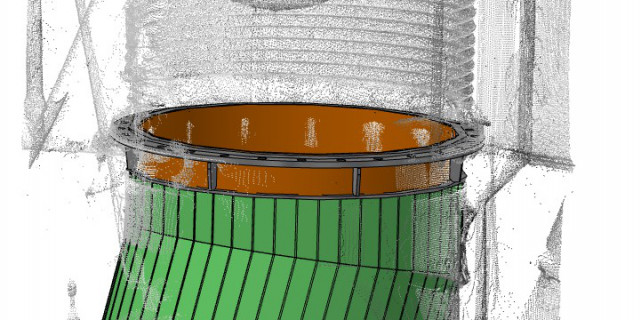
Table of contents
-
What can KSK Analyse Planung Design do for you in the field of failure analysis?
- Investigate causes.
- Record findings.
- Initiate investigation.
- Deriving results.
- Your contact person (KSK)
- Your contact person (StandZeit)
What can KSK Analyse Planung Design do for you in the field of failure analysis?
Investigate causes.
Your component has been damaged. You were able to repair the damage quickly and assure the production team that operations could resume, but what happens next? Will similar damage occur elsewhere? Was the repair measure sufficient?
The crucial question is: What caused the damage?
Our experts from KSK Analyse Planung Design, together with our partner company StandZeit GmbH from Coesfeld, will be at your side to help you determine the causes. Our colleagues at StandZeit are specialists in the field of materials testing and have decades of experience in the power plant and waste incineration industry, among others.
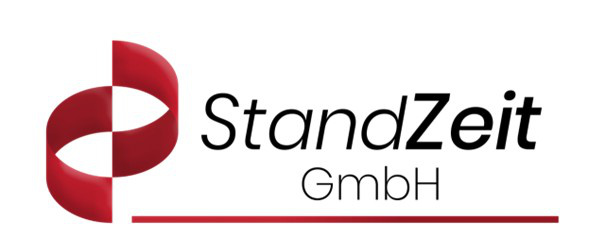
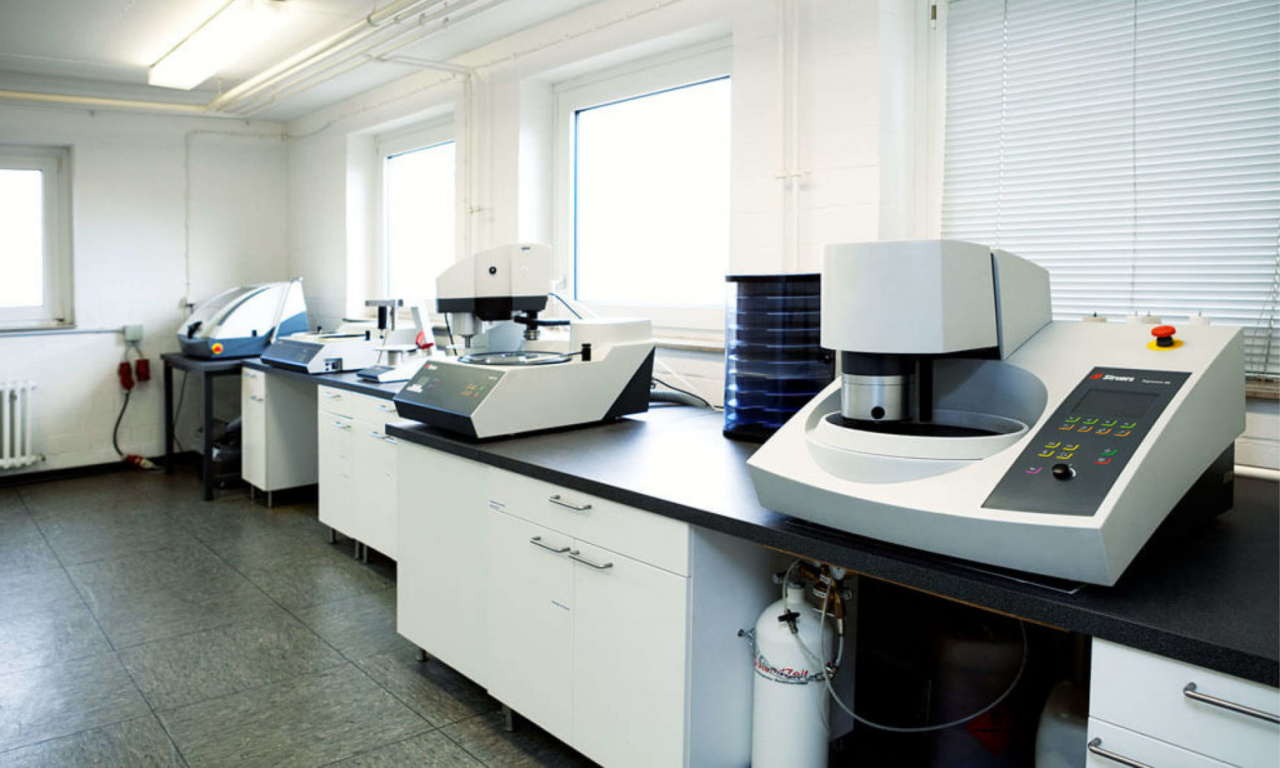
Record findings.
After damage occurs, the following three points, among others, must be considered when determining the cause of the damage:
1.) Determining the actual primary damage area, which is often overlaid by numerous secondary damages.
2.) Cutting out and sending the damaged areas under the guidance of our experts.
3.) Providing further information, such as operating parameters or indications of previous damage.
