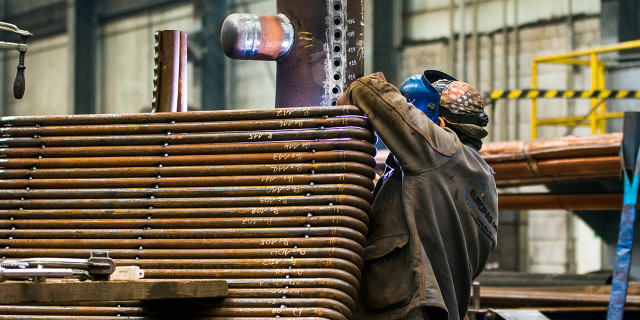
Shape metal.
Apparatus manufacturing has the longest tradition at KSK. Most of the constructions we manufacture in the area of melting and recycling units and in the area of exhaust gas cooling are designed as pipe constructions. In order to meet more specific requirements, we also regularly use special designs with cooling channels or half shells. Depending on the application, we process boiler steel, stainless steel and copper in various grades.
Table of contents
- What can KSK do for you in the field of apparatus manufacturing?
- Apparatus engineering: innovation and quality
-
Current trends in apparatus engineering
- Innovations and technological developments
- Sustainability and efficiency in manufacturing
- The importance of customized engineering solutions
What can KSK do for you in the field of apparatus manufacturing?
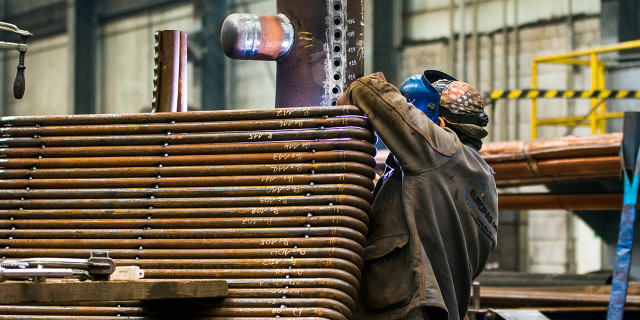
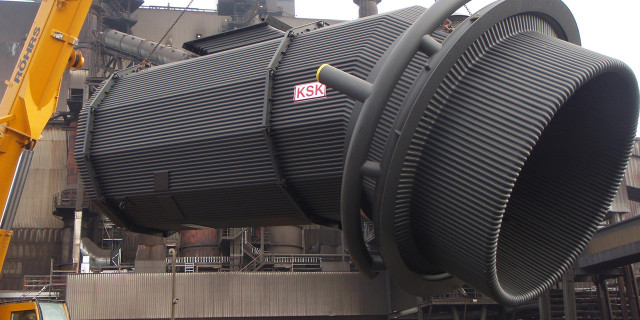
Assembly

Repairs
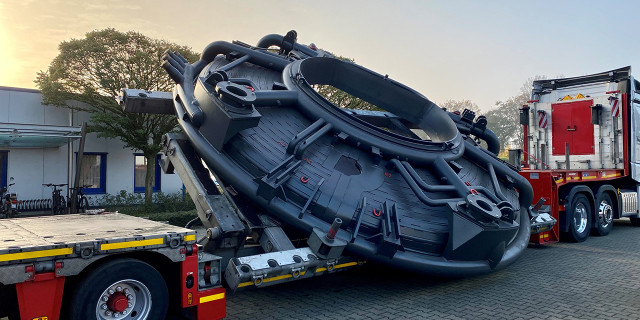
Warehousing/ Delivery of spare parts
What can KSK do for you in the field of apparatus engineering?
Apparatus engineering: innovation and quality
In the world of technology and innovation, quality and precision are at the forefront, especially when it comes to apparatus engineering. A multifaceted field that deals with the development and manufacture of complex equipment for a wide range of applications, apparatus engineering plays a crucial role in numerous industries. From the steel industry to recycling and the chemical industry, as well as energy production, the demand for high-quality, efficient and reliable apparatus is ubiquitous. In this dynamic environment, innovation and quality are not just key concepts, but indispensable pillars that guarantee the success and sustainability of the produced apparatus.
Driven by rapid technological change and increased demands for performance, safety and environmental protection, the field of equipment manufacturing has seen immense progress in recent decades. Innovative materials, advanced manufacturing techniques and digital technologies such as the Internet of Things (IoT) and artificial intelligence (AI) have opened up new horizons in equipment design and manufacturing. These developments not only enable the production of more complex and efficient equipment, but also greater flexibility in adapting to specific customer needs and requirements, as well as optimized resource efficiency and sustainability.
