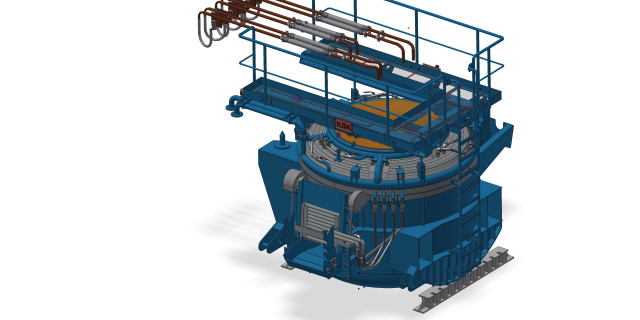
Table of contents
- What can KSK Analyse Planung Design do for you in the field of 3D surveying?
- Your contact
- What is 3D measurement and how does it work?
- Why is accuracy crucial in 3D measurement?
- What advantages does 3D scanning offer for industry?
- How does optical measurement of components work?
- How can you decide on 3D measurement services?
What can KSK Analyse Planung Design do for you in the field of 3D surveying?
Take measurements.
Our measurements in industrial environments and of large components or machines are extremely accurate—down to the millimeter, to be precise. In most cases, we use our Faro X30 3D scanner. It delivers detailed images that can be integrated into common CAD systems for further evaluation and planning. This allows you and us to start planning right away. Costly planning errors are reduced to a minimum and our joint projects are accelerated. You, your team, and your potential customers benefit from simplified communication thanks to the visualization of realistic 3D models of the actual situation.
Gain clarity
Are you standing in your plant with drawings from the last century and simply can't figure out where which pipe leads? To remedy this, we can offer you the following services in the field of 3D scanning:
- Inventory of plants, components, and machines and transmission of the original point cloud
- Creation of as-built models
- Support with conversions and extensions
- Documentation for maintenance and repair.
Your contact
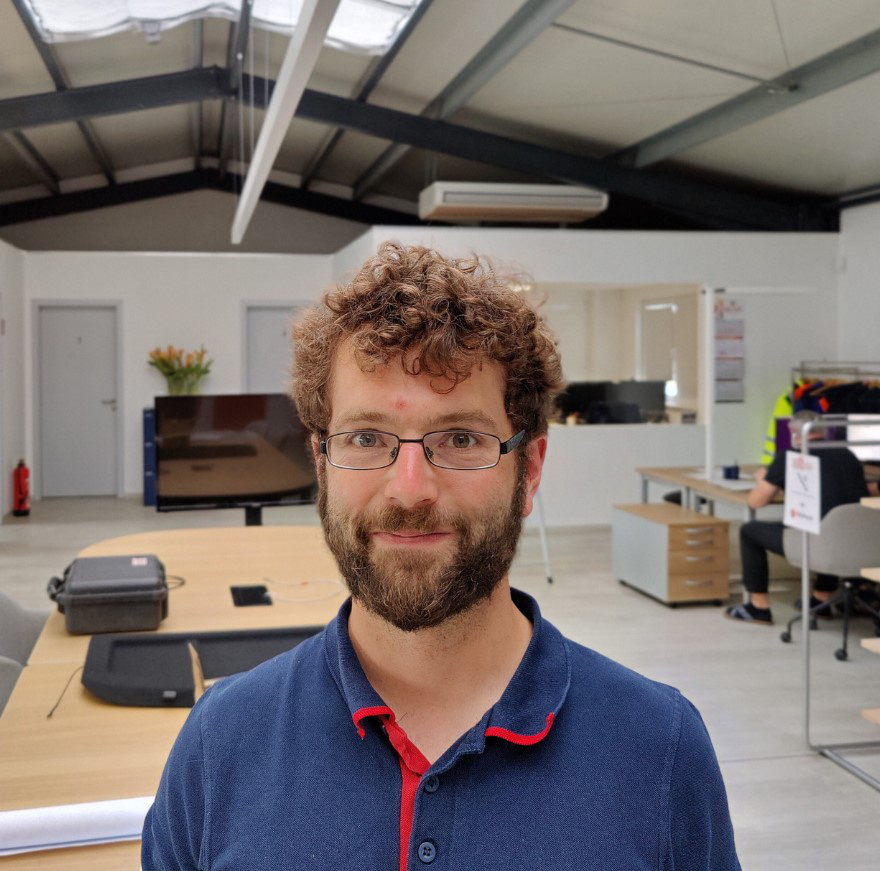
Florian Röhl, M. Eng.