In some cases, it makes sense to have our experts carry out the on-site inspection, especially if further examinations of neighboring components can be carried out at the same time.
Initiate investigation.
During the laboratory investigation, StandZeit relies on the most modern preparation and investigation methods, which are constantly kept up to date by partner companies.
Using semi-automatic preparation machines also allows us to examine a larger number of samples in a short period of time. We are always on the lookout for damage characteristics using the latest analysis equipment, such as scanning electron microscopy and confocal laser scanning microscopy. Both in the microstructure and in the chemical composition. Nothing remains hidden.
Deriving results.
The damage pattern is pieced together step by step like a puzzle from the results of the on-site inspection, the information from the production and design, and the materials testing of the damaged component in the materials laboratory. Based on the damage characteristics determined, the damage mechanism is derived first, followed by the actual causes of the damage.
We then discuss the results of the investigations with you and our experts and derive measures and recommendations for the future operation of your components.
Your contact person (KSK)
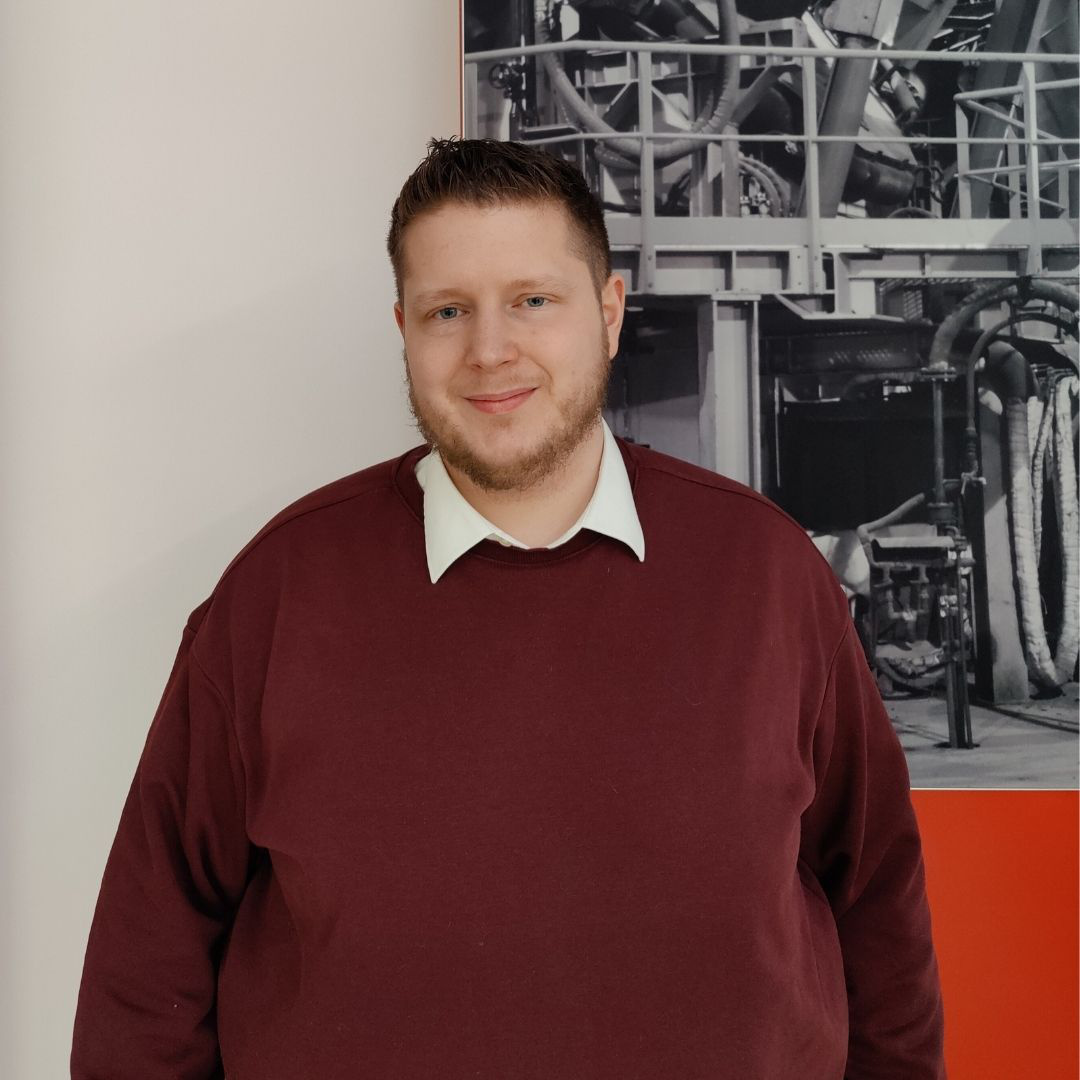
M.Sc. Björn Brüningk-Weißhar
Head of Engineering
+49 (0) 2364 60897 -20
Your contact person (StandZeit)
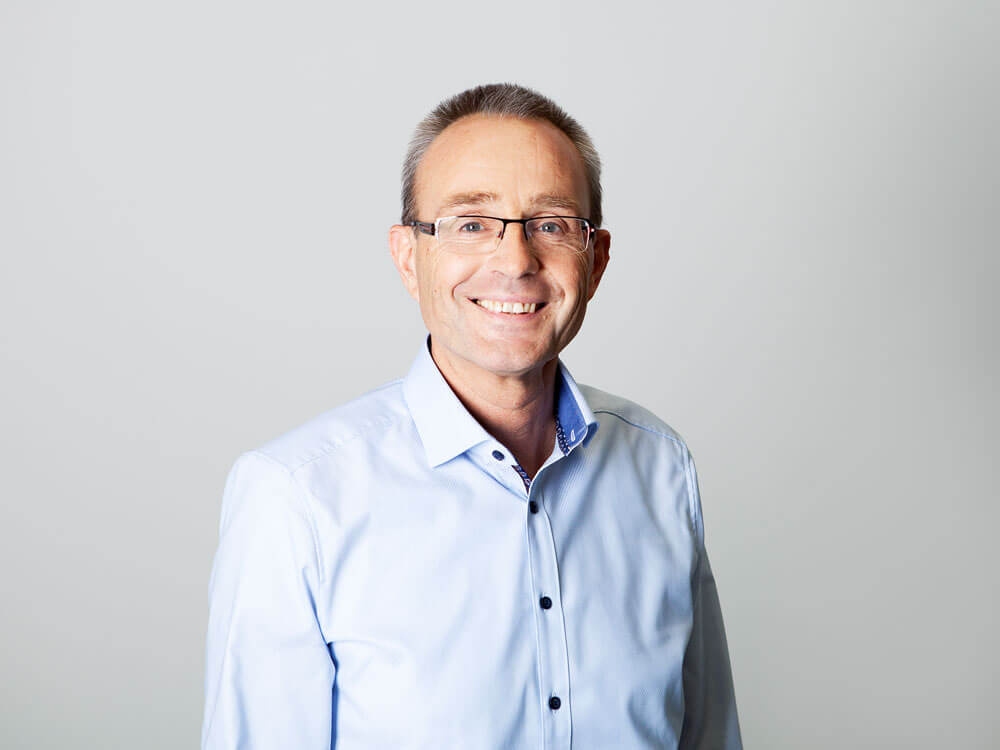
Dr. Gereon Lüdenbach
Managing Director StandZeit GmbH
+49 (0) 2364 60897 -20
What is the aim of a damage analysis?
Why is damage analysis important?
In today's industrial world, where the integrity and reliability of components are of critical importance, failure analysis plays a central role. Effective failure analysis is crucial to understanding component failure and preventing future damage, ultimately helping to increase the efficiency and safety of products. This guide provides an in-depth look at the objectives, methods and benefits of systematic failure analysis.
The primary goal of failure analysis is to determine the direct and hypothetical cause of damage to a component and to understand the reasons for its failure. A thorough failure analysis helps to identify the root cause of damage and thus to take targeted measures to avoid similar damage in the future. It also provides valuable insights into the microstructural changes caused by design flaws or anticipated service loading.
What are the benefits of systematic failure analysis?
There are numerous benefits to systematic failure analysis. It enables a precise determination of the cause of damage and promotes knowledge management within a company by collecting data and insights from previous damage events. This improves the comparability of different failure analyses and supports the technical optimization of vulnerable components. Ultimately, a well-founded analysis helps to improve production and reduce downtime.
How can failure analysis help to prevent future damage?
By identifying the cause of the damage and understanding the conditions that led to it, companies can take preventive measures to avoid future damage. This can be done, for example, by exchanging components or making technical improvements so that they can withstand the expected stress. Thus, failure analysis not only provides insights into past events, but is also a tool for continuously improving product quality and reliability.