But innovation alone is not enough. It must go hand in hand with unrivaled quality to ensure the durability, safety and performance of the equipment. Quality management and continuous improvement processes are therefore a central component of modern equipment manufacturing. Through meticulous planning, precise manufacturing and strict quality controls, manufacturers ensure the reliability and efficiency of their products.
In this context, quality means more than just meeting technical specifications. It is about exceeding customer expectations and ensuring that every piece of equipment meets the high standards of performance, safety and cost-effectiveness.
Current trends in apparatus engineering
KSK GmbH stands for mechanical and apparatus engineering complete solutions of the highest quality. Our team of dedicated employees is continuously working on custom-made systems and containers for the individual needs of our customers. Nowadays, customer-specific solutions and economically efficient plant engineering are more in demand than ever. Our long-standing partners benefit from our expertise in container and apparatus engineering when they need pressure vessels or other components for their systems.
An important trend in apparatus engineering is the development of complete systems that are tailored to the specific requirements of our customers. From planning and design to manufacturing and assembly, we offer customized solutions that precisely meet the specifications and wishes of our customers. We place a high value on efficiency and cost-effectiveness to ensure that our systems are not only of high quality but also cost-effective.
Our company specializes in the construction of containers and apparatus that can be used in a variety of industries. Whether in the steel, recycling or chemical industry, we are able to develop customer-specific solutions that meet the diverse requirements of our partners. Our experienced employees have the necessary know-how and technical expertise to successfully implement even the most demanding projects.
Innovations and technological developments
Innovation and technological development play a crucial role in today's business world. KSK is a company that specializes in the production and servicing of state-of-the-art special apparatus. Since the company was founded 40 years ago, we have continuously worked on the development of new technologies to provide our customers with customized solutions.
At the KSK customer is the center of attention. The company strives to provide the best possible service and meet the needs of its customers. From design to manufacturing, we work closely with our customers to ensure that the machines produced meet their exact requirements.
If you are looking for a reliable and innovative solution for your production needs, look no further than KSK. With our experienced team of engineers and technicians, we are able to manufacture customized equipment that meets the individual requirements of each customer.
Sustainability and efficiency in manufacturing
Sustainability is playing an increasingly important role in all industries today. Environmentally conscious production methods are also becoming more and more important in the manufacturing industry. Sustainability refers to the idea of using resources in such a way that they are preserved in the long term and the environment is impacted as little as possible. This means that companies are increasingly turning to renewable energies, recycled materials and resource-efficient processes to reduce their ecological footprint.
Efficiency, on the other hand, refers to the optimization of production processes in order to save time and money. Efficient manufacturing processes not only help to reduce costs, but can also contribute to sustainability. By using modern technologies such as automation, networking and data analysis, companies can make their production more efficient and thus also reduce their energy consumption.
An important aspect for companies is therefore to combine sustainability and efficiency in manufacturing. By implementing resource-saving processes and simultaneously optimizing their production processes, they can achieve both ecological and economic goals. However, this requires a rethinking of the entire corporate culture and investment in new technologies and training for employees.
It is important that companies involve their suppliers and partners in the process of sustainable and efficient production. Long-term success can only be achieved if the entire value chain is sustainably positioned. Through transparent communication and close collaboration with suppliers, companies can ensure that high standards of sustainability and efficiency are maintained throughout the entire supply chain.
The importance of customized engineering solutions
Welcome to our article on the importance of customized design solutions. In today's world, it is crucial that companies are able to offer their customers tailor-made products and solutions. Standardized solutions are often insufficient, as customer requirements and needs are becoming more diverse and specific. Therefore, the individual design of products and solutions is becoming increasingly important.
Customer-specific design solutions enable companies to stand out from the competition and gain a competitive advantage. By responding to the individual requirements and wishes of customers, they can increase customer satisfaction and build long-term customer relationships. Customers appreciate it when companies are willing to meet their specific needs and offer customized solutions.
The customer-specific design solutions also ensure greater efficiency and customer benefit. By customizing products and solutions, companies can ensure that they are optimally tailored to the needs of customers and thus exceed their expectations. This not only leads to satisfied customers, but also to a strengthening of the market position and an increase in competitiveness.