Project Engineer
+49 (0) 2364 10539-22
What is 3D measurement and how does it work?
The precision of 3D measurement: Optical measurement of components
In the modern industrial world, 3D surveying has become an indispensable tool. This advanced technology enables components to be captured with the highest precision and accuracy, resulting in a significant improvement in quality assurance and efficiency in production. Optical measurement of components offers a non-contact method for creating detailed 3D models that can be used as a basis for various applications.
How does 3D measurement differ from conventional methods?
3D measurement differs fundamentally from conventional measurement techniques in that it enables three-dimensional capture of objects. While traditional methods often require physical contact points to collect measurement data, 3D measurement uses optical and laser-based technologies to scan the surface of an object without contact. These methods are not only faster, but also provide a more accurate capture of the geometry, minimizing deviations.
What technologies are used in 3D scanning?
Various technologies are used in 3D scanning, including laser scanning and optical scanners. Laser scanners use a laser beam to scan the surface of an object and generate a point cloud that forms the basis for a 3D model. Optical scanners, on the other hand, use cameras and projection techniques to capture detailed images of the surface. Both technologies enable fast and accurate data capture and are crucial for the creation of CAD models.
How is a 3D model created through measurement?
The creation of a 3D model begins with scanning the physical object to generate a point cloud. This point cloud serves as a digital representation of the object's surface and is then processed in a CAD program. There, the data is further modeled and edited to create an accurate 3D model. This allows engineers and designers to perform detailed analyses and make precise adjustments.
Why is accuracy crucial in 3D measurement?
How do you achieve precise measurement results?
Precise measurement results are crucial in many industrial applications, especially when it comes to quality assurance and tolerance compliance. Accuracy is achieved through the use of advanced scanners and calibration techniques. Regular quality controls and adapting the measurement technology to the specific requirements of the project also help to ensure maximum accuracy.
What role does quality control play in 3D measurement?
Quality control plays a central role in 3D measurement, as it ensures that the data collected meets the specified standards. Regular checks and calibrations of the measuring equipment ensure that the measurement results are accurate and reliable. This is particularly important for minimizing deviations and ensuring the integrity of the 3D models.
How is accuracy ensured in the optical measurement of components?
Accuracy in the optical measurement of components is ensured through the use of high-precision optical 3D scanners. These scanners capture the surface of the component in detail and digitize it in high resolution. By combining modern optics and advanced data acquisition technology, precise 3D models can be created that correspond to the real geometries of the components.
What advantages does 3D scanning offer for industry?
How does 3D scanning support reverse engineering?
3D scanning is a crucial tool for reverse engineering because it enables the exact capture of existing objects. By creating detailed 3D models, engineers can analyze and replicate the structure and function of a component. This technology makes it possible to digitize inventory plans and transfer physical objects into CAD models, which facilitates the redesign and improvement of existing products.
How can companies work more efficiently with 3D measurement?
3D measurement enables companies to work more efficiently by accelerating the design and production process. By accurately capturing components, companies can respond quickly to changes and make adjustments without having to create physical prototypes. This not only saves time and money, but also improves the quality of the end products through faster iterations and fewer errors.
Which industries benefit most from 3D scanning?
Various industries benefit significantly from integrating 3D scanning into their processes. The steel and recycling industries in particular use these technologies to analyze and develop complex components and systems.
How does optical measurement of components work?