What is the process of failure analysis?
What steps are included in a systematic failure analysis?
The failure analysis process involves several systematic steps. First, the damage is documented and a hypothetical cause of damage is established. This is followed by an examination of the component to analyze the microstructural and material changes. The final failure analysis is supplemented by an evaluation of the examination results, which is often in line with VDI guideline 3822 to ensure comparability and precision of the analysis.
How is a cause of failure determined?
Determining a cause of failure is done through a combination of visual inspections, material testing, and analytical methods. The goal is to identify the primary and secondary cause of failure and understand the entire failure picture. This process often involves examining microstructures and analyzing materials to determine if the damage was caused by corrosion, material fatigue, or other factors.
What role does VDI Guideline 3822 play?
VDI Guideline 3822 often plays a central role in the context of failure analysis because it provides standards and guidelines for conducting a systematic and comparable analysis. This guideline helps engineers and technicians to apply a consistent methodology when examining and evaluating damage, which leads to more reliable and comprehensible results.
What methods are used in the damage investigation?
Which investigation methods are suitable for metallic materials?
For metallic materials, non-destructive testing methods are used in particular for failure analysis in order to maintain the integrity of the material. X-ray fluorescence analysis, electron microscopy and spectroscopy are among the most commonly used methods. These techniques enable a detailed examination of the material composition and microstructures to identify possible anomalies and damage.
How is materials testing carried out?
Materials testing is an essential part of damage analysis and is usually carried out in specialized laboratories. It includes both mechanical tests, such as tensile and compression tests, and chemical analyses. These tests help determine the strength, elasticity and resistance of materials under different conditions in order to identify weak points and potential causes of damage.
What techniques are used to identify corrosion damage?
Specific techniques such as electrochemical impedance spectroscopy and potential measurement are used to identify corrosion damage. These methods help determine the corrosion rate and the protective effect of surface coatings. Through targeted analysis, the causes of corrosion damage can be identified and suitable countermeasures can be developed to extend the service life of the components.
How can the results of a damage analysis be used to prevent future damage?
What measures can be taken to prevent the causes of damage?
Various measures can be taken to prevent the causes of damage, including adapting the design and materials, implementing preventive maintenance strategies and monitoring operating conditions. The results of a damage analysis provide valuable information that makes it possible to address specific weak points and improve the function of the component.
How does damage analysis affect the function of the component?