In summary, the importance of customized design solutions in today's business world cannot be underestimated. Companies that are willing to respond to the individual requirements and wishes of their customers will be successful in the long term and gain a competitive advantage. Welcome to the era of customer-specific design, where the needs of the customer are the top priority and customized solutions become the standard.
Planning and construction: the cornerstones of successful projects
Careful planning and construction are the foundations of successful projects. These two steps lay the groundwork for the success of any project. Planning involves setting goals, organizing resources, and creating a schedule. It is the key to ensuring that the project is completed successfully. Construction, on the other hand, involves the actual implementation of the project, putting the planning into practice. It is important that all steps are carefully planned and executed to avoid problems and delays.
Project objectives and requirements: Before planning and constructing a project, the objectives and requirements must be clearly defined. The project objectives define what the project is intended to achieve, while the requirements define the framework for the project. It is important to ensure that all parties involved have a unified understanding of the objectives and requirements to avoid misunderstandings and ensure that the project is successfully implemented.
Team collaboration and communication: Successful planning and construction requires close collaboration and effective communication within the team. Each team member brings different skills and experiences to the table that can help to successfully implement the project. Through open communication, problems can be identified and solved early on, resulting in a smooth implementation of the project. It is important that all team members communicate regularly with each other and share information about the status of the project.
Risk management and quality assurance: During the planning and design of a project, it is important to also keep an eye on risk management and quality assurance. Risks can arise at any time and jeopardize the project, so measures should be taken at an early stage to minimize or avoid them. Quality assurance ensures that the defined standards and requirements are met and that the project delivers the desired results.
The role of planning in product development
The role of planning in product development plays a crucial role in the successful implementation of innovative and competitive products. Careful planning ensures that all aspects of the product development process are taken into account, from the initial idea to market launch. Planning makes it possible to use resources efficiently, minimize risks and manage the project workflow.
An important step in planning is the needs analysis, in which the specific requirements and wishes of the target group are determined. This serves as a basis for product conception and design. Based on this information, development goals can be defined and measures to meet these goals can be planned. The needs analysis also helps to identify possible gaps in the market or trends at an early stage and to integrate them into product development.
Technological and economic feasibility reviews are also an important part of the planning in product development. It is crucial that the planned products are both technically feasible and economically viable. Technological feasibility reviews ensure that the necessary resources are available and that the required technological developments can be carried out. In contrast, economic feasibility studies assess the potential profitability of the product and help determine the price and calculate the costs.
Time and financial planning also play a key role in product development. Realistic time planning makes it possible to set milestones, track progress and identify bottlenecks early on. Financial planning, on the other hand, helps to keep an eye on costs, create budgets and monitor the profitability of the project. Both aspects are closely related and have a significant influence on the success of a product development project.
From concept to realization: the design process
A design process usually involves several steps that are taken when developing a product or system. The initial focus is on the idea or concept. This is then recorded in a detailed design in which all the requirements and functions of the product are precisely defined. Possible materials and manufacturing processes are also determined at this stage.
The next step in the design process is model creation. This is where the product is digitally constructed using CAD software. All components are virtually assembled and checked for functionality. Initial simulations can already be carried out at this stage to identify and eliminate possible weak points or problems at an early stage.
The modeling is followed by the detailed design. This is where all the technical and geometric details of the product are finalized. Dimensions are precisely defined, tolerances are taken into account, and all components are thought through down to the smallest detail. This phase is crucial for the subsequent production and assembly of the product.
The last step in the design process is the realization. In this phase, the digital model is transformed into reality. Components are manufactured, assemblies are mounted and the finished product is tested. Any adjustments can still be made before the product goes into production. The entire design process aims to develop a product that meets the customer's requirements and wishes, while also being manufactured efficiently and cost-effectively.
Customized solutions for complex requirements
Customized solutions for complex requirements are crucial to meeting the specific needs and requirements of a company. Every company has unique challenges and goals that a standardized solution cannot always meet. Customized solutions offer the opportunity to develop tailored solutions that are precisely tailored to the needs of the company. This enables companies to work more efficiently, reduce costs and increase their competitiveness.
When developing individual solutions, the specific requirements of the company are analyzed and evaluated. This enables developers to design customized solutions that are optimally tailored to the company's needs. Individual solutions can be used in various areas, such as software development, marketing or process management. By adapting to individual requirements, the efficiency and productivity of the company can be increased.