What types of 3D scanners are available?
There are different types of 3D scanners, each suitable for specific applications. The most common are laser scanners, which scan the surface of an object using a precise laser beam, and optical scanners, which use cameras and projection techniques to capture detailed image data. These scanners differ in their range, accuracy, and the applications for which they are best suited.
How is the surface of a component captured?
The surface of a component is captured by scanning it with a 3D scanner, which digitally captures the geometry of the object in the form of a point cloud. This point cloud consists of thousands of points that map the surface of the component in detail. This data is then processed in software to create a complete 3D model that can be used for further analysis and applications.
How does optical measurement contribute to the creation of CAD models?
Optical measurement plays a crucial role in the creation of CAD models, as it enables the precise digital reproduction of the physical geometry of a component. By capturing surface features and shapes with high accuracy, detailed CAD models can be created that serve as the basis for design changes, simulations, and manufacturing processes. These models are essential for developing new products and optimizing existing designs.
How can you decide on 3D measurement services?
How can our customers benefit from customized 3D measurement solutions?
Our customers benefit from customized 3D measurement solutions that are tailored to their individual requirements. By adapting the measurement technology to specific projects, accurate and efficient results can be achieved. This leads to improved product quality and a reduction in time and costs in the development process. We offer comprehensive services ranging from data acquisition to the creation of CAD models.
What expertise is required to perform 3D scans?
Performing 3D scans requires in-depth expertise in the fields of measurement technology, data processing, and CAD modeling. Our specialists are able to efficiently capture the data and convert the raw data into usable 3D models. In addition, a deep understanding of quality control and the specific requirements of the industry is necessary to deliver accurate and reliable results.
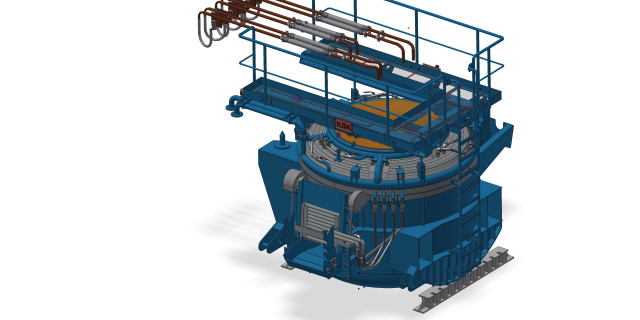
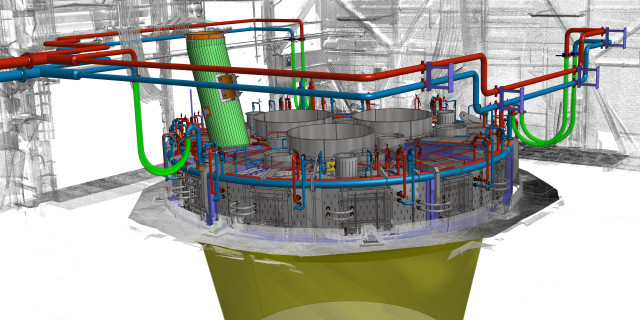
Engineering Office
Table of contents
- Q: What is 3D surveying?
- Q: How does a 3D scanner work?
- Q: What are the advantages of 3D measurement?
- Q: Where is 3D surveying used?
- Q: How accurate are 3D scans?
- Q: Can large objects also be measured with 3D scanners?
- Q: What is the difference between 3D laser scanning and optical 3D measurement?
- Q: How can I have a 3D model created?
- Q: What role does CAD play in 3D surveying?
Q: What is 3D surveying?
A: 3D surveying is the process of accurately capturing objects and environments in three dimensions. This is usually done using technologies such as 3D scanners, which create detailed digital models. 3D surveying is the process of accurately capturing objects and environments in three dimensions. This is usually done using technologies such as 3D scanners, which create detailed digital models. This technology is used in numerous industries, including construction and engineering.