Failure analysis has a direct impact on component function by identifying and addressing potential failure modes. It can be used to correct design flaws, optimize material selection, and adjust manufacturing processes to improve component performance and durability.
How can vulnerable components be technically optimized?
The technical optimization of vulnerable components is achieved through a combination of design adjustments, material improvements and innovative manufacturing techniques. A thorough failure analysis provides the data needed to make targeted changes that increase the resilience and reliability of components. Through continuous monitoring and adjustment, companies can ensure that their products meet the highest quality and safety standards.
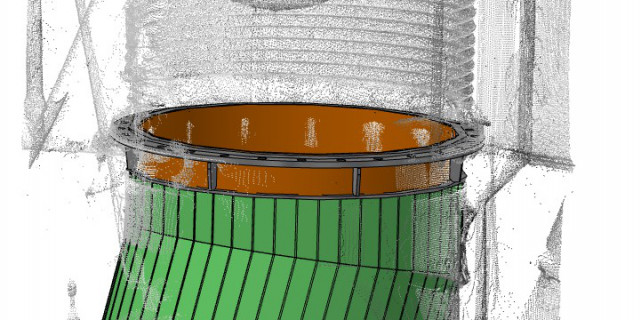
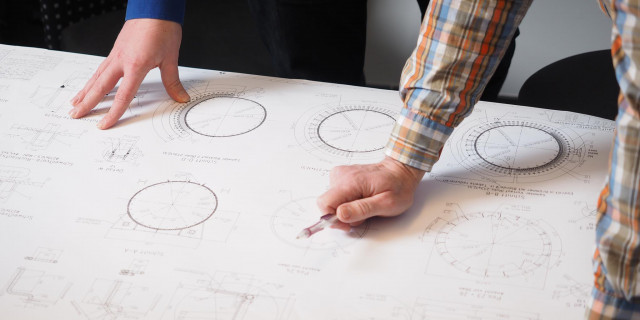
Analysis and advice
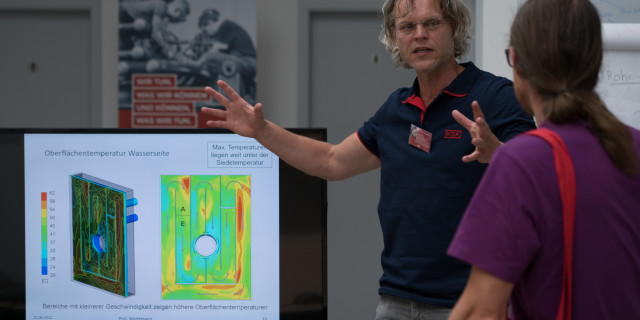
CFD Simulations
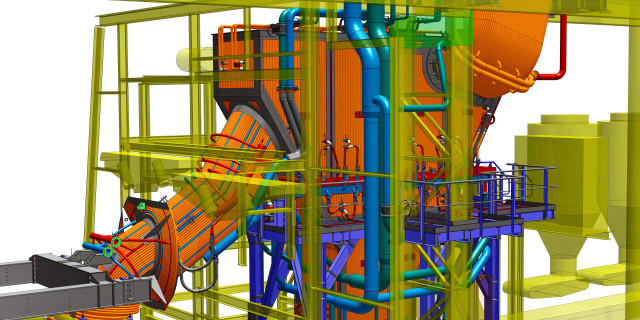
Conceptual Engineering
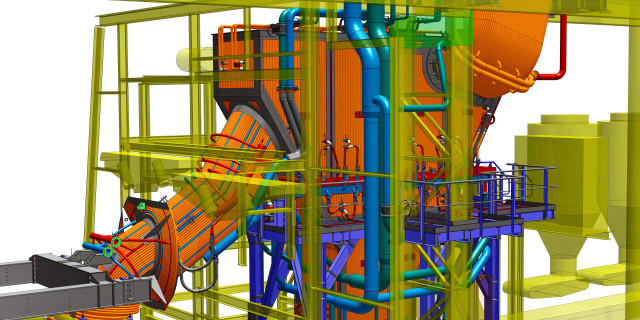
Conceptual Engineering
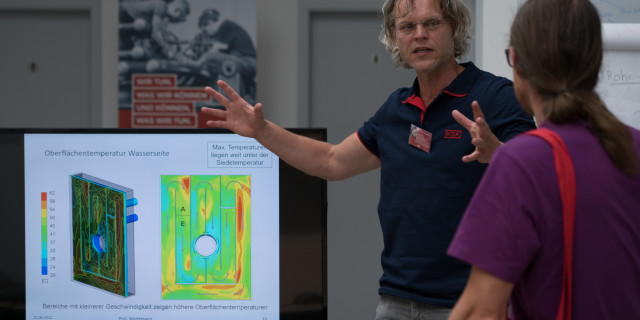
CFD Simulations
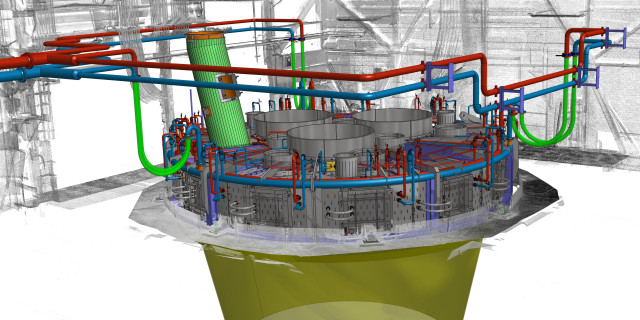
Konstruktionsbüro
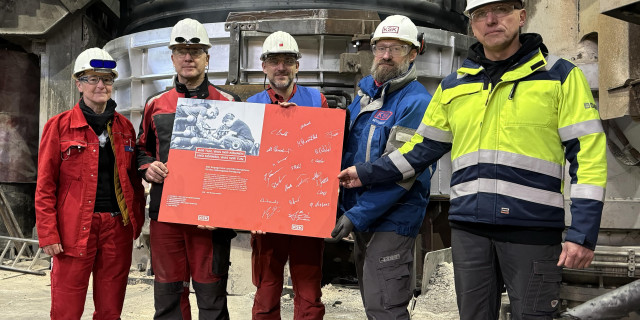
Inbetriebnahme von Anlagen
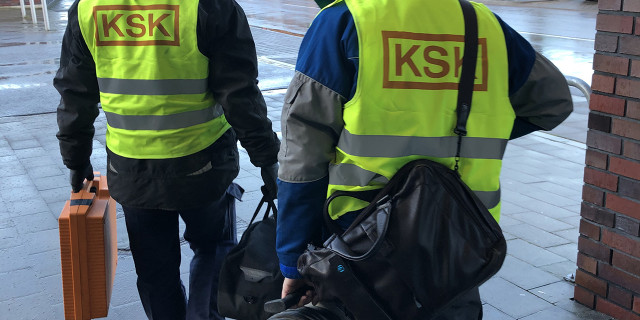
Project management
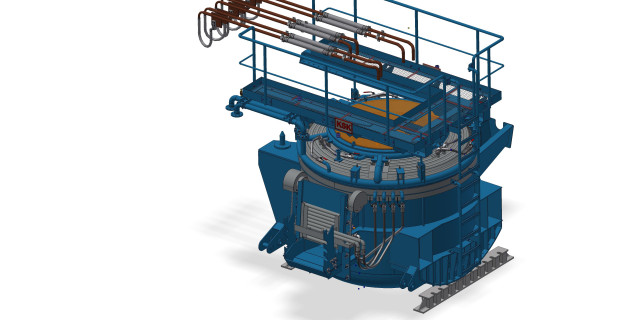
Reverse Engineering
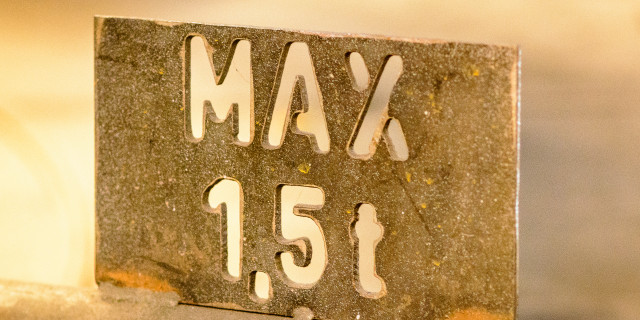
Safety Engineering
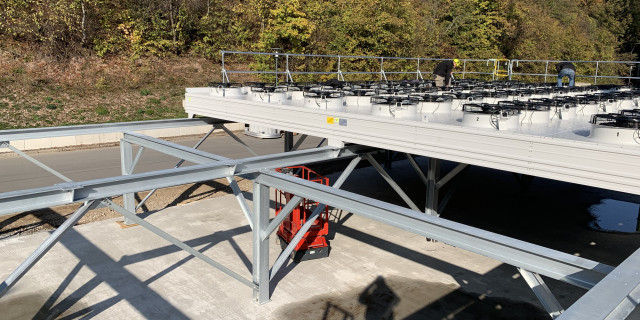
Stahlbau-Statik
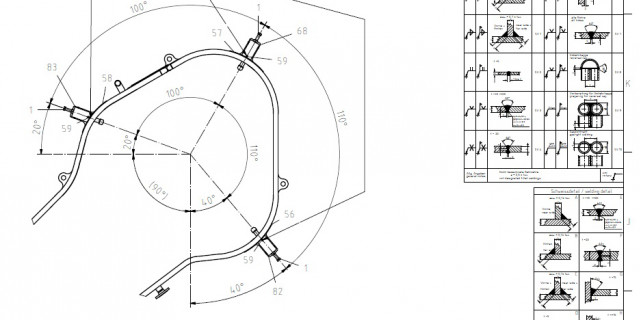
Technische Dokumentation
Table of contents
- Q: What is the goal of a failure analysis?
- Q: How is a failure analysis systematically carried out?
- Q: What role does VDI guideline 3822 play in damage analyses?
- Q: Why is determining the cause of damage important?
- Q: What investigative methods are used in failure analysis?
- Q: How does failure analysis help prevent future damage?
- Q: What are typical causes of component damage?
- Q: How can the findings of a failure analysis be used?
- Q: In what context is a failure analysis carried out?
Q: What is the goal of a failure analysis?
A: The goal of a failure analysis is to determine the cause of the failure and to develop measures to prevent future failures. This is done by systematically examining and evaluating the failure in order to restore the function of the component and to derive preventive measures. An essential part of the failure analysis is the collection and evaluation of data, which can include both qualitative and quantitative aspects. This includes examining the operating conditions, analyzing material properties and evaluating design and manufacturing processes.
The investigation often involves techniques such as visual inspections, non-destructive testing, microscopic analysis and chemical analysis. These methods help to determine the nature and extent of the damage and to identify possible causes such as material fatigue, corrosion, overloading or manufacturing defects.
Once the causes of the damage have been determined, measures to rectify and prevent them are developed. These may include design changes, improvements in material selection, adjustments to operating conditions, or the introduction of regular maintenance and monitoring programs. The aim is to increase the reliability and lifespan of the components and minimize the risk of future failures.