Another advantage of custom solutions is the flexibility they offer. Standard solutions are often rigid and cannot be easily adapted to changing requirements. Custom solutions, on the other hand, can be easily modified and expanded to meet the changing needs of the business. This keeps the company agile and able to quickly adapt to new market conditions.
To successfully implement custom solutions, close collaboration between the company and the development team is crucial. Through regular communication and feedback, the developers can ensure that the solution meets the company's requirements and that all needs are met. With custom solutions, companies can optimize their processes, increase efficiency, and strengthen their competitiveness in the market.
Manufacturing techniques and materials in apparatus and container construction
The apparatus and container construction industry includes the manufacturing of tanks, pressure vessels, apparatus and pipelines for various industrial applications. In this industry, different manufacturing techniques are used to produce the required components. These include welding, forming, cutting and machining, among others. Each of these techniques has its own advantages and disadvantages and is selected based on the requirements of the project.
Materials play a crucial role in the construction of apparatus and containers. The selection of the right material depends on various factors, such as the type of liquid or gas that the container is to transport, the pressure that the components must withstand, and the temperature at which they are used. Materials commonly used in this field include stainless steel, carbon steel, aluminum, and plastics such as PTFE or PVC.
An important aspect of apparatus and container construction is quality assurance during the manufacturing of components. Various inspection methods are used to ensure that the finished parts meet the required standards. These include non-destructive testing methods such as X-ray and ultrasonic testing, but also destructive testing methods such as tensile and pressure testing.
In summary, it can be said that manufacturing techniques and materials in apparatus and container construction are closely linked and contribute significantly to the quality and safety of the manufactured components. By using appropriate techniques and materials, companies in this industry can produce durable, reliable and efficient products that meet the requirements of their customers and make an important contribution to the industrial infrastructure.
The latest manufacturing processes and their advantages
Cutting-edge manufacturing processes have undergone rapid development in recent years, offering numerous advantages for the production of all kinds of products. By utilizing state-of-the-art technologies such as 3D printing, CNC machines, and automation, companies can work more efficiently and precisely than ever before. These innovative manufacturing techniques make it possible to produce complex components in less time and with fewer rejects, resulting in improved quality and higher productivity.
In addition to time and cost efficiency, modern manufacturing processes also offer greater flexibility in production. By using computer programs and digital models, products can be quickly adapted to new requirements without the need for expensive tool changes or extensive conversions. This enables companies to react more quickly to changes in the market and to make their product portfolio more flexible.
Another major advantage of modern manufacturing processes is the ability to customize products. Thanks to advanced technologies, companies can manufacture tailor-made products that meet the specific requirements and preferences of their customers. This enables companies to stand out from the competition and offer their customers unique solutions that are tailored to their individual needs.
In addition to the advantages already mentioned, modern manufacturing processes also offer improved sustainability and environmental compatibility. By using resource-saving materials and energy-efficient processes, companies can improve their ecological balance and contribute to environmental protection. This is not only good for the environment, but can also help to strengthen a company's image and increase customer satisfaction.
Selecting materials for durability and performance
The selection of materials plays a crucial role in the durability and performance of a product. It is important to choose high-quality materials that can withstand the demands placed on them and ensure a long service life. Various factors should be considered, such as the conditions of use, the stress on the product, the environmental influences and the desired performance properties.
Materials with high durability
When selecting materials for durability and performance, it is important to favor materials with high resistance. These materials are able to optimally withstand stress and wear and are characterized by a long service life. Examples of such materials are stainless steel, aluminum alloys, titanium and special plastics.
Optimization of performance properties
To optimize the performance of a product, it is important to use materials that have certain performance properties. These include, for example, high strength, good corrosion resistance, low friction or high temperature resistance. Through the targeted selection of materials, these properties can be improved and the functionality of the product increased.
Consider the influence of environmental factors
When selecting materials for durability and performance, it is important to also consider the influences of the environment. Various environmental conditions, such as high temperatures, humidity or chemical substances, can affect the materials and negatively impact their performance. Therefore, care should be taken to select materials that meet the specific requirements of the operating environment.
Overall, the right choice of materials is crucial for the longevity and performance of a product. Using high-quality and durable materials with the right performance properties can significantly improve the functionality and lifespan of a product.