In construction, it helps to monitor the progress of a project and ensure that all components are positioned accurately. In industry and engineering, 3D surveying is used to create prototypes, refine product designs, and improve quality assurance. By accurately capturing dimensions and shapes, companies can ensure that their products meet the highest standards.
Overall, 3D measurement offers a wide range of opportunities to increase precision, efficiency, and creativity in various fields. As this technology continues to develop, its applications and influence will continue to grow, creating new opportunities for innovation and improvement.
Q: How does a 3D scanner work?
A: A 3D scanner measures an object by emitting laser beams or light patterns and capturing the reflected signals. This data is then processed to create a digital 3D model of the object. A 3D scanner measures an object by emitting laser beams or light patterns and capturing the reflected signals. This data is then processed to create a digital 3D model of the object.
After the raw data has been captured by the scanner, a series of processing steps takes place. First, the point clouds that describe the surface of the object are cleaned up and optimized to remove noise and unwanted artifacts. This can be done using algorithms that filter out outliers and adjust the density of the points to ensure a more even distribution.
The point clouds are then registered. If the object has been scanned from multiple angles, the different scans must be correctly aligned with each other. This is done by detecting overlapping areas and adjusting the point clouds so that they fit together seamlessly.
The next step is network generation. This involves converting the point clouds into a polygon mesh that describes the surface of the object. These meshes consist of many small triangles that together reproduce the shape of the object. The density of the mesh can vary depending on the application, with more detailed models requiring more triangles.
Once the 3D model has been created, it can be further processed or analyzed. In industry, for example, it is used for quality control, prototyping, or reverse engineering.
Overall, 3D scanning technology offers a wide range of possibilities for digitally capturing and processing real objects, leading to innovation and efficiency gains in many areas.
Q: What are the advantages of 3D measurement?
A: 3D measurement offers advantages such as high precision, efficiency, and the ability to quickly and accurately capture complex geometries and hard-to-reach locations. This enables accurate modeling and analysis of the captured objects and environments. By using 3D measurement technologies such as laser scanning and photogrammetry, detailed digital models can be created for use in various industries. In industry, companies benefit from 3D measurement by optimizing production processes and quality controls.
Overall, 3D surveying helps save time and money while increasing accuracy and efficiency in numerous areas of application.
Q: Where is 3D surveying used?
A: 3D surveying is used in many areas, including engineering, component measurement, and the creation of 3D CAD models. 3D measurement is used in many areas, including construction, engineering, component measurement, and the creation of 3D CAD models. This technology enables the precise capture of spatial data, which is crucial for the planning and execution of projects. In architecture and construction, 3D surveying can be used to create accurate models of buildings and construction sites, which greatly facilitates planning and visualization. Engineers use this data to analyze and optimize structures, while component measurement captures the exact dimensions and shapes of components to ensure high manufacturing accuracy.
Overall, 3D surveying offers numerous advantages, including greater accuracy, efficiency, and the ability to convert complex data into understandable visual information, which supports and improves decision-making in various industries.
Q: How accurate are 3D scans?
A: 3D scans are extremely accurate and can capture details down to a fraction of a millimeter. The accuracy depends on the scanner used and the specific requirements of the project. 3D scans are extremely accurate and can capture details down to a fraction of a millimeter. The accuracy depends on the scanner used and the specific requirements of the project. High-quality scanners can even capture the finest details and textures.
In industry, 3D scans are often used for quality control and reverse engineering. By accurately capturing components, deviations from specifications can be quickly identified and corrected. In architecture, 3D scans enable the precise documentation of buildings and structures, which is particularly advantageous in restoration projects.
Choosing the right 3D scanner depends on various factors, including the size and complexity of the object, the required resolution, and the working environment. There are different technologies such as laser scanning, structured light, and photogrammetry, each with its own advantages and disadvantages.
In the future, advances in 3D scanning technology could lead to even more accurate and faster scans, which could further increase the range of applications and open up new areas of use.
Q: Can large objects also be measured with 3D scanners?