Another important aspect of failure analysis is the documentation of the results and communication with all relevant stakeholders. This ensures that the knowledge gained is used effectively to achieve continuous improvements in product quality and operational reliability.
Q: How is a failure analysis systematically carried out?
A: A systematic failure analysis typically follows a defined process that includes determining the direct cause of the failure, examining the affected component and evaluating the influencing factors. Various investigative methods such as materials testing are used. A systematic failure analysis typically follows a defined process that includes determining the direct cause of the failure, examining the affected component and evaluating the influencing factors. Various investigative methods such as material testing, non-destructive testing and microscopic analysis are used.
The process usually begins with a thorough visual inspection of the damage to obtain initial information on possible causes. Non-destructive testing methods such as ultrasonic or X-ray examinations can then be used to identify internal defects or material flaws without further damaging the component.
Material testing, such as hardness tests or tensile tests, provide valuable information about the mechanical properties of the affected material. Microscopic analyses, including scanning electron microscopy (SEM) or light microscopy, enable a detailed examination of the material's microstructure and can provide information about corrosion, cracks or deformations.
An essential part of the failure analysis is also the consideration of the operating conditions and the environment in which the component is used. Factors such as temperature, pressure, chemical influences or mechanical loads can significantly contribute to the damage event. By evaluating these influencing factors, conclusions can be drawn as to whether the damage was caused by material fatigue, overload, chemical corrosion or other mechanisms.
Finally, a comprehensive report is prepared that summarizes the results of the analysis and provides recommendations for preventive measures. These may include changes in design, material selection, maintenance strategies or operating conditions to avoid future damage and extend the service life of the component.
Q: What role does VDI guideline 3822 play in damage analyses?
A: VDI Guideline 3822 provides a framework for the systematic performance of failure analyses. It helps to ensure the comparability of different failure analyses and supports the determination of the causes of failure using standardized procedures. VDI 3822 places particular emphasis on a structured approach, from data collection and damage description to cause analysis. The main components of the guideline include:
1. documentation of the damage: a comprehensive collection of all relevant information, including environmental conditions, operating parameters and previous damage.
2. Description of the damage: A detailed description of the damage, including the type of damage (e.g. cracking, corrosion, deformation), the materials affected and the localization of the damage.
3. Analysis of the causes of the damage: Application of analytical methods to identify the physical, chemical or mechanical causes of the damage. This can be done by laboratory tests, simulations or other technical analyses.
4. Evaluation and documentation of the results: Compilation and evaluation of the findings in order to draw clear conclusions about the causes of damage and possible preventive measures.
5. Recommendations for action: Development of recommendations for action to avoid future damage. This may include the modification of design features, the change of materials or the adjustment of maintenance intervals.
The application of VDI guideline 3822 is particularly important in industry, as it provides a standardized approach to improving the reliability and safety of technical systems. By systematically analyzing damage events, companies can not only better understand the causes of failures, but also gain valuable insights into how to optimize the service life and performance of their products.
Q: Why is determining the cause of damage important?
A: Determining the cause of failure is crucial to taking targeted action to prevent future failures. Only by understanding why a failure has occurred can preventive measures be effectively planned and implemented. Failure mode analysis makes it possible to uncover weaknesses in the system and address them in a targeted manner. It is important to consider all relevant factors that could have contributed to the failure. This includes technical aspects as well as human error or organizational deficiencies.
To conduct a thorough investigation, various methods can be used, such as failure mode and effects analysis (FMEA), cause-and-effect diagrams, or the 5 whys method. These approaches help to systematically identify and evaluate the underlying causes.
Once the causes are clearly defined, concrete measures can be developed to prevent similar incidents in the future. These may include improving processes, training employees or investing in new technologies.
It is also crucial that the lessons learned are documented and shared with all relevant stakeholders. This is the only way to ensure that the entire company benefits from the insights and that continuous improvement takes place. In the long term, this approach not only helps to prevent damage, but also strengthens the resilience and efficiency of the organization as a whole.
Q: What investigative methods are used in failure analysis?
A: Various investigative methods are used in failure analysis, including microstructure analysis, materials testing, and corrosion testing. These methods help to identify the causes of damage and prevent component failure. Various investigative methods are used in failure analysis, including microstructural analysis, materials testing and corrosion testing. These methods help to identify the causes of damage and prevent component failure.
Another important aspect of failure analysis is fractography, which involves examining the fracture surfaces of damaged components. By taking a close look at the fracture surfaces, conclusions can be drawn about the type of load and the failure behavior of the material. This is particularly helpful in distinguishing between brittle and ductile fracture behavior.
In addition, chemical analysis plays an important role. By examining the material composition and identifying impurities or unwanted phases, potential weak points in the material can be revealed. These findings are crucial for making improvements in the manufacturing process or in the selection of materials.
Non-destructive testing (NDT) is also an essential part of failure analysis. Techniques such as ultrasonic testing, radiography or magnetic particle inspection make it possible to detect internal defects without damaging the component. These methods are particularly useful for regular inspection and maintenance of safety-critical components.
In summary, these inspection methods provide valuable insights into the causes of damage and help to increase the service life and reliability of components. By systematically applying these techniques, engineers can develop improved designs and ensure safety in various industries.
Q: How does failure analysis help prevent future damage?
A: Failure analysis helps to develop targeted measures to prevent further damage by using the knowledge gained. By replacing or adapting vulnerable components, future damage can be avoided. In addition, failure analysis enables continuous improvement of existing systems and processes. By identifying weaknesses and risk factors, companies can proactively take measures to increase the reliability and longevity of their products or systems. This not only reduces maintenance costs, but also increases customer satisfaction and improves the company's reputation.