Quality assurance and standards in production
Quality assurance and standards in production play a crucial role in every production process. It is important to ensure that the products manufactured meet the highest quality standards and meet customer requirements. To ensure this, various quality assurance measures are used, including inspections, tests and audits. In addition, standards also play an important role as they serve as a guide for manufacturers to ensure that their products meet industry-specific requirements.
An important aspect of quality assurance is the control of production processes to ensure that all steps are carried out in accordance with the established standards. This includes monitoring materials, machinery and labor to ensure that no deviations occur that could affect the quality of the products. In addition, regular training is also provided for employees to ensure that they are familiar with the latest standards and techniques.
In addition to monitoring production processes, controlling the end products is also crucial. Through inspections and testing, manufacturers can ensure that their products meet the required quality standards. This includes checking dimensions, weight, materials and functionality to ensure that the products meet customer requirements.
Audits are another important tool for ensuring quality in production. Through regular reviews, manufacturers can ensure that their production processes meet the established standards and are continuously improved. In addition, audits can also help identify potential risks and take measures to improve quality. Overall, quality assurance and standards play a crucial role in production to ensure that the manufactured products meet the highest quality standards and fulfill customer requirements.
Innovative solutions and products: the way forward
Quality assurance plays a crucial role in production to ensure that the manufactured products meet the requirements and standards. It is important that all processes and steps are carefully monitored to detect and correct errors at an early stage. Consistent quality control can prevent possible defects and reduce production costs. In addition, high product quality contributes significantly to customer satisfaction and strengthens trust in the company.
To meet these requirements, standards are set in production that serve as guidelines and specifications. These production standards define how certain processes are to be carried out in order to ensure consistently high product quality. Among other things, standards and certifications are taken into account to ensure comparability and compatibility with other products.
Adherence to these production standards is regularly reviewed and controlled by quality audits. These involve analyzing and evaluating the processes, procedures and results in order to identify potential improvements. If deviations from the standards are detected, corrective and optimization measures are initiated to ensure the quality of the products.
In addition to internal quality assurance, cooperation with suppliers and external partners also plays an important role. High quality standards are set and monitored by means of quality management agreements and standards. Close communication and cooperation with external partners is crucial to ensure smooth production and a high quality standard. Only consistent compliance with quality standards and a continuous improvement process can ensure sustainable product quality and customer satisfaction.
Development of new products for various applications
The development of new products for various applications is a crucial step for companies to remain competitive and meet the needs of their customers. Innovation and creativity play an important role in meeting the increasing demands of the market. Through targeted product development, companies can open up new markets, increase their sales and strengthen their competitive position.
A structured approach is necessary to successfully develop new products for various applications. First, the requirements and needs of the target group should be analyzed in detail. Then, ideas that meet these requirements and offer real added value for customers should be generated. These ideas must then be carefully examined and evaluated to ensure that they are technically feasible and economically viable.
Close collaboration between different departments within a company is also an important aspect of the new product development process. By taking an interdisciplinary approach, different perspectives and skills can be combined to develop innovative solutions. For example, engineers, designers and marketers can work together on new product development to ensure that both technical and aesthetic as well as market-relevant aspects are taken into account.
The rapid pace of technological development and constant change in many industries requires companies to be highly flexible and adaptable. It is therefore important to continuously invest in the development of new products and to actively engage with current trends and developments. Only in this way can companies successfully survive in the market in the long term and ensure their competitiveness.
Adapting to market needs and future challenges
Adapting to market needs is crucial for companies to be successful in the long term. This requires an in-depth understanding of customer needs and expectations, as well as the ability to respond quickly to changes in market dynamics. Companies that fail to adapt run the risk of being overtaken by the competition and ultimately failing in the market. It is therefore important to constantly analyze the market and adapt your products and services accordingly.
The future challenges that companies face are diverse and complex. In addition to the constantly changing market environment, technological developments, legal framework conditions and demographic changes also play a role. Companies must be able to proactively address these challenges and take timely action to stay ahead of the competition. A sustainable company is characterized by flexibility, innovative strength and adaptability.
One way to adapt to market needs and meet future challenges is to implement a long-term strategy. This should take into account both the current needs of customers and possible future developments. Regular review and adjustment of the strategy is required to ensure that the company stays on track and remains successful in the long term.
Another important aspect of adapting to market needs and future challenges is investing in employee training and development. Only well-trained and qualified employees are able to meet the growing demands of the market and drive innovation. Companies should therefore invest in the development of their employees and ensure that they have the skills and knowledge needed to meet the challenges of the future.