A: Yes, modern 3D scanners are capable of measuring both small and large objects efficiently and accurately. This enables the creation of digital models of the highest quality. Yes, modern 3D scanners are capable of measuring both small and large objects efficiently and accurately. This enables the creation of digital models of the highest quality. Through the use of advanced technologies such as laser scanning, structured light, or photogrammetry, even complex surfaces and structures can be captured in detail.
In addition, continuous advances in 3D scanning technology are promoting the development of portable and user-friendly devices that can also be used in smaller businesses or even in the private sector. This democratization of technology is opening up new opportunities for innovation and creativity in various disciplines.
Q: What is the difference between 3D laser scanning and optical 3D measurement?
A: 3D laser scanning uses laser beams to measure distances, while optical 3D surveying uses light patterns. Both methods are efficient and accurate, but laser scanning is particularly suitable for longer distances. 3D laser scanning uses laser beams to measure distances, while optical 3D surveying uses light patterns. Both methods are efficient and accurate, but laser scanning is particularly suitable for longer distances.
Laser scanning has the advantage of being able to create highly detailed and accurate models of large and complex structures. This makes it ideal for applications in architecture, construction planning, and historic preservation, where large buildings or landscapes often need to be captured. The technology is also capable of working effectively in low-light conditions or in areas that are difficult to access.
Optical 3D surveying, on the other hand, is particularly useful for smaller objects or when a quick and cost-effective solution is required. This method is often used in quality control, reverse engineering, and product development because it offers high accuracy in capturing surface details.
In the future, both technologies are expected to continue to evolve and improve, with advances in sensor technology and data processing enabling even more precise and faster measurements. This will expand the range of applications and open up new opportunities in various industries.
Q: How can I have a 3D model created?
A: To have a 3D model created, you can contact specialized service providers who perform 3D scans and use the data for modeling. Contact us today for more information. To have a 3D model created, you can contact specialized service providers who perform 3D scans and use the data for modeling. Contact us today for more information.
If you are interested in the process, we would be happy to explain the individual steps to you. First, a 3D scan of your object or environment is performed. This involves the use of state-of-the-art technologies such as laser scanners or photogrammetric methods to capture accurate and detailed data.
After scanning, the raw data is imported into special software programs that process it and convert it into a digital 3D model. Adjustments and optimizations can also be made at this stage to ensure that the model meets your requirements.
Finally, the finished 3D model is exported in the format you require, whether for construction, simulation, or other applications. Our experts are available throughout the entire process to ensure that you receive a high-quality end product.
Please do not hesitate to contact us to discuss your project and receive a customized quote. We look forward to helping you realize your 3D projects.
Q: What role does CAD play in 3D surveying?
A: CAD (Computer Aided Design) plays a central role in 3D surveying as it enables the processing and visualization of the scanned data. It helps to create and analyze precise digital models. CAD (computer-aided design) plays a central role in 3D surveying, as it enables the processing and visualization of scanned data. It helps to create and analyze precise digital models. CAD software allows engineers and designers to work more efficiently by modeling complex geometries and checking the accuracy of components.
The integration of CAD into the 3D surveying process makes it possible to combine data from different sources, such as 3D scanners or laser measuring devices, and display it in a unified model. This promotes collaboration between different departments and disciplines, as everyone involved has access to the same accurate information.
In addition, CAD offers advanced simulation and analysis tools that help optimize design decisions. For example, material properties and stress tests can be performed in the virtual environment to evaluate the durability and performance of a product before it goes into production.
Another advantage of CAD in 3D surveying is the ability to make changes and adjustments quickly without having to create physical prototypes. This saves time and money and enables rapid iteration and improvement of design concepts.
In the manufacturing industry, CAD not only ensures greater precision and efficiency, but also contributes to innovation by paving the way for new design possibilities and more complex structures. The continuous development of CAD technologies and their integration with technologies such as artificial intelligence and augmented reality also opens up new perspectives for the future of 3D measurement and design.