Another advantage of failure analysis is the opportunity to learn from past mistakes and to incorporate the acquired knowledge into the development of new products. Thus, failure analysis not only helps to prevent damage, but also promotes innovation and sustainably optimizes product quality.
Overall, failure analysis is an important quality management tool that helps companies remain competitive and sustain their market position in the long term.
Q: What are typical causes of component damage?
A: Typical causes of damage to components can be design flaws, inadequate manufacturing processes, overloading or corrosion. A systematic failure analysis can determine the primary and secondary causes of damage and help develop targeted measures to prevent damage. Various analytical methods are used to identify the causes of failure. Commonly used methods include visual inspections, material analyses, non-destructive testing methods and computer-aided simulations.
An important step in the failure analysis is the precise documentation of the damage and the environmental conditions. This includes recording temperature, humidity, load history and other relevant factors that could have contributed to the development of the damage.
Once the causes of damage have been determined, appropriate corrective measures can be implemented. These include optimizing the design, improving the choice of materials, adapting the manufacturing processes or using protective coatings against corrosion. In addition, regular maintenance and inspection intervals can be defined to detect and prevent future damage at an early stage.
Ultimately, a thorough failure analysis not only helps to extend the service life of components, but also to increase the safety and cost-effectiveness of plants and systems.
Q: How can the findings of a failure analysis be used?
A: The findings of a failure analysis can be used to improve knowledge management and optimize manufacturing processes. By systematically evaluating the data obtained, companies can continuously improve their products and processes. The results of the failure analysis provide valuable insights into weaknesses and inefficiencies within existing systems. By identifying common sources of failure, targeted measures can be taken to increase product quality and reduce production costs. In addition, the analysis enables better prediction of potential risks, leading to a more proactive approach to product development.
Another advantage of failure analysis is that it promotes a learning culture within the company. Employees can learn from the results and integrate these insights into their daily work. This not only strengthens individual knowledge but also contributes to the collective intelligence of the organization.
Furthermore, failure analysis can provide the basis for innovation. By understanding why and how failures occur, companies can develop new, improved solutions that not only address existing issues but also meet new market demands. In this way, failure analysis becomes an integral part of a comprehensive quality management system that contributes to the long-term success and competitiveness of the company.
Q: In what context is a failure analysis carried out?
A: A failure analysis is typically conducted within a technical framework, especially when a component does not withstand the expected level of stress or fails. The process of a failure analysis is documented in a conclusive manner in order to develop future prevention strategies. A failure analysis is typically conducted within a technical framework, especially when a component does not withstand the expected level of stress or fails. The process of a failure analysis is documented in order to develop future prevention strategies.
The first step in a failure analysis is data collection. This involves gathering all relevant information about the failed component, the operating conditions and the circumstances of the failure. This includes technical specifications, operating logs, maintenance histories and environmental conditions.
This is followed by a visual inspection of the component to identify initial indications of the cause of the failure. During this process, damage, cracks, discolorations or deformations are documented. Non-destructive testing methods such as X-rays or ultrasound examinations are often used to uncover hidden damage.
After the visual inspection, a detailed material analysis is carried out. This may include chemical analysis, metallographic examination and mechanical testing. The aim is to identify material defects such as inclusions, corrosion or unexpected material fatigue.
At the same time, a root cause analysis is carried out to determine the exact reasons for the failure. Methods such as fault tree analysis or failure modes and effects analysis (FMEA) can help to systematically identify and evaluate possible causes of failure.
Finally, all the results are compiled and documented in a report. This report not only contains the identified cause of failure, but also recommendations for improving the design, choice of materials, manufacturing processes or maintenance strategies to prevent future damage.
The findings from the damage analysis are incorporated into the development of preventive strategies aimed at increasing the reliability and lifespan of components. These include, among other things, the introduction of improved quality controls, the adaptation of operating guidelines or the training of personnel in the early detection of signs of potential failures.