Investment in research and development for technological progress
Investment in research and development is crucial for a country's technological progress and competitiveness. Continuous support for innovation can lead to the development of new products and services that better meet the needs of society and open up new markets. In addition, research and development helps to increase the efficiency of production processes and optimize the use of resources.
To achieve long-term success, it is important that both the public and private sectors invest in research and development. The state can create incentives through targeted funding programs to encourage companies to invest in innovation and develop new technologies. At the same time, companies should establish their own research departments or work with external research institutions to expand their expertise and remain future-proof.
Over the past few decades, technological progress has led to groundbreaking developments in areas such as information technology, biotechnology and renewable energies. By investing in research and development, new opportunities can be discovered that improve people's daily lives and help solve global challenges. Innovation is key to sustainable growth and job creation in a constantly changing world.
To remain competitive in the long term, it is therefore essential that countries invest in research and development and promote a culture of innovation. By creating incentives for companies and research institutions to invest in new technologies, governments can help their country to succeed in the global competition for the best ideas and talent. Only through continuous investment in research and development can progress and prosperity be secured in the long term.
Boilers and pressure vessels
Apparatus engineering is a branch of mechanical engineering (related to plant engineering) and deals with the design, manufacture and construction of special apparatus. The design and manufacture of apparatus requires extensive knowledge of manufacturing theory, materials science, fluid mechanics and construction theory. In apparatus engineering, containers are usually manufactured whose parts and components consist of different materials. In many cases, the devices are used in technological processes such as steel production, recycling or energy. At KSK, we have been supplying special designs in the field of apparatus engineering for almost 40 years. Our devices not only consist of a tubular body, but are also heat exchangers and pressure vessels or steam boilers.
In apparatus engineering, the pressure vessel is defined by a specific function (storing, filtering, heat transfer). In particular, pressure vessels are closed containers in which the internal pressure is higher than the ambient pressure. A pressure vessel is a closed container that contains a liquid or a gas. The operation of pressure vessels is specified for a particular installation location. Steam boilers are used to generate steam or hot water (over 110 °C) using a furnace, an electric heater or waste heat. Pipelines that transport liquid are not pressure vessels. Pressure vessels of various sizes and shapes are manufactured for different purposes. Classic pressure vessels are preferably spherical, conical or cylindrical in shape. A typical design in apparatus engineering is the combination of a long cylinder with two bases. If you compare this form of apparatus engineering with the special apparatus of the KSK – for example with a hot gas line – it is noticeable that our apparatus engineering manages without bottoms at first glance and often does not even represent a closed body. So how can it be a pressure vessel in the sense of apparatus engineering? The solution is simple: the actual container is not the body (usually) formed from pipes, but the piping itself. These act as heat exchangers between the flue gas and the water flowing through them and are under pressure because in 99% of cases they are in a closed cooling circuit.
Trust is good, verification is better
A central component in apparatus engineering is the production and assembly of containers. The production of pressure vessels or vacuum containers must meet the strictest safety requirements, which are regulated, among other things, in the Pressure Equipment Directive 2014/68/EU (harmonization of the legal provisions of the member states regarding the provision of pressure equipment on the market, defines the requirements for pressure equipment for placing on the market within the European Economic Area). At KSK, pressure vessels fall into two main categories of the Pressure Equipment Directive:
“Sound engineering practice” according to Article 4, Paragraph 3 of the DGRL means that the pressure equipment has been designed taking into account all relevant factors that influence its safety.
Category IV, Module G (individual testing)
Individual testing ensures the highest possible product safety and versatility. The notified body checks the technical documentation and approves the pressure equipment. Upon positive test results, the notified body issues a certificate of conformity. This is the basis for the manufacturer to issue a declaration of conformity and CE marking. Prior to construction, the manufacturer must submit full-size drawings for approval by the purchaser and the inspection agency. In addition to dimensions and thicknesses, these drawings must include the following information:
- Welding procedure for application
- Important welding details
- Heat treatment processes applied
- Non-destructive testing requirements
- Test pressure
Manufacturers involved in apparatus engineering are often required to maintain a material identification system so that all materials in the finished pressure vessel can be traced. During apparatus engineering, each pressure vessel must be inspected by a notified body. The standard specifies the steps from receipt of raw materials to packaging of finished products for the agency to review. For example, a customer may request further examination of the internals. The manufacturer must specify the welding procedures used in the fabrication of the pressure vessel and provide test pieces representative of the material and thickness used in the actual pressure vessel. The inspection agency generally oversees the preparation and testing of these test items, unless certified test items are already available. Welders must pass a certification test in apparatus engineering to show that they can produce welds that are identical to those in a real vessel. An accredited certification body certifies these certificates for welders in apparatus engineering.
