulting in an improved working environment for employees. Overall, the electric steel process offers an efficient, environmentally friendly and versatile method of producing steel, making it an attractive option for steelmakers. It is important that industry recognizes these benefits and increasingly considers the electric steel route to reduce environmental impact and improve efficiency and flexibility in steel production. By choosing more sustainable and efficient methods of steel production, we can help protect our environment and ensure the long-term competitiveness of the steel industry.
What happens in a steel mill?
A steel mill is where many important processes that are needed to produce steel take place. First of all, raw materials such as iron, coal and limestone are processed in the blast furnaces to melt the iron and remove impurities. This process requires a very high temperature, often over 1500 degrees Celsius. Once the iron has melted, it is poured into various molds to shape it into the desired form. The steel is then further processed by rolling, forging or other methods to improve its strength, hardness and other properties. Throughout the entire process, various machines and systems play an important role in making production efficient and safe. Furthermore, skilled operators and engineers are essential to ensure the smooth running of production and to safeguard the quality of the end product. Finally, adhering to strict environmental protection regulations is also a central part of the steel mill process, to ensure that the impact on the surrounding environment is kept to a minimum.
Aside from the mechanical and technical aspects, the safety of employees also plays a crucial role in a steel mill. Due to the high temperatures, heavy machinery and chemical substances, there is always a certain risk of injury. It is therefore essential that strict safety protocols are followed and that employees receive regular training to avoid accidents. In addition, regular inspections and maintenance are carried out on the equipment to ensure that it operates safely and efficiently.
In addition to these technical and safety-related aspects, the economic significance of a steel mill also plays an important role. The steel industry makes a significant contribution to a country's economy by creating jobs, supporting the growth of other industries and enabling important infrastructure projects. In many countries, steel production is an essential part of the economy and plays a key role in industrial development.