Ihr Ansprechpartner (KSK)
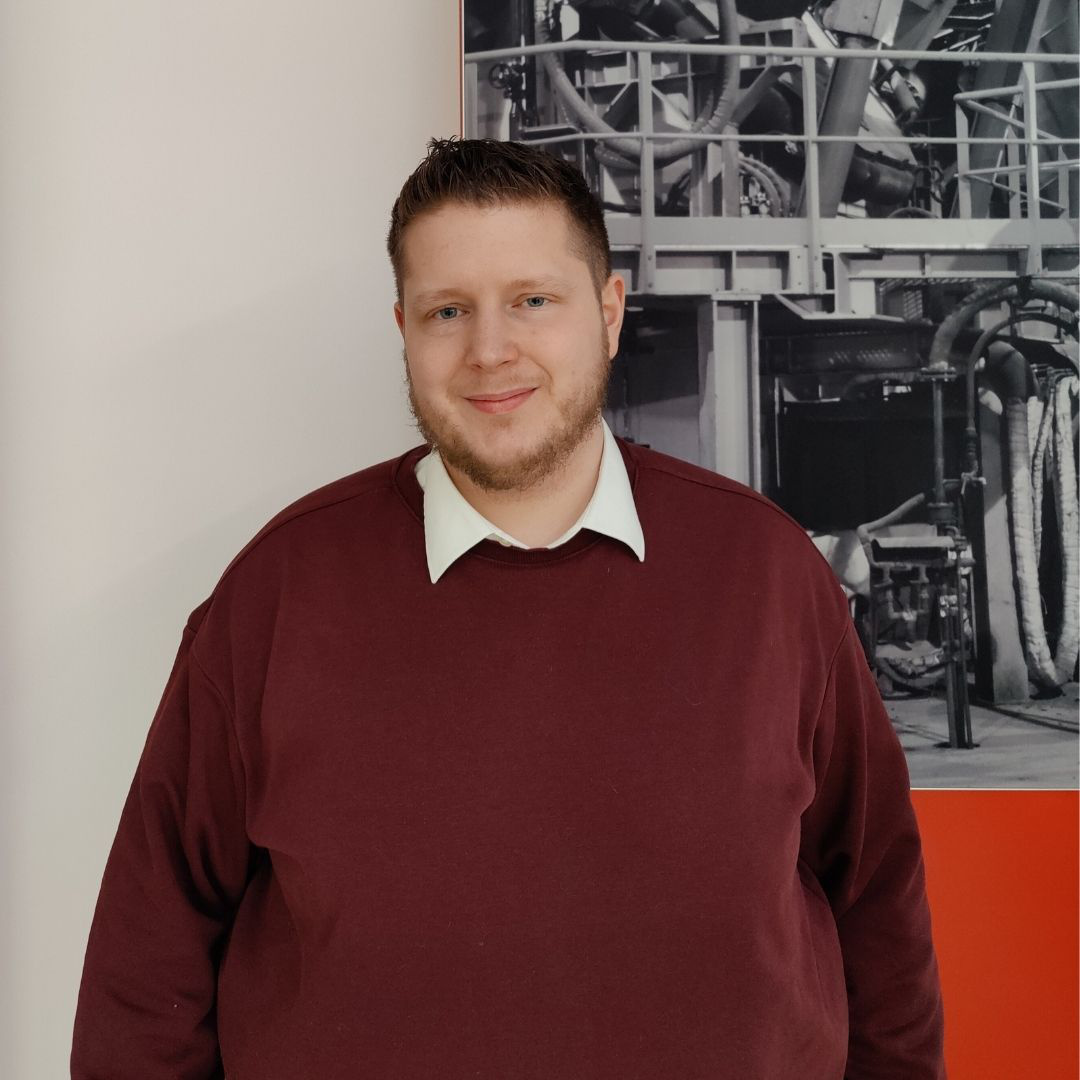
M.Sc. Björn Brüningk-Weißhar
Head of Engineering
Ihr Ansprechparnter (StandZeit)
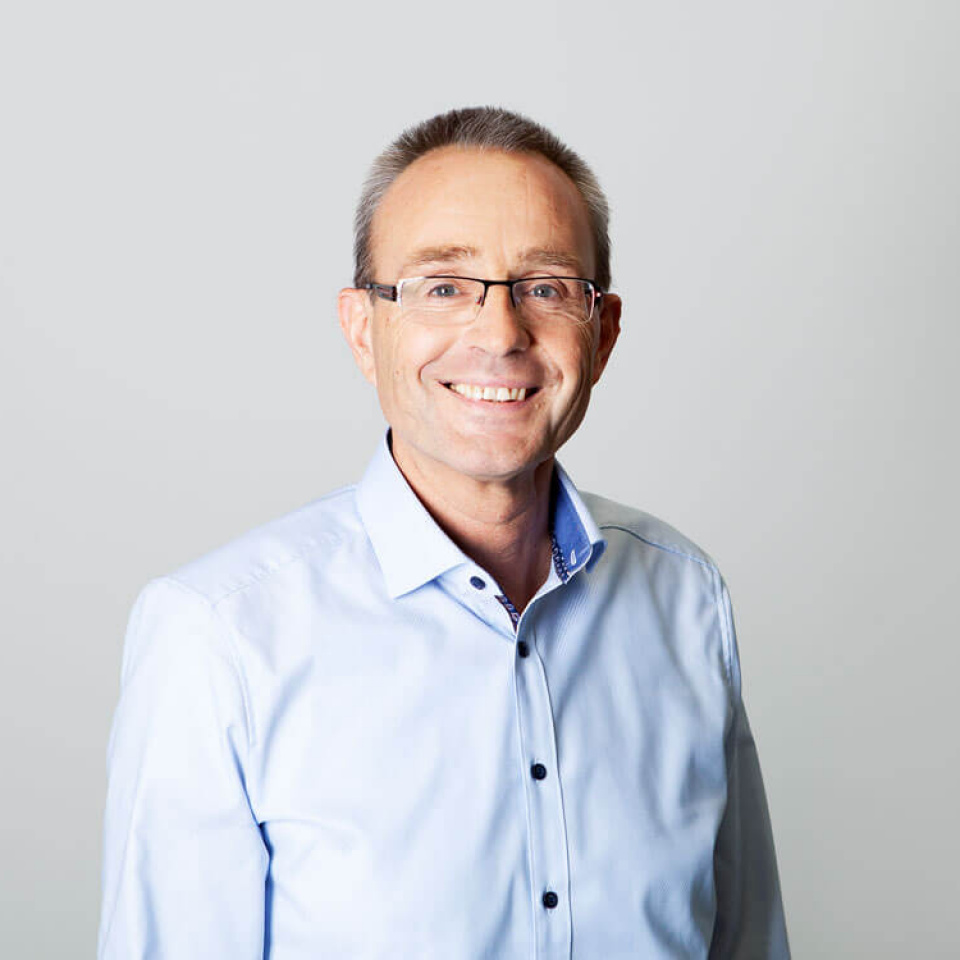
Dr. Gereon Lüdenbach
Geschäftsführer StandZeit GmbH