FAQs on apparatus engineering
Table of contents
- Q: What is apparatus engineering?
- Q: What services can you expect from KSK?
- Q: How do I find the right partner for my apparatus engineering project?
- Q: What makes a good partner for apparatus engineering?
- Q: How important is certification for an equipment manufacturing company?
- Q: When do companies need the services of an apparatus engineering company?
- Q: Why is it beneficial to work with a local heat exchanger company?
- Q: What trends are influencing modern apparatus engineering?
- Q: How do you welcome new partners in equipment manufacturing?
Q: What is apparatus engineering?
A: Apparatus engineering involves the development, design and manufacture of devices, apparatus and systems that are used in various industries. These range from the chemical and pharmaceutical industries to food technology and energy production. Typical examples of apparatus in apparatus engineering are pressure vessels, heat exchangers, columns, mixers, agitators, dryers, filters and pumps. These devices are used to carry out various processes such as mixing, separating, heating, cooling or processing substances.
In apparatus engineering, close cooperation between engineers, designers, technicians and skilled workers is essential to develop customized solutions for the respective requirements. Aspects such as safety, efficiency, economy and environmental protection must be taken into account.
Apparatus engineering is an important area in industry because many production processes can be optimized and improved by using specially manufactured apparatus. With the increasing digitalization and automation, topics such as Industry 4.0 and Smart Factory are also playing an increasingly important role in apparatus engineering.
Overall, it can be said that apparatus engineering is a versatile and demanding field of work that represents an important interface between engineering, technology and production.
Q: What services can you expect from KSK?
A: From KSK, you can expect a comprehensive range of services, from consulting and planning to manufacturing, assembly and commissioning, as well as customer service and maintenance of the manufactured apparatus and systems. Furthermore, you can also get customized solutions for special requirements from KSK, tailored to your needs. These include, for example, special designs, adaptations or conversions of existing systems.
We have many years of experience and expertise in the field of apparatus and plant engineering and can therefore guarantee you high quality and reliability in the implementation of your projects.
In addition, KSK is also able to comply with all legal requirements and standards to ensure the safety and environmental compatibility of the manufactured apparatus and plants.
Overall, you can expect professional and comprehensive support for your projects from KSK, ranging from planning to maintenance and servicing.
Q: How do I find the right partner for my apparatus engineering project?
A: The right partner for your apparatus engineering project should have extensive experience in your specific field of application. They should also be able to provide references that demonstrate the quality and reliability of their work. Open communication and transparency in all phases of the project are equally important. In addition, the potential partner's technical capabilities and innovative strength play a crucial role. It is important to ensure that they have the necessary expertise and resources to successfully implement your project.
Another important aspect is adhering to deadlines and budgets. A reliable partner should be able to create and stick to realistic timetables and cost estimates.
Finally, collaboration on a personal level is also crucial. A good partner should be able to respond to your individual needs and requirements and communicate with you on an equal footing.
Overall, it is important to choose a partner that not only has the necessary know-how and technical capabilities, but also shares the values and goals of your organization. A long-term and successful partnership is based on trust, transparency and a shared vision.
Q: What makes a good partner for apparatus engineering?
A: A good partner for apparatus engineering is characterized by technical expertise, industry experience, a high level of quality assurance, and flexibility in project implementation. In addition, the ability to develop customized solutions and provide comprehensive after-sales service is essential. A good partner in apparatus engineering has an experienced team of engineers and technicians with extensive knowledge in the field of apparatus and plant design. They should be able to understand individual customer requirements and develop customized solutions that meet the specific requirements of the industry.
Furthermore, it is important that a good partner has a quality assurance system in place that ensures all products meet the required standards and processes are carried out efficiently and reliably. This is particularly crucial in industries such as food or pharmaceuticals.
Flexibility in project implementation is also an important aspect, as customer requirements can change frequently and prompt adjustments may be needed. A good partner should be able to respond quickly to changes and provide effective solutions without compromising on quality.
Finally, comprehensive after-sales service is essential to ensure that customers are supported in the event of problems or questions and that products function reliably over the long term. A good equipment manufacturing partner should therefore offer reliable customer service that can be reached quickly when needed and provide efficient solutions.
Q: How important is certification for an equipment manufacturing company?
A: The certification of an apparatus engineering company is very important because it certifies compliance with certain quality standards and norms. This gives customers peace of mind regarding the quality, safety and reliability of the products and services. Through certification, companies can also strengthen their competitiveness and stand out from competitors. In addition, certifications can facilitate market access requirements for certain industries and markets.
A certified apparatus manufacturing company demonstrates that it has established quality management processes to meet production, warehousing, delivery and customer service requirements. This can help minimize errors and failures and increase customer satisfaction.
The most common certifications for apparatus engineering companies include ISO 9001 certification for quality management, ISO 14001 certification for environmental management, and OHSAS 18001 certification for occupational health and safety.
Overall, certification of an apparatus engineering company is an important step in building trust with customers and other stakeholders and increasing competitiveness.
Q: When do companies need the services of an apparatus engineering company?
A: Companies need the services of an apparatus engineering company when they require individually manufactured apparatus, machines or plants that are specially tailored to their specific production or processing procedures, or when existing plants need to be optimized or expanded. Apparatus engineering companies offer customized solutions for various industries, including the food and beverage industry, the chemical industry, the pharmaceutical industry, environmental technology and many more. They can help improve efficiency and production processes, reduce costs and increase the quality of manufactured products.
An apparatus engineering company has specialized engineers, technicians and skilled workers who have the necessary know-how and experience to develop and implement individual solutions. They work closely with their clients to understand their requirements and specific needs and to produce high-quality apparatus, machines or plants.
The services provided by an apparatus engineering company include the planning, design, production, assembly and commissioning of individually customized solutions. They also offer maintenance and repair services to ensure that the plants function optimally and last a long time.
Overall, heat exchanger companies are important partners for companies that require customized solutions to optimize their production processes and remain competitive. They play a crucial role in developing innovative and efficient solutions to meet the increasing demands and challenges in various industries.
Q: Why is it beneficial to work with a local heat exchanger company?
A: Working with a local apparatus engineering company can have several advantages, including short distances for meetings and possible adjustments, better knowledge of local regulations and standards, and possibly lower transport costs for the delivery of the manufactured apparatus and plants. Furthermore, working with a local apparatus engineering company can offer the opportunity to benefit from their expertise and experience in the field of apparatus engineering technology. Through direct contact and proximity to the company, any problems or difficulties can be solved faster and more efficiently.
Another advantage is the promotion of the local economy and the support of small and medium-sized companies. By working with a local company, long-term business relationships can also be established that are characterized by trust and reliability.
In summary, working with a local apparatus engineering company offers many advantages that can be important for both your own company and the local economy. It is therefore worth considering the option of working with a local partner.
Q: What trends are influencing modern apparatus engineering?
A: Trends influencing modern equipment manufacturing include digitalization and automation, the use of advanced materials, improving energy efficiency and sustainable production, and the increasing integration of Internet of Things (IoT) technologies to monitor and optimize plant performance. Digitalization enables the networking of machines and equipment, resulting in improved productivity and efficiency. Automation technologies such as robotics and artificial intelligence make it possible to optimize processes and increase production capacity. The use of advanced materials such as carbon fiber or aluminum alloys reduces the weight of the equipment and increases its lifespan.
Improving energy efficiency is an important aspect of modern equipment manufacturing in order to reduce energy consumption and minimize environmental impact. Sustainable production techniques such as recycling and reusing materials also help to reduce environmental impact.
The integration of IoT technologies enables real-time monitoring and control of equipment to detect problems early and optimize plant performance. By analyzing data, processes can be further improved and maintenance intervals extended, resulting in higher plant availability.
Overall, these trends are helping to make modern equipment manufacturing more efficient, sustainable and connected in order to meet the increasing demands of industry.
Q: How do you welcome new partners in equipment manufacturing?
A: We welcome new partners in equipment manufacturing with a comprehensive introduction to our processes, capacities and projects realized to date. We value transparent communication and a collaborative partnership from the outset in order to achieve the best results together. We are proud to work with state-of-the-art machines and qualified employees to meet the most demanding requirements of our customers. We are open to new ideas and innovations and look forward to working with you to implement successful projects together. Welcome to our network and to a successful collaboration!